Thinking beyond the groove
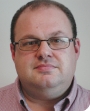
The benefits of grooved-end mechanical piping systems extend beyond quick, heat-free joints to reducing the need for flexible couplings and straight runs of pipe to and from pumps. Andy Carter of Victaulic shares his ideas on the effect on plantroom space requirements.
High performance and low maintenance are key criteria for plantroom installations. Whilst owners demand on-time, on-budget delivery of high-quality systems that work well and are easy to maintain, space is becoming a critical factor too. Ever tighter architectural designs are putting pressure on consulting engineers and contractors to deliver reliable, cost-effective HVAC solutions that minimise the mechanical room footprint.
Grooved-end mechanical piping systems address all these issues. The smaller size yet higher integral strength of grooved components compared with welded or flanged systems make them ideal for projects that are tight on space. Their ease and speed of installation offer savings on total installed costs and they also deliver improved performance and reliability.
![]() |
The lighter weight and smaller size of grooved components, combined with higher integral strength, make then ideal for projects where space is constrained. |
Eliminating flexible connectors
Grooved couplings are designed with an elastomeric gasket contained inside the internal cavity of a ductile iron or stainless steel housing and secured by two nuts and bolts to create a leak-tight joint. This design gives the couplings noise and vibration reducing properties superior to those of traditional devices.
In traditional installations flexible connectors — or rubber bellows — are placed in the piping system at either side of the pump to reduce noise and vibration. Not only do they take up valuable plantroom space, but rubber connectors are considered the weakest point of an installation and the first component that is likely to fail, as general wear and tear and exposure to UV light in the mechanical room cause the rubber to erode.
They also require ongoing maintenance; as bolts gradually slacken and the system starts to weep, the bolts need to be tightened regularly. With a best life expectancy of 10 years, rubber bellows may need to be replaced several times within the life of the system — which involves system downtime plus the cost of a new unit. Failure of rubber bellows can be sudden and unpredictable, causing serious health-and-safety risks if, for example, the rubber splits and water escapes.
Installing three grooved flexible couplings either side of a pump solves these problems. It eliminates the need for costly, bulky flanged units and avoids the use of rubber bellows. The coupling construction enables the gasket to seal against the pipe, while the metal housing provides both space for the resilient elastomeric material to flex and containment to prevent overstretching. This creates a discontinuity similar to that of a rubber compensator. Additionally, ductile iron and stainless steel both have their own vibration-dampening qualities, so the external housing also serves to absorb sound, thereby protecting equipment and enhancing the life time of the system.
![]() |
Three flexible couplings place close to a pump or chiller reduce noise and vibration significantly and eliminate rubber bellows. |
Three flexible couplings can be used not only with pumps but also with chiller units, cooling towers and any equipment with an engine that causes vibration. The use of additional grooved couplings, whether flexible or rigid, in the distribution lines will further reduce the transmission of vibration. This method provides a low-maintenance solution that saves space and delivers both practical and commercial benefits throughout the life of the system.
Improving pump efficiency
Cavitation is a problem frequently experienced, especially where space is limited.
When turbulent water enters a pump chamber and the suction eye of a pump impeller, the degree of turbulence has a direct correlation with lower pump efficiency and greater hydraulic noise within the pump casing. To reduce the effects of turbulence before the water enters the centrifugal action of the pump impeller, suction pipes are typically kept as long and straight as possible before the connection onto the pump flange. However, creating long lengths of pipe does not sit well with modern design trends which aim to keep plantrooms compact.
Where a bend is connected directly onto the pump suction, the water flow may spin in opposite directions within the eye of the impeller. Pump energy then has to be spent correcting this action before producing the expected performance. Inevitably, both flow and pressure measurements will be less than those expected at the design stage.
![]() |
A suction diffuser enables pipework to be connected closer to the pump, permitting a smaller mechanical room footprint.
|
A simple alternative is to fit a type of strainer called a suction diffuser to straighten the spinning fluid created by the change in direction (bend), enabling pipework to be connected closer to the pump at a 90° degree angle. Eliminating long pipe runs, elbows and reducers makes for a smaller mechanical room footprint and optimum pump performance. There are cost savings, too, with installation being completed more quickly, so labour costs are reduced.
Winning formula
Switching from welded and flanged specifications to the grooved method for plantroom installations can make a big difference to the success of a project.
Engineers, contractors and owners all stand to gain from grooved systems. Design engineers can realise space savings, contractors can make time and cost savings, and owners get an efficient, reliable system which is easy to maintain.
Andy Carter is product engineer at Victaulic with 23 years' experience of providing technical support for a range of products.