Taking the pressure off energy supplies
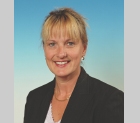
The controversy surrounding soaring energy bills and our creaking National Grid putting increasing pressure on the supply side reinforces the need for better integration of building-services solutions to reduce demand, says B&ES president Sue Sharp.
![]() |
The owner of British Gas has been lambasted in the national press since it announced a £600 million profit on its consumer energy business on the back of a 6% increase in gas and electricity prices for its nine million UK customers.
Household energy bills have doubled in the last five years, and the Government estimates that one in five families are now in ‘fuel poverty’ where they spend more than 10% of their total income on staying warm and keeping their lights on.
Whatever the rights and wrongs behind the way big corporations treat their customers, the new reality is that we are now all subject to a highly volatile energy marketplace. Gas and electricity bills are only going in one direction — up.
At the same time, the country is facing a critical energy shortage. Our ageing coal-fired power stations are all being shut down, removing 11% of our total power generation capacity over the next three years. Attempts to replace capacity with new nuclear power stations and renewables are a long way behind schedule. Energy is becoming a precious commodity with all the associated costs.
Demand
This means we have to address the demand side to try and narrow the looming gap between supply and demand — generating capacity will not catch up in time. This puts the building-engineering sector in prime position because it has the expertise to show building users how to drastically reduce energy consumption.
Buying or refurbishing a building is becoming increasingly fraught as owners and operators wrestle with the cost of energy and the penalties of failing to comply with low-carbon legislation.
The real problem is that every building is a prototype, which is why so many end up disappointing their owners and occupants. The wide range of factors involved (including site location, orientation, size, purpose, number of occupants and technologies used) means that every new or refurbished building presents a different set of challenges to its designers and ultimate operators. We have to look again at how we design building systems with the integration of new and existing solutions at the heart. Buildings, whether new or refurbished, simply have to work better.
While car manufacturers have mastered the art of combining components from various suppliers into a pretty seamless product, building engineers are battling to make boilers from Germany work with control systems from Scandinavia, and solar panels from China integrate with pipework systems forged by various suppliers all over the UK and Europe.
The one thing all the technical solutions have in common is the need for robust commissioning and expert integration.
The issue, at the end of the day, is not how ‘sexy’ a proposed solution is, but what it actually delivers during day-to-day operation. It is not about the technologies you throw at a building, but if your building is warm enough, cool enough, well ventilated and served with adequate hot water? How much does it cost to run?
Manufacturers of building-services technologies are providers of building components. While they can justify claims about their own individual product under laboratory testing conditions, they cannot make any promises at all about how something is going to work once it is installed in a building and linked to many other components.
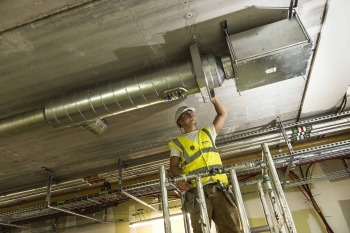
The secret is to keep things as simple as possible and to consider the outcome at the very start of the process. It is very easy to over-complicate, particularly with the range of technology alternatives now on offer. Unfortunately, just when we need things to be simpler they have a tendency to get more complicated. The new systems being deployed to meet climate-change targets can be more difficult for users to understand, and the way these systems work in tandem with a building’s envelope can also be critical.
During the previous decade, it was all about cutting carbon emissions. Now we are far more pragmatic. The truth is that cutting carbon is relatively easy if you can afford to throw renewable technologies at buildings, but that can be very expensive and do little to reduce your running costs. In our economically constrained circumstances, this is no longer a practical or acceptable solution.
Solutions
B&ES is producing an ‘Integrator’s guide’, which is the subject of detailed debate at the CIBSE Technical Symposium in Liverpool (11 and 12 April 2013). It provides the technical detail to underpin strategies for delivering integrated solutions that ensure buildings operate as designed.
Government subsidies and initiatives depend on operational costs being at or close to predicted levels. The Renewable Heat Incentive (RHI), for example, promises building owners generous payments for any heat they generate from renewable systems like biomass boilers and heat pumps. However, to gain these payments the data gathered from the systems must be accurate and usable, which requires the skilled installation of heat meters.
If heat meters are not being correctly installed or calibrated, it will lead to erroneous data that could undermine the RHI payment system. B&ES has also produced guidance on this subject in partnership with the regulator Ofgem. If the systems do not perform as promised then the right level of payments will not be forthcoming, and the whole premise will collapse.
In many cases, rather than installing renewables yourself, it will often prove more cost-effective and practical to link your building to shared systems like large-scale renewables that supply multiple buildings and which are more cost-effective than the individual building-by-building approach.
Using off-site renewables in tandem with thermal storage could overcome the problem of renewables not always producing energy when it is most needed. For example, the Sun might not be shining on your solar thermal system when you need hot water or the wind might not be blowing when you want electricity from your turbine. In simplistic terms, bigger is always better with renewables.
Building-engineering-services firms are at the centre of efforts to ensure technologies deliver their promises and, therefore, the running cost benefits for building owners. Handing over a project should be the start of the process — not the end.
Very few people have the right mix of skills to be able to address this issue, which is why this rapidly evolving energy situation is a great opportunity for suitably qualified, competent building-engineering-services firms.
Sue Sharp is president of the Building & Engineering Services Association (B&ES).