Centralised efficiency
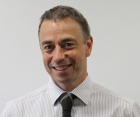
Installing heat-interface units in apartments as part of a community heating system rather than individual boilers opens up the potential for more efficient operation and the use of lower-carbon central plant. Neil Parry of Altecnic discusses how the technology enables consultants and engineers to deliver cost-effective and energy efficient centralised energy centres.
Generating instantaneous hot water via a heat interface unit has long been recognised as one of the most cost-effective and easiest ways to meet the UK’s stringent regulations regarding low-carbon building services. In simple terms, localising a building’s energy centre simplifies the installation of its services infrastructure; rather than a network of gas pipes throughout the building, a single gas supply to the plant-room is all that’s required.
Current flue-design regulations have also made it very difficult to produce a cost-effective system if individual apartment or house boilers are installed, and is another reason why centralising the plant produces the most cost effective overall solution.
So centralising the boilers has clear cost saving benefits, but what about the benefits to system efficiency? Is it more efficient to have larger boilers in one place rather than individual boilers around the building? The simple answer is, yes.
The start/stop cycle of a boiler really impacts on efficiency. Centralising the boiler and amalgamating the demands produces a flatter and reduced demand graph with lower peaks and troughs. This allows the boiler to run more consistently and at a more consistent level, maximising efficiency.
A by-product, and additional benefit, of this more consistent load pattern is a reduction in boiler maintenance.
Most people recognise the efficiency improvements that condensing boilers can give, but how often does a boiler actually condense when a return temperature of over 55°C prevents significant condensation in the heat exchanger? Most heating circuits in the UK are still designed with radiators and have a ∆T between flow and return temperatures of 10 to 15 K. The flow temperature is commonly around 75 to 80°C, giving an average return temperature to the boiler of around 65°C. On start up the boiler may condense quite nicely, but as soon as the building temperature starts to increase, the likelihood is that condensing within the boiler all but stops.
So how can this situation be improved?
Under-floor heating will certainly help, but often this is simply not practical or cost-efficient in a large multi-storey apartment building. Low-surface-temperature radiators can also help, but their size can prohibitive. Architects and tenants alike would prefer not to fill up the rooms with radiators.
Storing DHW in cylinders tends to compound this problem. Once the cylinder is approaching, or at the required temperature, and above 60°C to prevent legionella growth, the return temperature will again be very high and potentially preventing the boiler(s) from condensing, even when the building is cold.

Heat interface units (HIU) address this issue and help reduce the return temperature to the boiler significantly. Depending on the HIU design, even when the unit is on full DHW demand, the return temperature back to the boiler can be as low as 20 to 30°C. This extremely low return temperature, when combined with the hot water, would typically bring the total return temperature down to around 45°C. As a general rule, the lower the return temperature, the more a condensing boiler will condense and the more efficiently it will operate.
Integrating renewable energy sources, such as solar, heat pumps and, even, combined heat and power (CHP) centrally makes sense. The low return temperature ensures the maximum gain from the heat pump or solar system and ensures that the CHP can extract its heat more easily, allowing it to run for longer and produce more valuable electricity.
Boiler maintenance costs are also reduced with these types of systems, as even a building with a hundred apartments would typically only have two or three boilers. As these boilers are located in the plant-room, access is far easier than localised boilers within tenants’ apartments.
Energy metering, logging and software products also ensure that these systems are easy to monitor and simplify tenant billing. MID- and RHI-compliant energy meters installed within the HIU constantly monitor the tenant’s energy use for both heating and DHW production. These data can be then be collected wirelessly, or more commonly, by using a hard-wired MBus system. With these hard-wired systems, the usage data is automatically sent to a centrally located data-logger. This can be accessed periodically by the landlord or building owner and the data used to produce the tenant bills.
Advances in technology continue to make this process easier and more efficient. The latest data-loggers on the market have built in infra-red technology that allows them to communicate directly with a compatible GPRS modem. The two units do not need to be wired together, the information passes between them via infra-red. A mobile network SIM card can then be installed into the GPRS modem, and the system can be set up indirectly via a simple text message sent to the SIM. The modem then sends the usage data daily, weekly, monthly etc. in the form of a csv (Microsoft Excel compatible) file directly to a nominated email address. The latest Internet-based pre-payment systems (gas and electricity) and home energy displays can also be integrated into this system. This new technology allows for accurate billing as well as the efficiency of a building to be monitored in real-time.
Manufacturers are continuing to significantly invest in new technology to deliver effective and efficient community heating systems. It is essential that consultants and architects embrace these advances and utilise them to their full potential if they are to meet the Government’s ever-increasing drive for efficiency, the restrictions on building-services carbon emissions and provide clients with cost-effective energy delivery solutions.
Neil Parry is national specification manager with Altecnic