Why do buildings often disappoint their owners?
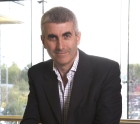
Most commercial building specifiers assume renewable and low-carbon technologies will solve their energy problems, but, as David Frise explains, it isn’t as easy as that.
It is hard for an industry to have to admit that it frequently disappoints its customers. They do say that honesty is good for the soul, so the building-services sector needs to do some serious soul searching.
The CIBSE /RIBA benchmarking exercise CarbonBuzz shows that most new and refurbished buildings consume between 1.5 and 2.5 times predicted values. At a time when buildings are better insulated and individual technologies more efficient than ever, this is a damning statistic.
![]() |
Building owners are becoming increasingly concerned about the commercial risks associated with so-called ‘low carbon’ buildings where performance expectations are not being met. CarbonBuzz encourages users to ‘go beyond compliance of mandatory Building Regulations calculations and refine estimates to account for additional energy loads in use’.
In other words, we have a duty to close the performance gap between design and operational energy performance. However, design engineers are struggling because planning rules and Building Regulations are now in direct conflict, leading to damaging unintended consequences.
Currently it is very tempting to design for planning and forget that the building does actually have to work. Simply bolting a ‘low-carbon’ technology onto a building will leave the operator with an expensive running-cost problem and, potentially, increased carbon emissions. Unfortunately, there is no incentive to make people go back in to see if designs actually do what they say they will.
This situation is compounded by the fact that energy-efficient strategies are poorly understood by most commercial building operators. There is a tendency to focus on technologies and assume that adding renewables or energy-efficient products to a building will solve the problem when all it does is over-complicate things. We buy products at the lowest cost and assemble them, rather than design systems.
The key element is integration. How do technologies work together, regardless of whether they are ‘old’ or ‘new’? How are they operated? What is the overall control strategy for the building? Having a properly thought through strategy means renewables might not be required at all.
The big complication is that every building is a prototype. The wide range of factors involved — including site location, orientation, size, purpose, number of occupants and technologies used — mean that every new or refurbished building presents a different set of challenges to its designers and ultimate operators.
While car manufacturers have mastered the art of combining components from various suppliers into a pretty seamless product, building engineers are battling to make boilers from Germany work with control systems from Scandinavia, and solar panels from China integrate with pipework systems forged by various suppliers all over the UK and Europe.
Manufacturers of building-services technologies are providers of building components. While they can justify claims about their own individual product under laboratory testing conditions, they cannot make any promises at all about how something is going to work once it is installed in a building and linked to many other components.
The secret is to keep things as simple as possible and to consider the outcome at the very start of the process. Conventional gas-fired heating is an example of how the industry has been able to refine its technology to deliver better results, and the task now is to make sure systems are properly commissioned and controlled in operation.
Renewables clearly have a place, but the trick is in making the basic system and fabric as efficient as possible before looking at where an emerging technology might add value. The way these systems work in tandem with a building’s envelope is critical and, often, mysterious. Planning officials and clients need to be presented with a coherent and persuasive argument showing that integration always beats expensive ‘green bling’, especially when it is used inappropriately.
![]() |
Is renewable energy to reduce a building’s carbon footprint a solution or a complication? |
They should also have a requirement to check the installed system is delivering the carbon saving claimed. The planning process should not be a simple tick-box operation. Sadly we seem to believe that because something is installed it works. Merely siting a solar thermal array on the roof of a building is enough to satisfy current planning requirements.
Part of the contractor’s role should be pointing out that things need to be simpler to give the building operator a chance of managing the systems successfully. The new systems being deployed to meet low-carbon targets can be more difficult for users to understand, particularly where multiple controls are used to control multiple systems.
Bringing all this together to deliver systems that work well together and complement each other is also the increasingly important and skilled task of building engineering contractors.
The old saying about peanuts and monkeys has never been truer than today. This lengthy recession has really tightened up budgets for building projects, so it is bound to be tempting to opt for the lowest price when reviewing tenders. However, choosing a contractor solely on price is likely to be much more expensive in the long run. Contractors that go in with low prices just to win work will cut corners, and the eventual outcome is unlikely to be fit for purpose.
Cutting corners is often disguised as ‘value engineering’, which has a nice ring to it but actually has very little to do with value. It is just a euphemism for taking things out of the design to get the initial cost down. With prices constantly under pressure, quality suffers, and procurers should be very wary of dramatic changes in specifications that are clearly attempts to meet unrealistic budgets.
The challenge for clients is differentiating between firms which are capable of providing a skilled service because they have invested in skills and those which will try to squeeze cost out of the project and walk away as soon as they can — leaving them to pick up the pieces and the bill for inflated running costs. Capital costs represent a fraction of the costs of operating a building, so a small saving in the construction phase could have a massive long-term cost.
Any client who seeks value should demand and pay for a ‘soft landing’ service where the handover and ongoing operation of a building project is just as important as the initial construction stage. This way they can ensure any energy-saving strategy is followed through with ongoing commissioning, service and maintenance. Contractor and client can both win this way — but it does require the client to take a long-term view and adjust their budgets appropriately.
To persuade the client that this is worthwhile, contractors must promote themselves as integration experts and have the courage to explain to clients that ‘green bling’ will not do them any good. What they save in capital costs should give them the breathing space to initiate a more joined up energy management strategy to avoid future disappointment.
We will continue to work with ‘old’ technology, as a result, but might have to learn a few new tricks.
David Frise is head of sustainability at the Building & Engineering Services Association (B&ES).