Fan upgrades add control and energy savings
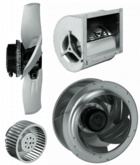
Lurking inside many pieces of equipment with fans in them are AC motors that can frequently be replaced with fans having electronically commutated motors to improve control and save energy — with attractive paybacks. Robert Harness takes up the story
EC fans are widely recognised as being the best thing in energy-efficient air movement technology, but what is an EC fan and what makes it so special? While most EC items are associated with the European Community, EC technology in relation to fans is not. In this case, EC stands for electronically commutated, which basically means it’s a fan with a brushless DC motor running directly from an AC supply.
Simple DC motors rely on carbon brushes and a commutation ring to switch the current direction and, therefore, the magnetic-field polarity, in a rotating armature. The interaction between this internal rotor and fixed permanent magnets induces its rotation.
In an EC motor, the mechanical commutation has been replaced by electronic circuitry which supplies the right amount of armature current in the right direction at precisely the right time for accurate motor control. Matters are further simplified by using a compact external-rotor design with stationary windings. The permanent magnets are mounted inside the rotor with the fan impeller attached.
Brushless DC motors have been around for many years but there has always been the need for a separate DC power supply. In applications using only an AC supply this requirement introduced added cost and complexity. Then, in 2003, ebm-papst brought out an EC fan with integrated electronics which could be connected directly to an AC mains supply. In addition to performing the commutation, the electronics converts AC to DC and controls the fan speed by regulating the power to the motor.
Put simply, DC motors are around 30% more efficient than AC motors because the secondary magnetic field comes from permanent magnets rather than copper windings. An AC motor consumes additional energy solely to create a magnetic field by inducing a current in the rotor. But this is only half the story. The use of modern electronics in controlling the motor has opened up many other possibilities which contribute to using less power.
To control the motor accurately and efficiently the integrated electronics have to continuously monitor the motor speed and adjust the control input. By making this circuitry available to external sources it’s possible to provide simple speed-control options. Dependent on the motor type, any sensor which can provide a 0 to 10 V/PWM or 4 to 20 mA input can be directly connected to provide closed-loop control for temperature, pressure or whatever parameter you choose to measure. No need to worry about DC supplies for the sensors either, because it is provided by another connection on the motor. In fact, simply connect a potentiometer and you have infinitely variable speed control — no triacs, no frequency inverters and no whining noises. An EC motor under speed control is virtually silent.
So how does this affect energy efficiency? Well, doubling the speed of a motor increases its power input by a factor of eight, so it is very wasteful to run a fan faster than is required. If you can tailor the fan speed to match the demand, the potential for energy saving is huge. Even when compared to on/off operation, EC speed modulation is much more efficient. (see diagram) Fitting variable-speed drives (VSDs) is one answer, but these actually reduce the efficiency of an already less-efficient AC motor. With EC fans, the VSD functionality is included in a much more efficient package.

The superior controllability of EC fans can also contribute to increasing the overall efficiency of an application. In a chiller, for example, keeping the compressor head pressure constant rather than having it rise and fall as fans switch on and off has been found to significantly reduce the load on the compressor, resulting in even greater energy savings.
Consider this as well. If two motors are producing the same amount of work but one has a greater power input then you can be sure that the surplus energy is being dissipated as heat.
A piece of equipment designed to remove heat will have to do extra work just to remove the heat produced by the fan motor itself. This is why, in cooling applications such as data centres, replacing AC fans with EC fans produces energy savings of over 40% — with paybacks of two years or less.
Fans are the hidden energy consumers in commercial buildings but upgrading them can produce some very visible savings. EC fans can be retrofitted on a like-for-like basis into most applications with no change to the fabric of the building, little or no disruption to the occupants and easily measurable results. When searching for your next phase of carbon-reduction measures it may be worth taking a good look at the fans in your HVAC systems.
Robert Harness is business development manager for ebm-papst UK Ltd.