Ecodesign – the heat is on
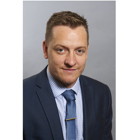
More stringent regulations for space heating are on their way as the next phase of Ecodesign requirements come into effect next year under the Energy-related Products Directive (ErP). Chris Meir considers the implications for boiler manufacturers and the building services industry as a whole.
Heating is a critical service in a building, but it’s also a large user of energy, accounting for around half its total energy use and associated emissions. Legislation like the European Union’s Energy-related Products Directive (ErP) aims to reduce energy consumption by establishing minimum performance standards for new heating equipment. Its goal is to phase out the installation of less efficient equipment across Europe, thereby reducing greenhouse gas emissions sufficiently to achieve its 2020 targets.
To recap, back in September 2015, tighter energy efficiency requirements were introduced under the Ecodesign regulations of ErP for new space heating equipment up to and including 400kW. These apply to both new build and replacement projects.
Next year further Ecodesign requirements will come into force. Firstly, from 1 January 2018, like-for-like replacement of non-condensing pressure jet boiler shells or burners under 400kW will no longer be possible. This was initially out of scope of the regulation to enable spares provision.
Then, from 26 September 2018, mandatory requirements for nitrogen oxide emissions will be come into effect. Maximum NOx emissions of 56mg/kWh will be enforced for gas and liquefied petroleum gas (LPG) boilers and 120mg/kWh for oil-fired boilers.
What implications has this had on boiler selection? ErP 2015 efficiency regulations have effectively made it mandatory to install condensing boilers on small to medium-size projects. The 2018 NOx requirements are likely to require a similar switch of technology and/or fuel supply to a more efficient or cleaner heating alternative.
In terms of both high efficiencies and low NOx criteria, condensing boilers are ahead of the game. The latest models are designed to achieve low NOx criteria at or below 40mg/kWh, making them future proof to ErP 2018. Some are also certified for operation on liquefied petroleum gas (LPG), providing a viable solution for off-grid organisations looking to switch to a more sustainable fuel source. As a result, the drive to condensing boiler technology looks set to continue.
So, what will this mean in practice? In new build projects, the emphasis will remain on specifying and installing high efficiency, low NOx, ErP-compliant heating equipment. The real challenge for consultants, specifiers and contractors could lie with refurbishment projects in dated buildings, where like-for-like boiler replacements may no longer be an option. Here a likely scenario is a switch to a condensing alternative operating on gas or LPG.
But, when switching to condensing boilers, additional design factors will need consideration. The flue or condensate arrangements, pipework modifications and/or change of fuel source, will all benefit from forward planning and collaboration with manufacturers to make the technology transition seamless.
Experienced manufacturers will be able to offer technical support and advice, identify challenges with the existing boiler plant, and recommend the most appropriate solutions. This includes engineering for maximum performance from the condensing boilers through intelligent design, good installation, and effective use of weather compensation and controls.
According to EU predictions, refurbishment projects can expect a welcome 20% reduction in energy costs when upgrading to ErP-compliant equipment. At the same time, ErP addresses the growing concerns over air quality by setting minimum performance standards for NOx emissions from heating. And the wide availability of ErP-compliant condensing boilers makes the requirements entirely achievable.
But while ErP may be the driver for improved boiler efficiency, the approach of the building services sector is key to maximising performance. Closer collaboration and knowledge exchange with heating manufacturers could help make the huge potential for energy savings and emissions reduction in the UK’s existing building stock into a reality.
Chris Meir is Sales Director at Remeha