The perils of neglecting maintenance
HVAC plays a critical role in many buildings — John Wright of Eaton-Williams Service
Preventive maintenance prolongs plant life, increase energy savings and saves money, so why do too few companies realise the benefits asksJOHN WRIGHT?Neglecting a building’s facilities, especially HVAC plant, leads to deterioration in equipment and environmental conditions that can prove costly in the long term and have far-reaching implications. Yet there are still companies out there cutting corners in a bid to reduce overheads, without realising the potential problems they are storing up.
Major obstacle Identifying costs and savings is clearly a major obstacle. It is very easy to look at a balance sheet and assess the cost of maintenance and how much can be ‘saved’ by reducing maintenance programmes from four visits to just once a year. But it is far more difficult to assess actual benefits. Experienced engineers always aim to ensure that a customers’ plant runs as efficiently as possible and performance is maximised, but it is an uphill struggle trying to convince them of the appropriate level of maintenance to maximise the efficiency and extend the life of their plant and not eat into their long term budget. Although modern facilities management is not just confined to the upkeep of the air-conditioning system and embraces a whole raft of services, HVAC plays a critical role in many buildings — ranging from providing a comfortable working environment for employees to maintaining conditioned environments for business-critical functions such as computing and telecommunications, clinical, pharmaceutical or industrial environments. Applications are diverse, but neglecting the service and maintenance of HVAC kit can have far-reaching effects in any one of them, including the following. • Health of the building’s occupants (sick building syndrome). • Safety. • Productivity. • Energy efficiency. • Increased life costs. • Litigation. • Loss of business.
Regulations The 1992 workplace regulations require every employer and building owner to ensure that air introduced should as far as possible be free of impurities that are likely to be offensive or cause ill-health. This means that mechanical ventilation systems should have effective filtration and be regularly and effectively cleaned. Equipment inevitably becomes less energy efficient as it ages, but with regular maintenance, performance levels can be maximised and durability may even be extended. It is only when repair bills start to appear more frequently that companies appreciate that dispensing with a maintenance contract is a false economy. If a car is not regularly serviced, it will eventually let you down. Similarly air-conditioning systems will not operate at peak performance and do the same. This results in low comfort levels for a building’s occupants and compromises a company’s commitment to energy efficiency, increases exposure to fire risks, increases costs, affects morale, health, safety and productivity. Litigation as highlighted by the recent Barrow-in-Furness case could become an issue. It is surprising that sometimes the person in charge of the building may not always be aware of their legal responsibilities and may flout the law without being aware that they have done so. All companies are legally obliged to exercise a duty of care, and ignorance of the law is not an excuse.
First sign As a rule when maintenance is no longer a priority there will be no immediate impact, but over time faults will develop. The first signs of reduced maintenance can be feelings of discomfort, either too warm and sticky or too cold. Over time these symptoms may increase until the building’s occupants are very uncomfortable and flag up problems with their environment. A dirty coil is but one example where reduced maintenance can seriously compromise the effectiveness and the service life of an air-conditioning system. Detritus accumulating on a coil acts an as insulator and hampers its ability to function. The effect is initially slow, but debris building up on the coil surface acts as a filter, catching more debris and becoming more efficient at catching smaller and smaller airborne particles. This will cause the system to work harder to achieve the same cooling effect — using more energy and increasing stress on other components, particularly the compressor by running it more frequently. The greatest strain on any component or system with moving parts is generally when it starts up. If compressors or fan motors are constantly stopping and starting needlessly and the problem is lack of proper maintenance the life span of the component is reduced. Premature failure can result in damage to other internal components such as a blade or bearing failure or create refrigerant gas leaks or fractured pipes due to excessive vibration.
Air quality Hygiene is a major consideration, and air quality-measurements are becoming commonplace. Air needs to be clean and filtered correctly. Filters need to be routinely cleaned or replaced. Clogged filters block the normal airflow and reduce a system’s efficiency significantly. With the normal airflow obstructed, any air that bypasses the filter may carry dirt directly into the evaporator coils and impair their heat-absorbing capacity. If left unattended, filters end up being coated in a concentration of local airborne contaminants which may eventually leak into the ductwork and the conditioned space to cause a potential health hazard. Rooftop fresh-air intake systems are often exposed to many unsavoury conditions. Vermin, wasps and flies may find their way onto the filter media if appropriate precautions are not taken
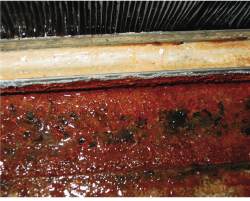
Blocked air filters can become a source of local airborne contaminants leaking into ductwork and the conditioned space to cause a potential health hazard.
Pigeons are notorious environmental vandals and can cause considerable damage. Rooftops and plant compounds are favourite haunts. Once pigeon excrement dries, it decays and breaks down and can find its way onto the filter media. This can then eventually be transported through ductwork and possibly inhaled by a building’s occupants if suitable filtration and adequate maintenance regimes are not in place.
Bare minimum Typically maintenance problems arise in peak periods and can be exacerbated by the lack of available service engineers who are already locked into other contractual obligations. All too frequently, maintenance programmes are reduced to the bare minimum, driven by an aggressive market and competitive pricing. Yet, when problems arise customers expect an immediate service, which may prove difficult because resources of most service companies match the maintenance contract value. Others simply operate by relying on breakdown repairs as and when needed. Some companies do not undertake any maintenance at all and only have sight of an engineer when a problem occurs. Reactive maintenance offers a short-term fix and one-off cost but it does not prevent further breakdowns and engineer call outs. All too quickly, the cost of any repairs and downtime can become a sizable overhead in itself.
Major issue Price is a major issue. In an already volatile market, customers clearly look for the best deal at the best price — even if that means compromising on how frequently a boiler is inspected or cutting back on the cleaning of filters, condensers or heat exchangers. Contracts should not be awarded solely on price. A well defined maintenance programme carried out by qualified and competent engineers will not only ensure reliability and optimum performance but will also encompass health and safety issues, energy efficiency and reduce whole-life costs.
John Wright is general manager of Eaton-Williams Service, Station Road, Edenbridge, Kent TN8 6EG.
Related links: