The special needs of data centres
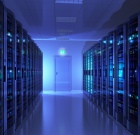
Data centres use lots of energy, including energy to cool the IT equipment. Not only must the building-services system be efficient but they also need to meet the special requirements of data centres, as Dominic Cutts of Armstrong Fluid Technology explains.
In critical cooling applications for data centres and other IT intensive spaces, HVAC system design has a fundamental impact on operational effectiveness and commercial success of the facility. Increasing use of advanced IT technologies, such as blade servers and virtualisation, is escalating the overall energy demand of data centres by 5 to 10% a year, and data centres are thought to be responsible for 3% of the electrical energy consumption of the UK.
![]() |
Fig. 1: Equipment that can automatically adjust to changes in demand throughout the day help to avoid using more energy than necessary. |
This high energy demand has led to the creation of an additional layer of energy-efficiency regulation and guidance for facilities of this type. The EU code of conduct on the energy efficiency of data centres, for example, aims to reduce the cost and carbon footprint of data centres, whilst also improving the robustness and security of IT systems. It covers two categories.
• IT processing capacity for the power consumed
• Building services load, including cooling systems etc.
In a separate initiative, The Green Grid Association, a non-profit, open-industry consortium of end users, policy makers, technology providers, facility architects, and utility companies has developed a metric measurement methodology. Using the PUE (Power Usage Effectiveness) metric, Green Grid has created a benchmark against which the environmental performance of every data centre can be measured. To explain how this works, a PUE of 1.5 means that for every unit of power used on core IT equipment, an additional 0.5 units is spent on the supporting infrastructure.
As the energy consumption of the IT equipment itself is difficult to reduce (as it is linked to the processing requirement) the drive to improve PUE (and thereby the ranking of the data centre in comparison to its competitors) has been focused on those aspects of efficiency which can be improved, namely the HVAC system providing cooling.
As much as 45% of the energy costs of a data centre can relate to the HVAC system.
Whilst both schemes are voluntary rather than mandatory, these benchmarking and accreditation initiatives are key to the ability of a data-centre to succeed in a highly competitive industry. For companies designing and installing the HVAC systems for customers of this type, the stakes are high. Performance of systems is continually monitored (with transparent reporting); upgrade cycles (and payback periods) are typically shorter than those of other buildings.
![]() |
Fig. 2: Modular systems such as this packaged pump set enable plant capacity to be increased rather than installing over-capacity. |
So when designing systems for data centres and other IT intensive environments, such as financial institutions, universities and laboratories, what priorities should you consider? In addition to the typical criteria of energy efficiency performance, and capital/lifecycle cost, it can also be useful to focus on the following.
• Demand-based control
• Scaleability
• Repeatability
• Integrity and reliability of the equipment
• Time to market
Demand-based control (as opposed to capacity-based control) is essential to optimise energy efficiency in these applications. Variable-speed components (Armstrong DE IVS pumps for example — Fig. 1) are essential to ensure that systems can automatically adjust to the differing demands for cooling throughout the day, in line with opportunities for natural cooling, and to cater for peaks in demand.
Scaleability. The business model on which data centres are established benefits significantly from the ability to scale up processing capacity incrementally as demand for the facility increases. This provides a more effective return on investment than designing in over-capacity at the outset.
The best HVAC solutions for data centres therefore feature modular design, enabling them to facilitate this incremental approach to the building’s cooling requirement. This avoids the significant energy wastage of over-sized plant, assisting the customer’s profitability. Armstrong iFMS modular packaged pump solutions (Fig. 2) meet this need, for example, as they are pre-designed, off-site manufactured pump packages that are fully-configurable to suit the application.
![]() |
Fig. 3: Off-site manufacture helps achieve system reliability and uptime. This is Armstrong’s self-contained IPP-CHW fully-integrated chilled-water plant package. |
Repeatability. The energy used by data centres energy is highly monitored and transparently reported. Best practice in system design will therefore offer predictability and repeatability of energy-efficiency performance to assist the customer’s considerable efforts to record and improve efficiency. Bespoke or ad hoc designs are of no advantage here. Proven, off-the-shelf solutions prove more effective.
Integrity and reliability of equipment. System reliability and uptime, referred to by the data centre industry as ‘The nines’, are key indicators of data-centre performance, and the building-services component is crucial in meeting these targets. Off-site manufacture has an important role to play here. Assembling and integrating a complete chilled-water plant room or pump package in the controlled environment of a factory provides the best possible guarantee of system integrity. Testing can also be carried out in the factory prior to delivery. The best solutions also incorporate fail-safe features. Armstrong’s self-contained IPP-CHW fully-integrated chilled-water plant package (Fig. 3) is a good example of this approach, combining the practical advantages of off-site manufacture, with outstanding energy efficiency via relational control.
Time to market. Responding effectively to commercial challenges and opportunities is key to the success of the data centre. As a result, approaches such as off-site manufacture, which can significantly reduce timescales by enabling assembly of systems to continue concurrently with other parts of the build, are already replacing traditional processes in this market. The Armstrong IPS (integrated pumping system), for example, (Fig. 4) has proved popular because it provides an off-site manufactured pre-packaged solution, with all the proven technology and repeatability of an ‘off the shelf’ system.
![]() |
Fig. 4: Offsite manufacture can reduce project timescales by allowing work to progress concurrently. This is an integrated pumping system. |
In conclusion, with energy requirements of data centres growing by 5 to 10% a year, HVAC system designers are at the sharp end, providing the means by which to manage the high sensible heat ratio, and to optimise performance of the IT equipment in order to reverse the growing energy demand. Within our industry, however, we already have the technology and expertise necessary to accomplish this task.
Dominic Cutts is director — system solutions with Armstrong Fluid Technology.