Commissioning radiator circuits in heat networks
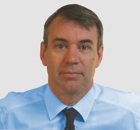
With many heat networks benefiting from low return temperatures, the control and commissioning of radiator circuits served by the network is crucial. Chris Parsloe of Parsloe Consulting examines the issues.
I was recently listening to a radio programme giving out plumbing advice. The caller described a problem of poor flow balancing in their radiator system. The expert adviser described a simple balancing process whereby the lockshield valve on the radiator that was slowest to warm up would stay full open whilst the second slowest would have its lockshield valve tweaked a quarter turn closed, the next slowest would be adjusted to two quarter turns closed, the next three quarter turns closed and so on, resulting in the previously most favoured radiator to be throttled the most.
Although undoubtedly effective on simple self-contained domestic radiator systems, this solution would not give satisfactory results on a radiator system fed from a heat network. For these systems, return temperature is critical to the efficient operation of the system.
Some low-carbon heat sources achieve peak efficiencies at low entering temperatures. Furthermore, the pumping and piping costs for the entire network can be dramatically reduced if a large ∆T is maintained. Therefore flow balancing for radiator systems fed from a heat network, whether they are fed directly or indirectly from the network, has to ensure that flows are set with sufficient accuracy to maintain the design temperature differential.
Using pre-settable valves can improve things and is a partial solution. If you know the pressure differential and flow rate for each piped radiator sub-branch, you can determine the setting on a pre-settable valve. But this assumes that a designer will calculate these values with sufficient accuracy to enable the pre-settings to achieve a balance. This requires some planning on behalf of the designer. In practice (and probably for this reason) this solution is unlikely to achieve sufficiently accurate flow balancing to achieve consistent return temperatures.
But accurate flow balancing will inevitably be problematic since individual radiator branches are not usually fitted with flow-measurement devices. Even if they were, the flows that would need to be measured are significantly less than the minimum flows that are measureable using conventional orifice type devices.
As an alternative to flow balancing, CIBSE Code W refers to ‘temperature balancing’ whereby the aim is to achieve return temperatures within ±3 K of each other. But this implies a great deal of trial and error since systems have to be heated up and allowed to stabilise for this to be measured and tested. Furthermore, it is very difficult to achieve if the design ∆T is large. Aiming to achieve a ±3 K range for radiators that each have a design ∆T of, say, 30 K would be, at the very least, extremely time consuming to achieve.
As is often the case, the objectives of CIBSE Code W can only be met if the design permits makes it possible.
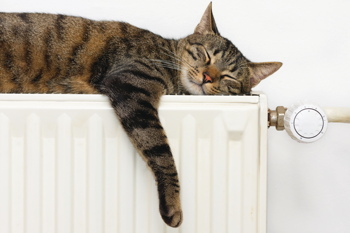
To stand a chance of achieving a balance, the branch serving the system needs to be pressure limited — i.e. fitted with a differential-pressure control valve (DPCV) that limits the differential pressure to a fixed value. Direct-fed heat-interface units are usually supplied with heating-circuit DPCVs for this purpose.
For small domestic heating systems, the pressure differential should ideally be set at around 10 kPa so that thermostatic radiator valves (TRVs) can be selected with sufficient authority to enable them to control effectively. (A TRV with a design pressure drop of 4 kPa should achieve good authority). This will also ensure that the design temperature differential achieved during balancing will be maintained during part load conditions as the TRV closes. Given the design flow rate and the maximum design pressure differential (i.e. 10 kPa) for each radiator branch, pre-settable radiator valves can then be used to achieve a reasonably accurate balance of flows.
Alternatively, for better accuracy, pressure-independent TRVs can be used (PITRVs). These can limit the pressure differentials across their own integral TRVs without the need for a separate DPCV. Individual flows can be set to their design values using the PICVs with reasonable accuracy. However, these valves are more expensive and, in direct-fed systems, additional DPCVs may still be required to limit the pressure across the PITRVs.
However, none of these solutions guarantee success. In cases where the maintenance of a large design ∆T is critical, the use of temperature-limiting valves in return pipes is the only solution. A temperature limiting valve installed in the return from each radiator will adjust its opening such that the return temperature is maintained at a constant value — typically 10 to 50°C. Although these valves add further cost to the system, they provide a significantly better guarantee of return temperature than balancing alone.
It can be seen that simple commissioning solutions that have served well in traditional systems will increasingly be found to be non-applicable when dealing with heat networks. There is certainly scope for more detailed commissioning guidance to deal with these applications.