Does the increased use of automatic balancing valves spell the end of the need for Commissioning Engineers?
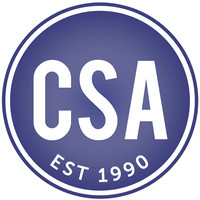
Surely, self-balancing valves and automatic balancing valves means there is no longer any need for a commissioning engineer? Wrong! Tony Anderson, Technical Manager at the Commissioning Specialists’ Association’s (CSA), explains why the commissioning engineer’s role is in fact more important than ever.
Commissioning a system that contains ‘automated valves’ should be quick and pain free for the commissioning engineer, according to most of the sales literature. However, as most commissioning engineers know this is rarely the case. Over the last 20 years ‘automated valves’ have become the front runners in the commissioning valve market. CFRs, DPCVs, PICVs and EPICV/EPIVs (see the explanation below) are just a few of the types available, each having their own sophisticated characteristics that can offer huge benefits in hydraulic applications.
When installed, using variable-flow pumps with a suitable system flow strategy, ‘automated valves’ can maximise flow efficiency, greatly reduce operational costs and offer enormous energy savings to end users compared with a traditional fixed-flow system. This translates into significant benefits over the operational life-span of the system.
From the off, it’s worth noting the terms ‘automated’ and ‘self-balancing’ as used in sales brochures largely refer to how the valves operate and control water flow after they have been set-up and commissioned.
Using caution
As a specialised component, one of the key challenges with automated valves is getting the system to a commissioned state that allows the valves to perform as per the design intent. Designers should use caution when assigning the pumping strategy around automated valves to ensure that the entire system is maintainable and lends itself to being flushed correctly. There are numerous examples where ‘temporary’ by-pass loops had to be installed retrospectively around the automated valve or component, as the energy-efficient design model did not allow for suitable flushing and back-flushing of all system components. This is a lengthy and costly addition to each project. It is no coincidence that, in nearly every example, the commissioning team was not appointed until the hydraulic installations were at an advanced installation level.
Specialist care is required when performing the pre-commissioning cleaning of systems that contain automated valves. It is possible that each automated valve has a specific flushing mode or dedicated flushing bypass installed; however, this is rarely found to be the case on-site. CFRs of the removable-cartridge type, for example, will have to have been bypassed or have their cartridges fully removed in order to achieve flushing velocities; the BSRIA standard flushing velocity or design +10% will not be achievable with the cartridge in place. Careful handling must be undertaken if removing and storing these cartridges to ensure these are not damaged and that they are correctly identified and re-installed in their original location and orientation. Most types of DPCVs must also be completely isolated during the initial flushing exercise. Alterations made to the system for flushing activities need to be recorded, and the system needs to be re-instated to ‘full flow’ condition before commissioning activities can commence. Proving the system has been reinstated and that control valves and flow cartridges are re-installed back to their original positions is a pivotal verification step on these types of systems.
The importance of pre-commissioning cleaning, again highlights the benefits of engaging a specialist commissioning engineer’s perspective at the design stage, as they can offer advice on the installation, chemical cleaning, commissioning and maintenance requirements of these valves and the system as a whole. Small changes, additions or alterations at design stage can make significant operational and maintenance savings in the long term.
What are the advantages
So what advantages do ‘automated valves’ offer to the commissioning of a system? A traditional proportional-balancing exercise on a fixed-flow system over a large circuit could mean revisiting and adjusting individual commissioning valves two or three times. The second and third times are the fine-tuning exercise, as excess flow from around the circuit can change the flow characteristics within a leg that has already been proportionally balanced. On an ‘automated circuit’ with automated valves on multiple branches, after a branch has been balanced there is no need for a second or third fine-tuning exercise. On a balanced branch with an automated valve set-up, the CFR, for example, would operate by limiting the maximum flow to this branch. Alternatively, a DPCV would counteract excessive pressure fluctuations by maintaining a constant pressure in the branch, regardless of what happens in the rest of the circuit.
The real benefit to the commissioning of a system with automated valves comes after this initial balance and set-up phase, as such valves can save a great deal of time by eliminating the need for fine tuning. Conversely, the commissioning engineer has to invest time in setting up the valve up in the first instance and then perform a varying-flow proving exercise. This involves the engineer being able to demonstrate that when different parts of the hydraulic circuit have been isolated, design flowrates in other parts of the circuit are maintained. This step proves that the variable-flow strategy works across the entire system.
Nowadays, buildings can contain numerous automated valves or combinations of different types of automated valves installed in various parts of the same system. The criticality for the commissioning engineer therefore shifts to understanding how the various valves are intended to interact and operate as a complete system, not simply how each valve operates individually. The clearest path to successfully commissioning and maintaining these systems is making sure the knowledge of how each hydraulic system is intended to be chemically cleaned, operated and maintained is shared between designer, installer, commissioning engineer and future maintenance teams.
With designers continually striving to produce the most energy-efficient solution to heating and cooling needs, the complexity of variable-flow models is forever increasing. As automated valves form an integral part of how each of these intricate design models operate, a specialist commissioning engineer should ‘automatically’ be selected at the earliest opportunity to help transform them into a fully functioning reality on-site.
Acronyms explained:
CFR: Constant flow regulator
DPCV: Differential pressure control valves
PICV: Pressure independent control valves
ePICV: Electrically operated pressure independent control valve
ePIV: Electrically operated pressure independent valve