Guiding principles for a part-load future
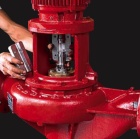
Peter Wolff, UK business development director at Armstrong, highlights best-practice tips for variable-speed, variable-volume HVAC systems.
HVAC systems the world over operate at between 10 and 60% of their design load for 90% of the time (Fig. 1), but many of the approaches to system design employed today have failed to adapt to a part-load mindset. Specifying variable-speed pumps over constant speed in piped systems is just the beginning. To combine lowest possible energy consumption with lowest installed cost, the variable-speed system must avoid the following pitfalls.
• Under-exploitation of the carbon-reduction and cost-saving potential of the technology.
• Compromised efficiency/cost due to changes during the project or after installation.
• Increased cost and loss of efficiency due to system complexity.
• Unnecessary upfront spend and wasted space in the plant room.
• Higher than necessary lifecycle costs.
Asking the following questions, however, can identify overlooked opportunities and prevent future problems
1. Will the system design harness the benefits of demand-based control?
2. Is the operating point for each pump at the optimum point on each curve?
3. Has the risk of inefficiency been removed from the system design by reducing system complexity and ‘variables’?
4. Have all of the opportunities to take cost out of the installation been explored?
5. Could physical footprint be reduced?
6. Can lifecycle costs be reduced?
![]() |
Fig. 1: Everywhere in the world, building-services plant operates at 10 to 60% of design load for 90% of the time. |
1: Will the system design harness the benefits of demand based control?
Traditionally, plant is sized for design-day conditions, but these conditions are rarely experienced in temperate climates. A part-load mindset involves matching boiler load and pump sizes to the building demand rather than to maximum capacity. This thinking needs to be applied across all aspects of system design, including the sizing of equipment, the choice of operating temperatures and the control of key components.
For example, over 90% of the system designs we see incorporating condensing boilers are designed for 80/70°C (meaning they will never condense) whereas they should actually be operating below dew-point — ideally 50/30°C. The difference in efficiency can be as much as 10%, depending upon boiler type and load. In addition, condensing boilers are at their most efficient at part load, so sequencing them at peak load actually switches them at their least-efficient point. A more effective strategy is to run all multiple condensing boilers simultaneously at their lowest possible load to meet the building demand.
2: Is the operating point for each pump at the optimum point on each curve?
Traditionally, the operating point for a pump is wherever the pump performance curve intersects the system resistance curve. As Fig. 2 illustrates, however, efficiency can be increased by placing the operating point where the pump performance, system resistance and control curves converge.
This is possible using demand-based sensorless control, which drives efficiency automatically using a variable-speed pump with integrated inverter. This technology has been around for more than a decade, but its capabilities are such that (in the case of the Armstrong IVS variable speed pump range) it complies with new European pump-efficiency legislation through to 2017.
![]() |
Fig. 2: Less pump power — setting the operating point. S1 is the curve for a pump controlled by throttling the flow. S2 is the curve for a system with sensorless control reducing the speed of the pump in response to reduced flow, thereby reducing power consumption. |
3: Has the risk of inefficiency been removed by reducing system complexity and ‘variables’?
Sensorless technology can also take elements of risk out of a system design. Automatic control of pump speed by integrated inverter eradicates the cost and guesswork of installing differential-pressure sensors. In addition to the energy savings (estimated at 35% compared to a sensor in the plant room) there are significant savings in installation and commissioning costs, as described below.
Further ‘variables’ include changes in operational requirements, either during the design process (involving costly redesigns) or after installation (because of changes in occupancy, alterations of building design, or modifications in the shade conditions due to changes in the building’s surroundings. New pump models (such as the Armstrong Design Envelope IVS pump), however, can provide a wider operational range without compromising efficiency, as shown in Fig. 3.
4: Minimising installation costs.
Labour and groundwork costs can be minimised by hanging vertical inline pumps from the pipework. This method eliminates the cost of inertia bases, springs, flexible pipe connectors, field grouting and alignment. Sensorless pumps can also eradicate the need for differential-pressure sensors and the resulting installation costs, saving an estimated £950 in installation wiring and sensor costs and £200 per pump in commissioning costs.
5: Physical footprint.
Using space-saving pump accessories (such as Armstrong suction guides and Flo-Trex valves) can free up valuable space in the plant room by performing multiple functions with a single component.
6: Maintenance issues.
Split coupled pumps featuring external seals can deliver significant reductions in maintenance costs by enabling all mechanical seal components to be withdrawn for servicing without the need to disturb other pump components or the motor connection.
In conclusion, variable-speed variable-volume systems have become the new baseline technology for our industry. Achieving an edge over competitors in the coming years, however, will mean mastering new guiding design principles specifically focused on the part-load environment. The most successful systems will be those that exploit each of the technical, environmental and commercial benefits to the full.
Peter Wolff is UK business development director at Armstrong.