New laws are a boost for hygiene market
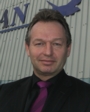
New health and safety powers should stimulate demand for higher standards of ventilation and water hygiene, according to Gary Nicholls.
The new health and safety law that came into force in January 2009 has significantly raised the stakes for employers who put their workforce at risk. The Health & Safety Offences Act 2008 increases the maximum penalties that can be imposed in the lower courts for most health and safety offences from £5000 to £20 000. It also makes imprisonment an option for a wider range of offences. The changes should ensure that businesses who do not take their health-and-safety management responsibilities seriously are more likely to face prosecution. ‘The Act sends an important message to those who flout the law,’ said Judith Hackitt, chair of the Health & Safety Executive (HSE), while adding that good employers and good managers had nothing to fear from it. This has major implications for the hygiene of ventilation and water systems. The market for specialist hygiene suppliers shows little sign of shrinking despite the credit crunch. This is thanks, in part, to increased levels of awareness about the implications of poorly maintained systems as well as the new laws — including those covering fire and corporate manslaughter. These days it is hard for building owners and operators to ignore the risks surrounding airborne bacteria transmitted through buildings by dirty ductwork and water hygiene concerns such as Legionnaires’ disease. Even before the new Offences Act came into force, the introduction of the Corporate Manslaughter Act in 2008 had already made it easier for prosecutors to secure convictions in outbreaks of Legionnaires’ Disease and also in the aftermath of building fires linked to poorly maintained ventilation. Now that the offence of corporate manslaughter has been established, the Government is seeking to back it up with draconian penalties. Organisations found guilty of causing the death of an employee or member of the public could find themselves paying fines which start at 5% of their total turnover; this could amount to millions of pounds in some cases. As well as commercial companies, the act covers a wide range of organisations including local authorities, NHS bodies, Government departments, police forces and some business partnerships. ‘Under the [corporate manslaughter] law you are required to render a piece of equipment safe,’ said Simon Joyston-Bechal, a partner in the firm of solicitors Pinsent Masons. ‘This includes putting in place a suitable maintenance regime. ‘If, for example, fire investigators found that there were no access doors in the ductwork, so making it impossible to carry out proper ventilation cleaning, and this led to somebody’s death in a fire, then the building owner could be guilty of negligence and face prosecution.’ Legal experts have also confirmed that the outcome of recent investigations into outbreaks of Legionnaires’ Disease might have been different if the Corporate Manslaughter Act had been in force. ‘The Barrow-in-Furness case [where seven people died and over 150 were seriously harmed in 2002] is very important,’ said Mr Joyston-Bechal. ‘Prosecutors were not able to find a “controlling mind” behind the outbreak so could not press manslaughter charges against the local authority involved. ‘The new act would make it much easier to achieve a prosecution because you would only have to show that anyone involved had control over a substantial part of the organisation’s activities. This act is creating a whole new landscape for Legionnaires’ Disease prosecutions.’ All this adds up to a serious duty of care for building owners and operators. The legal framework now makes it clear that you must have a strategy for keeping your ventilation and water services safe. Planned, preventative maintenance is the only way to minimise the risk of fires being spread through dirty ductwork and of legionella bacteria thriving in untreated water. Insurance companies are also playing an increasingly influential role in the attitude of facilities managers to maintenance issues. Budgets might be tightening as the economic gloom deepens, but very few people can afford to take the risk of operating without insurance cover. Also, most insurance providers now include clauses in their policies that mean they will not pay out following a fire or other disaster if there is evidence that the services in question were not properly maintained. In the case of ventilation ductwork, this means they must be thoroughly and regularly cleaned to reduce the risk of fire being spread by, for example, grease which has accumulated in extract systems. However, getting proper access to carry out cleaning can be a real headache. In most of the installed systems we survey there are not anything like enough access doors in place. It does not take a genius to work out that if access for maintenance was not addressed when the system was designed, it has probably never been cleaned properly. Expert fire investigators commissioned by insurers and/or law makers will not miss a detail like that during any inquiry in the wake of a serious incident. In most cases, the solution is for the hygiene contractor to put the access doors in himself to get at the blockages or dirty sections of ductwork — and that can be expensive and disruptive for the end user. On the supply side, ventilation components that are particularly prone to rapid build up of harmful airborne deposits include air intake duct/plenums, air-handling units/plant, heat transfer coils (particularly wet coils), humidifiers and surrounds, fan-coil units, fire dampers, internal insulation, floor/ceiling plenums, induction units and filters. A thorough approach is essential to make safe all the potential areas of risk and reduce the risk of contamination that could lead to sick building syndrome or the build-up of grease that increases fire risk. However, some maintenance firms will issue cleaning certificates even if they have only carried out a partial clean. This is not good practice. End users should ensure they are using competent hygiene maintenance firms which can provide proper evidence of their skills and give the user proof they have carried out a full, deep clean. The Heating & Ventilating Contractors’ Association (HVCA) provides a Guide to Good Practice (TR/19) ‘Internal cleanliness of ventilation systems’. This gives comprehensive information about how ventilation systems should be cleaned and how to set up a planned hygiene maintenance programme. It should be used as the basis for any remedial and on-going maintenance programme to ensure ductwork provides an acceptable level of ventilation and removes both health and fire risks. It is also an important weapon for keeping the insurers happy and the lawyers at bay. Gary Nicholls is managing director of building-services-hygiene contractor Swiftclean and chairman of the HVCA’s ventilation hygiene branch.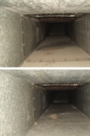