Refrigerant planning will keep plant running
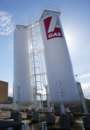
Are you fully prepared for the ban on virgin HCFCs at the end of this year? Ken Logan looks at the consequences of not having a plan and how to be prepared.
At midnight on 31 December 2009 a ban on the use of virgin HCFCs for servicing refrigeration and air conditioning systems will come into effect across all 27 European Union member countries. While there is no legal requirement to remove existing HCFCs from systems, all maintenance and servicing from this date must be carried out with reclaimed HCFCs. Reclaimed HCFCs may be used until 2015, but this date is under review and may be brought forward to 2012.
The use ban is presenting some facilities managers with a dilemma, but developing and implementing a refrigerant-management plan can ensure the successful phase-out of virgin HCFCs while keeping plant operational.
With less than six months before the use ban becomes law many companies are only now waking up to the realisation that doing nothing is not an option. Amidst widespread confusion and complacency, companies are now recognising that they need to act swiftly to comply with the law and ensure a reliable source of refrigerant.
A busy third and fourth quarter is expected by the refrigerant industry as companies in a broad spectrum of industries begin to realise that the use ban is not confined solely to the HVACR and food industries. All organisations involved with air conditioning and refrigeration equipment — from those who only use it in their buildings for cooling to those who rely upon it for manufacturing processes — will be affected.
For facilities managers who are unprepared, the ban on the use of virgin HCFCs could pose a huge logistical challenge particularly if they are responsible for more than one site. According to anecdotal evidence, some larger organisations have been slow to instigate a process to ensure compliance. Complacency is a major obstacle for many.
Some companies may feel that they can put off implementing a course of action until 2015, unless a system is leaking. However, some systems have been poorly designed and are more prone to leaks than others — so even the most rigorous inspections will not prevent leaks.
Action needs to be taken now to ensure that plant can continue running without interruption. There are no short cuts and tasks may include the following.
• Sourcing reclaimed HCFCs or using a refrigerant bank.
• Switching to replacement refrigerants.
• Addressing existing plant issues.
• Investment of capital and training to manage conversion and/or replacement.
• Investigating the consequences non-compliance: i.e. plant downtime.
It is essential to know where you are starting from by carrying out a full audit of your systems. Planning ahead and drawing up a refrigerant-management plan based on accurate inventories of equipment and refrigerant is a sensible strategy and will help ease the transition. Knowing where to start can be a major hurdle for many companies. Those which sub-contract out service and maintenance to third parties should obtain statements identifying the refrigerants used in their refrigeration and air-conditioning systems. If a statement cannot be supplied, contact your refrigerant supplier who will be able to carry out a test to verify whether HCFCs are being used.
To be effective, a detailed plan needs to be drawn up by a designated refrigerant manager, preferably one who can act as a focal point and with the necessary authority and budget to effect change. A full audit is a must so that a full understanding is achieved of what refrigerants are currently used, what plant is involved and whether there any potential problems. In some cases systems may not have been labelled correctly or refrigerants might have been decanted into a variety of cylinders with no clear paper trail to identify what is being used. Many refrigerant suppliers can provide an inexpensive health check to verify what is being held and whether contaminants are present.
A good plan will include the following.
• Equipment inventory.
• Operating and maintenance practices.
• Refrigerant recovery, recycling, and reclamation procedures.
• Refrigerant containment.
• Chiller retrofit or replacement plans.
Large organisations will already have much of this information as part of their service and maintenance schedule, so the task should not be too onerous. What may not already be formally documented is a basic refrigerant-management policy that should clearly show the company's intention to comply with all regulations and should cover the following as a minimum
• Annual refrigerant usage per chiller.
• Life expectancy of chillers.
• Are chillers well maintained.
• How frequently are oil and refrigerant samples tested.
• How much refrigerant is in stock.
• Is there any recovered material that can be reclaimed.
• Are there any alternative refrigerants that could be used.
Once a refrigerant-management plan has been produced, facilities managers are in a better position to assess refrigerant requirements and the potential impact of the ban of virgin HCFCs for their plant. Every plan should provide for equipment containment, conversion, and replacement.
Reclaimed HCFCs may be a viable short-term solution for existing systems in good condition, but factoring costs in to ensure refrigerant containment and future procurement will make the process much easier.
If equipment is to be converted or replaced, its condition, service needs and performance options need to be considered. Aged plant (installed before 2000) may be an appropriate candidate for replacement. Some chillers and AHUs have been known to last up to 25 years thanks to planned preventative maintenance, which can improve overall plant performance and minimise refrigerant loss.
Any refrigerant plan should also include a safety policy to minimise hazards. Proper handling of refrigerant equipment and following correct procedures prevents injuries and minimises hazards.
With less than six months to go, the critical time to act is now. Making prudent long-term capital investment decisions and addressing short-term demands, whilst maintaining equipment and refrigerant assets, should be a major concern for every facilities manager.
Developing a comprehensive plan will guide all affected personnel to effect an orderly transition which will ensure compliance of the regulations while also guaranteeing operational capabilities.
Ken Logan is managing director of A-Gas (UK) Ltd.