Surpassing Building Regulations with readily available technology
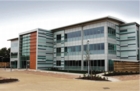
Ken Sharpe finds out how Cunnington Clark bettered the Building Regulations by 10% for little extra cost than other less energy-efficient buildings near the new headquarters of AB Agri.
In the mass of red brick buildings with pitched roofs that dominate Lynch Wood Business Park on the edge of Peterborough, the new AB Agri headquarters stands out for its scale and appearance.
Very much less evident, however, is how much lower its carbon footprint is compared to its neighbours and, indeed, how much it exceeds the requirements of the 2006 Building Regulations for this type of building.
Its carbon footprint is 10% better than required by the 2006 Building Regulations, which makes a sizeable dent on the 25% further improvement that is expected to be required by the next Building Regulations due in 2010. The overall cost was not significantly more than other less energy-efficient buildings nearby.
With the help of M&E services designed by local consultants Cunnington Clark and installed by Adcock Group, also of Peterborough, that energy performance is achieved without the help of renewable sources, which, in any case, is not required by Peterborough City Council. You could regard the air-source VRF energy-recovery air-conditioning installation as exploiting renewable, but that was not the reason for its installation.
The rest of the design team is also based in Peterborough — no doubt reducing the design miles associated with the project. Architects were David Turnock, with Davis Langdon responsible for project management. Civil and structural engineers were Stirling Maynard, with SDC as building contractor.
The developer, Frenbury Properties, is also based in Peterborough. The 2278 m2 building was originally developed as a speculative development, but AB Agri expressed interest at an early stage in using it as a headquarters building.
AB Agri operates at the heart of the agricultural industry with activities that stretch from plough to plate. Its business interests embrace the food, drink and biofuel industry supply chain.
Both the client and developer were interested in a green building, giving David Clark of Cunnington Clark scope to apply expertise accumulated from a number of previous projects.
The philosophy included curbing solar gain to reduce cooling loads and focusing on minimising the energy used by the lighting. Not only is lighting the largest single energy user of the building, but it also adds significantly to the cooling load.
The building has large areas of glazing on its southerly aspect. Two measures have been applied to reduce solar gain. One is the use of translucent glazing at low level on each floor. The other is fixed louvres to protect the facade from direct sunlight in the summer but enable solar gain to be of benefit in the winter.
Energy-efficient fluorescent light fittings with high-frequency ballasts and T5 lamps are used throughout. Downlights use compact fluorescent lamps.
Around the perimeter of the building, lighting fittings in the ceiling are controlled according to available daylight using signals from interior photocells in the ceiling of each window bay. There are PIR motion sensors in office and breakout areas to prevent lighting staying on when the building is not occupied.
The unnecessary use of lighting in areas of the building that are used only occasionally is prevented by using PIR sensors to detect movement and switch lighting on and off. These areas include toilets, stores, meeting rooms, stairwells and breakout areas.
David Clark explains, ‘The most sustainable lighting is natural daylight, and our lighting design sought to maximise natural lighting in the building while maintaining indoor temperature regulation and reducing direct light glare. The lighting systems we have put in place maintain an ambient lighting level of around 400 lux.’
Taking control of lighting loads immediately reduces the potential cooling loads to be dealt with. It also increases the heating loads, but these are more efficiently taken care of by other means.
The mainstay of the heating and cooling installation is a Daikin VRV III energy-recovery installation with separate zones on each floor for the north and south aspects. Heat removed from the south aspect of a floor when cooling is required can be used to heat the north aspect if required, with very little additional energy input.
This VRV system is very flexible and very quick to install, both benefits which were helpful in accommodating changes to room layout and design, even while construction was in progress. Indeed, the whole project was completed from design to fit-out over 11 months — requiring well co-ordinated teamwork among the project team.
The air-conditioning plant is accommodated in a ground-level enclosure which houses seven VRV III outdoor units that can provide 232 kW of total cooling and a separate unit for the building’s server room. Pipework to the building goes a short distance underground and then up through risers. Some redundant pipework is provided to cater for system expansion in the future.
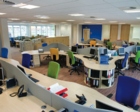
In open-plan areas conditioned air is delivered by fan-coil units in the ceiling with air delivered through circular ductwork to swirl diffusers. Cassette units are installed in meeting rooms.
There are controllers for the air-conditioning system in each space to give users control over temperature but not operating times, which are under the control of a Daikin front end. The central supervisor also provides information about energy consumption and system performance.
Close attention is also given to reducing the energy requirement for ventilation. A Daikin VAM system incorporates energy recovery using cross-flow plate heat exchangers to achieve up to 70% heat recovery. Air is drawn in through vents on the south aspect of the building and delivered at a constant rate.
Taking firm control of the main energy users of the new headquarters of AB Agri enabled the smaller requirements to be dealt without any special measures.
For example, no cooling is provided to the stairwells, and heating is provided by direct-acting electric NOBO panel radiators with local temperature control — but restricted to normal operating hours only. Electric panel heaters also have central time controller located adjacent to the Daikin controller.
Toilet areas are heated in the same way, but with an LST unit in the disabled toilets.
The toilet areas do not have external walls, and David Clark believes that heating is therefore not really necessary. Indeed, he believes he would not install heating into internal toilet areas in the future — especially with tighter Building Regulations.
A neat touch in the toilets in the installation of Dyson Airblade hand dryers. By drying hands more quickly, they should use less energy. On the other hand, more people might use them rather than rub wet hands together as they return to their desks. The proportion of hand dryers to wash hand basins is much better than what is commonly seen — with two dryers for three basins.
Ventilation for toilets is extract only.
Domestic hot water in toilets and break-out areas is provided by a central Heatrae Sadia electric unvented hot water located within the first floor riser with HWS circulating pump. To reduce the use of potable water and the energy needed for hot water, taps at wash hand basins deliver aerated water and all outlets are fitted with Robert Pearson flow regulating and isolating valves.
A further measure to reduce the use of mains water is to harvest rain water and store it in a 12 000 l underground tank. This water is filtered and pumped to a day tank at high level in the building to be used for low-flush toilets.
This headquarters building of AB Agri is all-electric, and there is no mains gas. Electricity is not a low-carbon fuel for heating purposes, but the application of heat-pump technology more than offsets this disadvantage over gas. In addition, the heat-recovery capabilities of the Daikin VRV III system further reduce the electrical energy required for heating. Those savings give sufficient margin to use direct-acting electricity for other services such as domestic hot water and heating stairwells.
But it must be the attention to minimising the electricity consumption for lighting that enables this building to come in 10% better than Building Regulations — both by reducing the electricity consumption for the lighting itself and the side benefit of reducing the cooling load.
Control of the lighting is entirely automatic with the exception of manual override controls to meeting and conference rooms, but the occupants have been given control of the temperature setting of the VRV system and electric panel radiators.
A hot topic in the building-services industry is whether building occupants should be given control over their internal environment so that they feel more comfortable or whether control should be entirely automatic to prevent users wasting energy.
It would be interesting to see what future Energy Performance Certificates show.
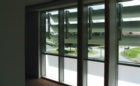