Low-energy heating and cooling enters a new phase
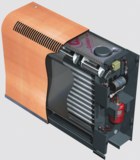
Storing heat when cooling is required and releasing that energy later when heating is required, and vice-versa, is an effective approach to reducing a building’s carbon emissions. Paul Aitchison explains how Monodraught has achieved just that.
Collaborating with the University of Nottingham, Ciba (BASF) Ltd, and the Carbon Trust, Monodraught has created a low-energy, intelligent passive-cooling and heat-recovery system for use in commercial, academic and healthcare environments.
Called Cool-phase, it provides powered fresh-air ventilation with the added capability of storing and discharging large amounts of latent thermal energy. The system uses a micro-encapsulated phase-change material (PCM) in the form of a slurry, which provides 4 kWh of thermal storage and supplies around 1 kW of cooling at any one time. All this is achieved using a fraction of the power required to run traditional air-conditioning (AC) systems, reducing carbon emissions and the detrimental effects usually associated with AC.
Phase-change materials absorb and give up large amounts of heat as they change between phases. These phase changes are typically solid to liquid and vice versa, but can also be solid to solid, solid to gas and liquid to gas.
Initially salt hydrates were used as the Cool-phase PCM, but we found that, owing to repeated cycles of phase, the material becomes ineffective after only two to three years. Ciba provided the solution, with a PCM that has a life span of about 10 years.
The material is supplied as a slurry, so the PCM can be stored more readily and used when required. In the Cool-phase application it consists of a wax held within a robust polymer shell. This has an extremely large storage capacity (a 1 cm-thick layer of PCM is equivalent to a 15 cm-thick layer of concrete).
The same technology can also be used to provide thermal mass in buildings. For example, by applying a layer of PCM to plasterboard, a metal-frame building can achieve the same thermal mass as a building constructed using traditional masonry techniques. This not only reduces construction time, but also reduces cost both during and after construction.
Cool-phase operates fully automatically, under three conditions: fresh air; cooling and heat recovery.
Under cooling conditions, the PCM is used to absorb heat from the air. In heat recovery mode it tempers incoming fresh air. Depending on operating conditions, the system will try to increase or decrease the temperature of the air using energy taken from the surrounding environment. However, an integrated CO2 sensor will override the control strategy and provide fresh air intake if levels exceed 1200 ppm.
In cooling mode, cold night time air is used to charge the PCM between 10 pm and 6 am. An increased flow rate from the fans draws cold air across the heat exchangers to cool the PCM, and this coolth is stored in an insulated tank.
During the daytime, the system draws fresh air into the space until the external temperature exceeds 23°C. An external damper is then closed and air is recirculated within the space. PCM is then pumped back through the system and air passing through the heat exchangers is cooled. Inversely, under heat recovery mode, the PCM is pumped through the system during the day, absorbing heat from the space, which is returned to the space the following day, tempering incoming fresh air.
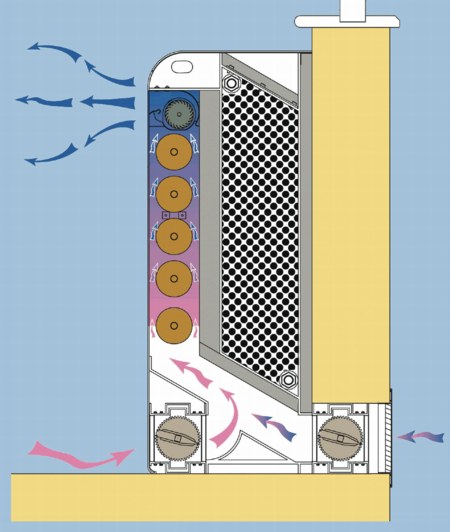
It is generally acknowledged that air-conditioning has detrimental effects on the environment, the major factor being the power consumption required to operate. AC typically requires kilowatts of power to run. Refrigerants used are extremely hazardous to the environment. Older types deplete the ozone layer and contribute to global warming. Even newer HFCs have over a thousand times the global warming potential of CO2.
The advantages of PCM for Cool-phase are its low power consumption (about 40 W), its recyclability (it is simply composted at the end of its life) and the obvious health benefits.
The Cool-phase system also provides fresh air and, with its inbuilt CO2 control, will maintain air quality at all times, providing low CO2 levels that are proven to increase concentration and well being.
The next stage is true zero-carbon cooling and heat recovery
Cool-phase was designed from the outset to run on DC power. Although only a small amount is required, that power is powered by mains electricity. Monodraught is therefore developing a solar-powered version, creating a true zero-carbon product for both commercial and domestic markets.
Paul Aitchison is product development manager for Cool-phase with Monodraught.