Biomass advice
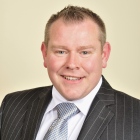
Biomass boilers tick all the right boxes, but achieving maximum benefit from biomass system requires many issues to be considered — says Neville Radford of Hamworthy Heating.
The benefits of biomass boilers in commercial applications are undoubted — dependable, predictable, controllable heat that is eco-friendly and good value. But to reap the rewards you need to prepare thoroughly for the complexities a biomass project presents. With no two biomass projects being the same there are many options to consider.
At Hamworthy we work closely with customers and help them understand what is possible or practicable before they set out on the biomass journey. We will help them to prepare carefully, identify their main priorities and develop the solution accordingly — checking the feasibility of the design to anticipate any potential issues early on in a project, before committing to a design and starting on site.
The biomass boiler model and size, associated fuel and fuelling equipment, buffer vessel etc. need to be selected to suit their location, and together be capable of outputting sufficient power to satisfy the required load cycle. However, as biomass power is related to the type and quality of fuel burnt (wood chip or pellet) and the rate at which this fuel is burnt, consideration must be given early on as to which fuel type to use, as this will affect the boiler type chosen and the size of the storage and feed system.
Fuel selection and storage
Biomass boilers can use either wood chip or wood pellet as the fuel supply, but the quality of the fuel and moisture content is important to maximise the performance of the boiler plant. The availability of suppliers for the chosen fuel type, preferably from within the locality, will be vital to ensure a low carbon footprint for transportation.
Wood pellets are relatively free-flowing compared with the bulkier wood chips, so the storage and fuel handling needs to be able to deal with these factors. If the building doesn’t have enough space to convert part of it into an internal fuel store, then solutions can include bunkers below ground, external silos, hoppers and hook-bin stations.
You will need to ensure there is space for the fuel store and to fit automated mechanical-handling equipment in the plant room, in the form of augers, to move the fuel from the store to the boiler. The installation of an intermediate hopper next to the boiler will reduce the wear and tear on the fuel-feed system and only operate the motors when needed, saving more energy along the way.
Access to the plant room for delivery and installation of the product and on-going fuel supply is also an important consideration. Delivery vehicles may also create disturbance, so considering noise issues is important, for example in residential areas or around buildings such as schools.
We are seeing an increase in demand for biomass packaged plant rooms which contain all the boiler-house equipment and fuel store in a self-contained unit. These can be delivered to site as a completed package and connected to the heating circuit. This removes the challenges of fitting a large boiler and fuel store into an existing plant room and makes installation easier and quicker on site.
Flues
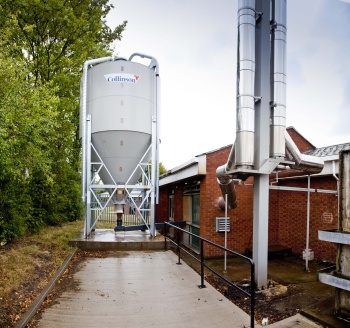
Flues are a vital component for any heating system; they should be considered early on and designed into the project. With biomass boilers the flues need to meet with local regulations on air quality control owing to the emissions released from the burning of wood. The flue needs to expel at least 2 m above the nearest building. Depending on the location of the biomass boiler, the flue system can be complex. In a recent city-centre project the flues had to extend to 28 m to comply with regulations.
Heat metering
The Renewable Heat Incentive (RHI) scheme launched by the Government in 2011 provides generous financial rewards to customers using renewable energy sources, such as biomass boilers, to heat their buildings. To make a valid and continuing claim for the RHI a heat meter compliant with Class 2 of Annex MI-004 of the EU Measuring Instruments Directive (MID) 2004 must be installed.
On simple systems where one biomass boiler provides the heat for a single circuit, a single heat meter needs to be installed in accordance with RHI guidelines to attain an accurate measurement of the heat generated by the biomass boiler. However, on complex systems with multiple heat sources, more than one heat meter may be required to be able to calculate the ‘useful’ renewable heat component that can be used in a legitimate RHI claim — i.e. heat provided solely by the biomass boiler for eligible heating uses. Ofgem must approve the installed heat meters to provide certification for the RHI claim but will only do this after installation, making it vital to put the time and attention in upfront.
Integrated solution
The importance of good project management in this kind of project is clear, and our knowledge and experience enables us to achieve the right outcome in the most effective manner.
It may not be appropriate to deliver the total building heat load through biomass boilers, so integrating with modular gas boilers is a cost-effective way of meeting environmental targets while keeping the investment affordable.
Neville Radford is business development manager — biomass with Hamworthy Heating.