Regulating for lower carbon emissions
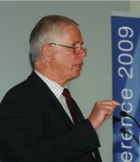
Not only do new Building Regulations due in 2010 require a further 25% reduction in design emissions of carbon dioxide, but they also plan procedures to ensure that the design intent is actually achieved, as Steve Irving explained to us.
Until 2006, designing buildings to comply with Part L of the Building Regulations merely required that the various elements met minimum standards. So the minimum U-value of walls, roofs, windows etc. were all specified. Designers could specify better than the minimum, but the task of the Building Control Officer was to ensure that compliance with minimum standards was met.
With concerns about reducing carbon emissions from buildings, leading lights in the industry, including Steve Irving, a director of Aecom (when it was Faber Maunsell), urged that designers and specifiers should seek to design buildings that were better than the minimum — but Part L of the Building Regulations did not require this.
The 2006 Building Regulations, however, saw a sea change in philosophy, with the projected energy consumption of buildings being reduced by about 25% over the same type of building designed according to the 2002 Building Regulations.
Engineers were given a certain amount of freedom to demonstrate their design skills by, for example, trading off fabric against windows, and heating-system efficiency against fabric heat loss. Constraints were imposed on design parameters — such as minimum U-values, minimum boiler efficiency and minimum efficiency for lamps etc. Building Control Officers were at least able to check compliance with such basic requirements, but would the building perform to its design?
Too often, the answer has been ‘no’, hence a fundamental change to the proposed Part L for the 2010 Building Regulations to address this problem. And this change is in addition to a further reduction in energy consumption of around 25% compared with the 2006 regulations.
‘As Steve Irving explains, ‘The forthcoming Part L aims to match the design performance with the as-built performance. There are various reasons why as-built performance does not come up to design performance, which the forthcoming Part L addresses.’
Steve Irving highlights three main elements in achieving compliance.
•Demonstrating that what is designed conforms to the standard in Part L.
•Demonstrating that what is specified is actually built.
•Demonstrating that what is built delivers the intended performance.
From his involvement in the preparation of the new Part L, Steve Irving can provide insights into how compliance is intended to work.
He explains, ‘The process begins when the plans are deposited with the Building Control Body, when the TER and BER should be specified.’ The TER is target emission rate for carbon-dioxide emissions as kg/m2/year and will be about 45% less than the same building designed to 2002 Building Regulations, depending on the type of building. BER is the intended building emission rate, which should be the same as the TER, or, preferably, lower.
‘At this stage, the BER should be accompanied by the specification on which the calculation is based. The compliance software will identify the most significant parameters that deliver the planned performance; this will help Building Control Bodies concentrate on these elements and check that they have been installed as per specification.’
When the building has been constructed comes the stage of confirming that what was specified has actually been built. Steve Irving says, ‘The person carrying out the work will be responsible for confirming that building constructed matches the specification. Likewise, if an accredited energy assessor carries out the TER/BER calculations, they must confirm the appropriateness of the data that is put into the SBEM or SAP program.’
Next comes the important stage of proving that the actual building delivers the intended performance. Steve Irving tells us that results from pressure testing have already led to significant improvements in the airtightness of dwellings, and the new Part L will require more dwellings in a development to be tested and that dwellings not tested should be assigned a leakage of 2 m3/h/m2 more than the average measured in the same type of dwelling (at 50 Pa).
In response to this higher assumed leakage, builders have two choices. They can do more pressure tests or accept the higher leakage and offset it with other energy-efficiency measures.
With the prominence placed by the forthcoming Building Regulations on intended performance, it is very appropriate that even more emphasis should be placed on commissioning. Steve Irving explains that when the plans are deposited, a commissioning plan should also be provided. He says, ‘Not only will the team that is responsible for design and construction have to consider commissioning as the design is developed, but the Building Control Body will be able to check that the commissioning plan is actually carried out.’
Not only do the new Building Regulations look to set in place procedures to ensure that buildings achieve their design performance, but they are also concerned that the building science on which designs are based reflect what happens in the real world.
Steve Irving explains that a major update to Part L for 2010 acknowledges that cavity party walls do not have zero heat loss if air can circulate in the cavity. He says, ‘Air movement in a cavity wall can cause the wall to have a U-value of 0.5 W/m2K, or even more, which is significantly higher than typical U-values for external walls of 0.25 to 0.30 W/m2K.’ Guidance on this problem includes edge sealing or full fill of the cavity.
While the 2006 Building Regulations gave more scope to engineers to give vent to their design skills, there were unintended consequences — notably completed buildings not achieving their design expectations. By requiring designers to say not just what their intentions are but also how they plan to deliver those intentions, will the 2010 Building Regulations help deliver buildings that use little more than half the energy of their 2002 counterparts?