Seeing the wood for the trees
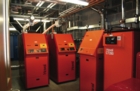
Specifying biomass boilers requires a different mindset to gas- and oil-fired boilers. Do you really know your chips from your pellets? Andy Owens outlines the key considerations.
Over the last few years there has been a huge increase in the use of biomass boilers in a wide range of projects. However, it is true to say that in some cases, where the specifier has lacked experience in biomass, the project has not gone as well as expected. That same lack of familiarity can deter end clients from adopting biomass technology when it is the most appropriate solution. As the Carbon Trust has noted: ‘A lack of customer knowledge and understanding of biomass heating technology is a significant barrier to wider uptake.’ All of which means that anyone specifying, or thinking of specifying, biomass has to look beyond the basic engineering design that would accompany any heating system to evaluate the day-to-day practicalities of living with a biomass system. This holistic approach has proved its value on many biomass projects that we have been involved in. The first stage is to understand the range of heat loads through the year and to design as much as possible for continual load with minimum cycling. For example, is it worth firing a biomass boiler at all if there is only a demand for domestic hot water? Would a suitably sized buffer vessel help the operation of the boiler? A small gas-fired boiler or, perhaps, solar thermal may be valuable additions to the project. It is also important to understand how different biomass boilers deal with variable loads. Some may go into standby without going out, offering a rapid response to a call for heat. Others may go out completely and use auto-ignition to re-fire when required, offering a slightly slower response time. Beyond these engineering considerations is the overall suitability of the site in relation to fuel storage and deliveries — both of which also impact on the choice of wood fuel to be used. In the UK that choice usually comes down to wood chips or wood pellets; both have their place but offer different characteristics. Wood chips undergo less processing than pellets and tend to show greater variation in combustion efficiency and physical size. Crucially, the calorific value and the bulk density of chips is lower than pellets, so higher storage volumes will be required and/or more frequent deliveries than pellets to deliver the same heating capacity. The variable moisture content and size of chips may necessitate more complex, and therefore more expensive, controls to maintain even combustion. However, chips cost less than pellets — though the cheapest chips will usually produce higher volumes of ash, which has implications for everyday maintenance. So there may be a balancing act between fuel costs and convenience. The type of delivery vehicle also needs to be considered. The size of the vehicle will dictate the required dimensions of access routes and turning circles. Chips are generally delivered by a tipper lorry, necessitating below-ground storage and a mechanism (‘walking floor’) for moving the chips out of the way as more flow into the space. A cyclone can be used to decelerate and spread the pellets, but it will occupy some headroom and may reduce the storage volume. Pellets are usually delivered by a smaller ‘blower’ vehicle with less-demanding access requirements. The best results are achieved using a vertical storage silo as this maximises fuel recovery. The silo may be made from GRP (glass reinforced polyester) for outdoor use, or a fabric silo can be assembled in-situ indoors. Because of their height, outdoor silos may require planning permission. The irregular shape and size of chips means they need more robust handling equipment with larger augers and motors, compared to pellets. In addition, the distance from storage to boiler should be as short as possible to minimise damage to the fuel during mechanical handling. If all that is not enough, it is also vital to get the buy-in of the people who will use the boilers. They need to understand how they differ from gas or oil, particularly maintenance aspects. Early engagement with key staff at the client end, combined with regular contact, even after handover, is therefore essential to a successful project. While there is not space here to discuss all the considerations, these examples highlight the need to take an holistic view of any biomass installation. If there is a plentiful supply of wood chips nearby and sufficient storage space on site, these may be the best option — as long as the client understands that the lower fuel price comes with higher maintenance costs, more frequent deliveries and more storage space. In other situations, pellets will be a better option, as long as the silos can be sited in an appropriate position. In all cases the proximity of boiler to fuel storage, vehicle access and the noise of delivery need to be considered. So it really does make sense to call on the expertise of those with considerable biomass experience to ensure that all boxes are ticked. Andy Owens is biomass technical sales manager with Hoval.
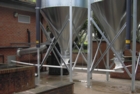