Closing the gap between design and performance
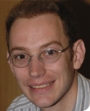
There is a world of difference between buildings that are designed to achieve low carbon emissions and those that actually deliver that intent. David Bleicher stands back from the problem.
Buildings use an awful lot of energy, and everyone agrees they ought to use less. Smart designers are always on the lookout for ways to reduce energy use without resorting to high-profile, high-tech gadgets. Sure, renewables have their place, but there are plenty of passive energy-efficiency measures that are more cost-effective, less prone to failure, and which really should be considered first.
Things like solar shading to reduce heat gains in Summer, variable-speed drives on AHU fans and presence-controlled lighting are now commonplace as a result of the CO2 targets built into Part L. But that isn’t the topic of this article. It’s about something that costs very little, but requires that we change the way we’ve been doing things.
There is a gap between the people who design, construct and commission buildings, and those who manage them, maintain them, and live or work in them — and that gap can lead to buildings using more energy than they should. Here are some things that can be done on any project to help close that gap.
Think about how the building will be used.
Certain building-services solutions suit certain buildings. Underfloor heating is great, but if it is in a room that is unoccupied for much of the day, it will not deliver the energy benefits. Biomass boilers are great, but unless you’ve got the staff who know how to maintain them, they will end up being forgotten about.
Set realistic energy targets.
SBEM is a tool for assessing compliance with Part L and producing the Energy Performance Certificate. It will give you a result in kilograms of carbon dioxide per square metre per year, but it will not be much use when it comes to benchmarking real-life energy performance.
Instead, build a proper model that takes into account process and ‘plug’ loads as well as regulated energy use, hours of occupancy for each space, shading provided by trees in the Summer, and the exact plant items installed, not just generic ones selected from pull-down menus.
Alternatively, benchmark your building against others of similar age and type. The Government’s £8 million programme for evaluating the performance of domestic and non-domestic buildings is seeking to popularise cradle-to-occupation energy modelling using a new version of CIBSE’s Energy Assessment Tool, TM22. This spreadsheet tool has long provided a systematic framework for undertaking an energy analysis. The latest version enables benchmarking of targets and results using Display Energy Certificate benchmarks, CIBSE TM46 benchmarks, or benchmarks from a client’s property portfolio. TM22 is an excellent aid for operational feedback and makes energy analysis from the early stages of design simple, unambiguous and robust.
Specify controls that the operators and users can understand.
The headmaster of a new school told us, ‘In the old school we had a caretaker for 20 years who knew it intimately and kept it going with chewing gum and string. We come in here, and we don’t have a clue. We have a very complex BMS to try and make it run, we’ve got sprinklers we’ve never had before, and we have a very sophisticated fire-alarm system that we've never had before. So the leap is a huge leap for us.’
Sometimes old-fashioned, intuitive, manual and analogue controls are what’s called for; at other times BMS is king. But any controls system has to be procured to suit the needs and capabilities of the end users, otherwise it will be wasted on them, and the building will likely spend years ‘running wild’.
Enable effective energy monitoring.
You cannot improve what you do not measure, which is why all new buildings have sub-metering — in theory. In practice, sub-meters are often missing, located in places where they cannot be read, or failing to communicate with the BMS. They are often incorrectly specified so they are lumping together energy uses that should really be separated, or they are giving bogus readings because they were never commissioned. The basic rule is not to trust any sub-meter readings until they have been calibrated, reconciled with main meters, and are reporting reliably. Meters tend to be prone to all sorts of failures and inaccuracies. This is especially true of heat meters. It is not enough to install them merely to comply with Part L. They need to be rigorously commissioned, checked and zeroed before they can be an operational tool for the building’s managers.
Provide instructions.
Buy a new camera, or a DVD player, and it comes with a booklet telling you what all the buttons do, how to look after it, and what to do when something goes wrong. In addition to the O&M manuals, buildings need two separate sets of instructions: a building manual for the people who manage and maintain the building; and a user guide for the occupants. The former tells you things like where the incoming power supplies can be isolated and what the operating procedures are for the chilled water pumps. The latter tells you when it is appropriate to close the blinds and who to talk to when there’s water dripping from the ceiling. BSRIA’s publication ‘BG 26/2011 Building manuals and building user guide’ gives guidance and templates.
Fine tune.
Commissioning traditionally focuses on achieving correct air and water flow rates, but this is not a guarantee that occupant comfort will be achieved. Ideally, seasonal commissioning should be carried out to ensure specified requirements are met during peak (Winter and Summer) and off-peak (Spring and Autumn) conditions. This process should be an on-going process until the building’s teething troubles have all been ironed out.
David Bleicher is publications and training manager at BSRIA.