Building a business case for predictive maintenance
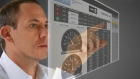
If it ain’t broke, don’t fix it is, perhaps, not the soundest maintenance philosophy, but modern approaches make it possible to plan fixing things just before they might break. Julian Horler of Trane explains.
The traditional approach to heating, ventilating and air-conditioning (HVAC) maintenance relies on a calendar or hour meter to determine when equipment is serviced. But technological advances over the last decade provide facilities managers with information that lets them perform maintenance when it is needed and not when the schedule says it is time.
Predictive or reliability-centered maintenance uses testing, diagnostics and computer modelling to identify actual maintenance needs. This approach hinges on establishing a performance baseline for HVAC systems based on the performance of similar systems. Systems are continuously monitored, and their actual performance is compared to benchmark data. As a result, it is possible to identify potential problems and schedule maintenance before they can cause systems to fail.
![]() |
Predictive maintenance can detect minors issues in a chiller before they become major problems. |
With budgets under pressure and the cost of energy and labour rising, many facilities professionals are increasing their emphasis on predictive maintenance to control costs and reducing the likelihood of an HVAC system failure that could shut down their operations.
Advances in HVAC-related technologies make it possible for many organisations to adopt a predictive-maintenance model without a large capital investment. Most organisations already have the technology backbone in place to enable a predictive approach.
For example, today’s sophisticated building-automation systems are designed to support predictive-maintenance programs, with web-enabled dashboards that make it easy for facilities professionals to gather, access and apply relevant information to keep their building operating efficiently. Most organisations already have highly capable building-automation systems in place. But facilities staffs may need additional training to take full advantage of their features, according to the Platts division of McGraw Hill, which estimates that more than half of facilities departments are under-utilizing their building-automation systems.
HVAC fault detection and diagnostics, such as Trane Intelligent Services, enables predictive maintenance. Intelligent services combine technology, access to existing benchmarking data and sophisticated analytics to continuously collect, interpret and act upon data from building systems and controls to detect and report faults in critical HVAC components, giving technicians early warning of potential problems, improving reliability and reducing unscheduled downtime.
Other predictive-maintenance programs can include methods such as oil analysis to detect minor issues in a chiller compressor before they become major problems.
Thermography can also identify hidden problems in a chilled-water system by detecting and diagnosing the thermal emissions of different components, which could suggest electrical and mechanical issues that can lead to component failure, unplanned outages and safety issues.
![]() |
Thermography can reveal hidden problems in electrical panels and chilled-water systems. |
The latest predictive modelling technologies use computer programs to compare an HVAC system’s operating characteristics with aggregated information from many similar systems. For example, they continuously analyse vibration levels, refrigerants and other fluids, and motor performance to detect potential performance problems, so the facilities department can schedule maintenance and have the required parts on hand.
Many facilities managers seek the help of external professionals to decide if predictive-maintenance is the best approach for their organisation or building. Others have the knowledge and resources to take on this task themselves. In either case, facilities managers will want to start by calculating the true cost of the current approach to HVAC system maintenance.
The average cost of planned and unplanned maintenance over several years is a good starting point. But it is also important to calculate the potential impact of an HVAC system failure on operations. For example, estimate the cost to the facilities budget of responding to an unplanned HVAC failure, including the higher cost of repairs made in a reactive mode.
Next consider the disruption that could have been avoided by proactive predictive maintenance. An unplanned HVAC failure can cause a building to close for hours or even days. Estimate the cost of an unplanned failure in terms that make the sense to the organisation — such as lost revenue, and the impact of an HVAC failure on productivity, customer satisfaction or business reputation.
Many large organisations have most of the technology they need to adopt a predictive maintenance solution. In stating their case, facilities leaders should consider any upfront investment required — including hardware, software, training or changes to existing service contracts. Estimate the savings from eliminating scheduled but unnecessary maintenance tasks, which will offset the cost of implementing a predictive maintenance program.
When all these factors are considered, predictive maintenance is worth considering for most organisations.
Julian Horler is service leader for Trane UK & Ireland.