Putting a cost on zero carbon
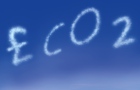
Achieving zero-carbon or low-carbon buildings has a price tag. Dave Cheshire give his perspective on the cost effectiveness of the various options.
The Government has announced its intentions for the zero-carbon definition, but what does this mean in practice?
The consultation on the definition of zero carbon proposed three steps towards compliance.
• The first stage sets a minimum level of energy efficiency.
• The second sets a minimum target contribution from low- and zero-carbon technologies called ‘carbon compliance’.
• A third stage uses on- and off-site ‘allowable solutions’. This last stage is there to make up the difference in CO2 reductions between the first two stages and full zero carbon and includes solutions such as exporting heat to surrounding buildings or contributing towards community heat infrastructure and plant.
July’s written statement by John Healey, MP, confirmed the definition of zero carbon. This included setting the minimum level of ‘carbon compliance’ for dwellings at 70% compared to 2006 Part L; the level for non-domestic buildings has yet to be set. It also proposed a guideline maximum price that they expect the industry to bear to implement ‘allowable solutions’. This has been set at £100 per tonne of carbon dioxide.
Assuming the same definition for non-domestic buildings and capitalising this figure over 30 years gives an equivalent capital expenditure of £3000 per tonne of CO2 emitted per year. So, how does this compare to energy efficiency and on-site renewable technologies?
There are some potentially low-cost passive energy-efficiency measures that require fundamental architectural design changes, such as the following.
• Optimising window sizes to balance daylight with heat gain/loss.
• Providing rooflights and light wells.
• Changing the internal configuration of spaces to ensure areas that have high internal heat gains are positioned towards the north elevations.
If these changes are implemented as part of the design concept, then they could have little or no cost implications. In fact, measures such as optimising window sizes may even reduce the glazed areas and so provide potential savings.
Then there are low-cost active measures, such as lighting controls and improved air tightness which could cost around £2000 to £3000 per tonne of CO2.
Further savings become more expensive, with presence detectors on lighting costing around £5000 to £6000 per tonne of CO2. Costs could rise to £10 000 to 20 000 per tonne of CO2 for advanced insulation standards.
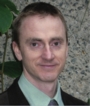
So, assuming energy efficiency compliance is set at an appropriate level, meeting the requirements through low- and zero-cost measures could cost around £2000 to £3000 per tonne of CO2.
The cost of on-site renewable energy costs (‘carbon compliance’) can vary widely depending on the technology applied. Typical costs are around £5000 to £10 000 per tonne of CO2, which makes renewables less attractive compared to the lower-cost energy-efficiency measures or allowable solutions.
On many sites there will be a physical limit to just how much energy can be generated. On a constrained inner-city site, biomass and wind may be ruled out. If the building is overshadowed, there would be limited yield from solar technologies. Ground area may limit the contribution from ground-source heat pumps. On a constrained site it makes sense to move quickly to allowable solutions, but on a site with potential for on-site generation, it may well prove to be cost-effective to exceed the minimum levels of carbon compliance.
The allowable solutions for housing include both further enhancements on-site (e.g. advanced building-control systems to reduce energy use in the home) and off-site solutions to reduce the overall carbon emissions (e.g. investments in low- and zero-carbon community heating infrastructure). This is likely to be offered as a choice between implementing further measures on-site or paying into a local community fund.
In most situations, it is likely to be more cost effective to pay into a local community fund. For some projects it may be beneficial to incorporate on-site technologies — for example, a CHP plant that can export heat to the local community. Contributions to off-site wind turbines, for example, could be cheaper than the £3000 per tonne of CO2 maximum for allowable solutions, making it even more likely that developers would invest only the minimum necessary to achieve energy efficiency and carbon compliance.
Ultimately, decisions on achieving the different levels proposed in the zero-carbon consultation will be based on cost-effectiveness, which will require more work to cost energy-efficiency measures and low/zero-carbon technologies on projects to determine the most cost-effective routes to achieving the targets.
The Government is proposing to consult further later this year on aspects of the definition of non-domestic zero-carbon buildings that are not yet fixed.
David Cheshire is a regional director in AECOM’s sustainable-development group.