10 rules for efficient boilers
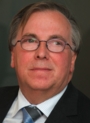
Neglecting boilers and controls can quickly lead to systems becoming inefficient and wasting energy. Tony Willis highlights 10 key considerations.
With increasing pressure to reduce energy costs and carbon emissions it is vital that existing boiler plant is fully optimised and maintained to deliver the maximum efficiencies. To that end it is useful to have a ‘check list’ of what to look out for.
Maintaining the BMS: Building-management systems or building and energy management systems (BMS/BEMS) are pivotal to maintaining the efficiency of a building and, like items of mechanical plant, they need to be regularly maintained. As building usage and occupation density change, so too do the control requirements for the heating system, and this needs to be reflected in the BMS configuration.
For example, the BMS PC terminal needs to be constantly reviewed and sensors require regular re-calibration, so you cannot always believe the information displayed. It is also worth remembering that a BMS manages the building’s requirements and typically doesn’t control individual boilers, so each boiler should be optimised separately to ensure maximum thermal efficiency.
Sequence the boilers: Most boilers deliver maximum thermal efficiency at 80% of their firing capacity, so it is important to ensure the minimum number of boilers is operating at any one time to satisfy variable system loads. Key areas to inspect include the motorised isolating valves (2-port valves) on each boiler to ensure they are working correctly and avoid unnecessary energy consumption due to boiler flow temperature dilution problems. The most efficient boiler is the one that is not firing!
Prevent dry cycling: Boiler dry cycling is an inherent problem found in all boilers of any size and age. Early attempts to overcome dry cycling either created a predetermined firing period (time delays) or lowered boiler set points based on return temperature. These measures affected room temperatures and comfort levels and potentially reduced the storage temperature of domestic hot water, increasing the risk of legionella. Both measures will also conflict with an existing BMS or weather-compensation controls.
In recent years technology has been developed to prevent dry cycling without reducing the boilers set points or room temperatures. This technology optimises the load of individual boilers using real-time analysis of the temperature profile of each boiler, rather than using predicted or historical firing patterns. Analysing real-time flow and return temperature profiles for each boiler differentiates between general heating demands and false demands created by standing losses that lead to dry cycling This technology also integrates seamlessly with existing controls such as BMS, weather compensation and boiler sequencing.
Regularly check boiler operating times: Check that time clocks are correctly set for required operating/occupancy times, with different settings for weekends and holidays, and are adjusted when the clocks move between GMT and BST. Building-optimisation/weather-compensation controls must also be correctly commissioned for required space temperatures, and occupancy times, and sensors should be regularly calibrated.
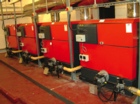
De-scale the boilers and clean the flues: Boilers with a build-up of scale or sludge waste energy through reduced heat-transfer efficiency, so it is important to check for correct chemical dosing and for leaks that may result in untreated water continuously refilling the system. This make-up water increases scaling and reduces the overall system temperature, thus wasting energy. Flues should also be cleaned regularly; dirty boiler flue-ways can reduce boiler efficiency by more than 10%.
Ensure your temperature set-points are correct: Boilers and controls should be set correctly for the required demand, particularly with high/low burners where reducing boiler set points can result in comfort issues. Hot-water storage temperatures need to be within legal requirements.
Check boilers are correctly designed for the application: Boiler plant should be correctly designed and commissioned for the application, with close attention paid to service reports and combustion efficiency — re-commissioning to adjust fuel/air ratio if necessary. The efficiency of replacement boiler plant may be affected by the existing distribution system, and re-commissioning should take account of this problem.
Understand the energy consumption: Main billing meters will not identify the energy consumption of individual items of plant, so sub-metering is required to properly understand energy consumption at this level and measure the benefits of energy-improvement initiatives. Any analysis of energy consumption needs to be degree-day-corrected and take account of other variables such as back-washing of swimming pools etc.Check for conflicts between heating and cooling: It is surprising how often poor control of space temperature results in a space being heated and cooled at the same time. HVAC systems should be integrated so they work in harmony and avoid these conflicts.
Assess occupants’ behaviour: Actions by a building’s occupants, such as changing room thermostats and opening windows, can have a serious impact on boiler/system efficiency. Or building managers may override the normal program for a special event such as a parents’ evening at a school and forget to re-set the controls afterwards. Regular evaluation of such behaviour will prevent these actions going unnoticed for extended periods.
Tony Willis is technical sales director with Sabien Technology.