Why size matters for spiral ductwork
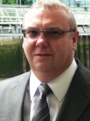
Philip Johnson of ADCAS* explains why the association is renewing its campaign to end non-standard sizing for circular ductwork — and the benefits for the entire industry.
Incorrect sizing of circular ductwork is costing the UK building-services industry millions of pounds every year — and that waste is simply not justified.
Standards — some new and some that date back as far as the 1960s — are being ignored by system designers in the search for...for. Well I am afraid that at that point I run out of ideas because, it is hard to work out just what they are looking for.
It cannot be good practice to insist on sizing that drives up the cost to the client, and surely it is the client’s interest that must be paramount for the consultant designer.
The simple fact is that there is no benefit in using non-standard sizes of circular ductwork. Designers, manufacturers and stockists of ductwork and components, contractors all lose.
Ironically the key advantage of circular ductwork rests on standardisation. The whole concept is to use this type of ducting for areas where standard sizes can be applied. Rectangular ductwork is custom made for areas where the standard approach is not possible.
Circular ducts — and all the ancillary components from volume control and fire dampers to VAV boxes and attenuators that go with them — are designed to be available on short delivery times, often ex-stock. Producing non-standard sizes takes up warehouse room that should be devoted to standard products. It adds unnecessary cost at every level up to and including transport to site. Non-standard items probably account for as much as 10% of the total stock value.
There is no excuse for this waste of effort, time and money. The standards that govern (or should govern) the proper selection of circular ductwork are plain enough. The primary standard is BS/EN 1506: 2007, and this standard is adopted for reference by HVCA DW144 — the ductwork industry specification that has been evolving since the 1960s.
Campaign
ADCAS — with support from a number of other leading industry bodies BSRIA, CIBSE, HVCA and HEVAC — launched a campaign to highlight the problems caused by non-standard sizing.
We have lobbied long and hard among consultants, contractors and our own members who manufacture and supply the ductwork. We have talked to the software houses that produce the system design software; as a result, some programs now incorporate simple alarms to flag up non-standard sizing to stop the problem before it starts.
We have made some real progress, as a recent survey reveals.
The old 600 mm-diameter ducts have virtually disappeared. Sales of 180 and 280 mm sizes have slumped by 50%, while demand for 224 mm circular ductwork has fallen by 27%.
But there is still no room for complacency. Demand for 224 mm ductwork was dropping, only for the trend to be reversed by an order for a single large project!
Now we have to redouble our efforts. It is time to return to the battle against waste and excess cost.
Domino effect
Perhaps I might quote an example from my own recent experience to highlight the ‘domino effect’ of difficulties that choosing a non-standard size can set in motion.
A huge amount of 280 mm-diameter ductwork and associated accessories was specified for the project. We asked for these items to be changed to standard sizes. This was refused because no-one would take responsibility for the change in design. The consultant had only prepared a design brief, and responsibility, therefore, passed on to the contractor. However, the contractor was not interested in changes, because the job had been priced with non-standard sizes and he saw no benefit for him in making alterations.
The result was a sharp increase in both cost and heartache. We had problems sourcing many of the accessories (dampers, supports, radius access doors etc.) and had to restock with a non-standard size ductwork that we had run down to emergency levels. Getting the product to site on time was a major problem, and this affected the overall programme.
All this hassle and waste could have been avoided if the design had called for standard ductwork sizes.
Cutting the number of standard duct sizes in line with BS/EN 1506:2007 also reduces the number of ancillary components — from volume control and fire dampers to VAV boxes and attenuators. Reducing the range of ductwork and components as required by the new standard makes it possible for manufacturers to offer a good selection of ‘standard’ products at competitive prices.
Latham
I am sure that you would never specify non-standard products. You know too well that Sir Michael Latham saw standardisation as an integral feature of a quality supply chain.
But if not you, perhaps it is one or more of your colleagues. And, as your eye runs round the office from desk to desk looking for a nervous glance, a guilty blush, a question naturally occurs. Why? Why do they do it if they do not gain any benefit? Well, sometimes old habits die hard, and some design software has not really kept pace with evolving standards.
ADCAS is determined to change all this; with your help we can.