Tackling the boiler plant
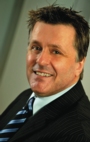
We will only get close to the UK’s target for carbon emissions reductions if we start to properly maintain and refurbish our existing building services, including boiler plant, argues Mark Northcott.
The Government is committed to reducing greenhouse-gas emissions by 34% by 2020 and a staggering 80% by 2050 (from base 1990 levels). While emerging renewable energy sources in new-build projects grab the headlines, the majority of savings will have to come from both a better approach to maintenance of existing building services and simple energy-efficiency improvements on refurbishment projects.
The coalition Government has pushed on with legislative drivers to bring about change in terms of the UK’s energy efficiency performance. Amendments to Part L (Conservation of fuel and power) of the Building Regulations came into force in England and Wales on 1 October 2010. They represent an average 25% improvement in efficiency over the 2006 regulations.
We have also seen the introduction of the CRC Energy Efficiency Scheme. The CRC EES is mandatory and aims to raise around £1 billion per year by 2014/15 by effectively taxing large energy users (over 6 GWh of electricity per annum) for the carbon-dioxide emissions that are attributable to energy consumption.
According to the Carbon Trust, about a third of the UK’s energy consumption is used for heating or producing hot water. A significant proportion is provided by commercial boiler plant, so it should be top of the list of any energy-reduction strategy. Typically, energy improvements of 10% or more can be made relatively easily through maintenance and low cost improvements to controls, insulation etc.
On older boilers, insulation may be in poor condition and can account for heat losses of as much as 10% of the energy input. Insulation should be replaced where it is insufficient or showing signs of degradation. Similarly, the insulation on the associated boiler pipework and valves should be replaced if necessary, which can result in additional savings of up to 10% of the boiler energy input.
On older and larger boilers, the flue can cause a flow of air through the boiler, even when it is not firing — cooling the boiler and losing heat to the atmosphere. A flue damper can be used to close off the flue when the boiler is not firing, preventing this energy loss.
Most heating systems use the same amount of energy for pumping, regardless of the load on the system, but they normally require maximum flow for only a limited time. Variable-speed pumps can be fitted which reduce the flow in the system to match demand. This can save 25 to 50% of the pumping energy consumption.
The most effective way to improve boiler performance is through controls. The minimum control strategy should encompass valved zone control, thermostats and timers. Further improvements can be achieved by the following methods.
• sequential control of boilers
• thermostatic radiator valves (TRVs)
• weather compensation
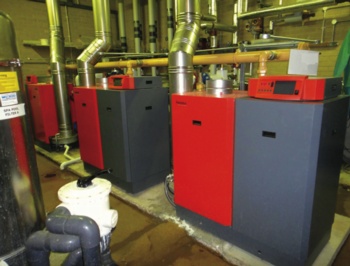
• optimised start/stop
• full zoned time control
• full building-management system
• decentralising the heating system to avoid long pipe runs
As an example, sequence control alone can achieve energy savings of 5 to 10% of the overall energy consumption of the boiler plant, as can optimised start/stop control.
Effective maintenance is essential in getting the best performance from your boilers. A full boiler service should be carried out each year, ideally before the start of the heating season. This service should include flue-gas analysis, controls calibration, burner cleaning and limescale treatment.
The fuel-to-air ratio is critical in ensuring efficient boiler operation. Analysis of the boiler’s flue gases for levels of carbon dioxide (CO2), oxygen (O2) and carbon monoxide (CO) will determine whether this ratio is correct and what adjustments need to be made.
If combustion conditions are not correct, particularly if too little air is used, unburnt fuel particles (soot) will build up on the fire side of the boiler’s heat exchanger. This soot creates an insulating layer, inhibiting heat transfer to the water. A 1 mm layer of soot will require a 10% increase in energy input to the boiler to meet the same heat demand.
In hard water areas, limescale can build up on the water side of the boiler’s heat exchanger. This also creates an insulating layer, inhibiting heat transfer to the water in the same way as the soot deposits above. A 1 mm layer of limescale will cause a 7% increase in energy input to the boiler to meet the same heat demand. The most effective method of limescale removal is through chemical treatment of the water. This should be done annually by a qualified technician to minimise limescale build-up and keep your boiler running at its most efficient.
Mark Northcott is commercial products director at Remeha.