Innovation in maintenance
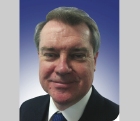
In the face of conflicting pressures of maintenance expectations and budgets, Tony Byrne of Interserve discusses the latest trends in building maintenance and highlights some of the current models and innovative techniques being developed to help organisations realise both cost-savings and efficiency gains.
Recent research carried out in 2012 by Interserve identified that 60% of organisations outsource more than half of their facilities services, with cost savings remaining the key driver. Of the 16 objectives identified for outsourcing, every one except innovation is being met in 70% of cases. Against this backdrop of improved service delivery, reduced costs and increased competition, it is surprising that innovation is falling short.
Over the past 30 years, maintenance of the built estate has changed — perhaps more so than any other management discipline. These changes are due to a huge increase in the number and variety of assets (including plant, equipment or the building fabric itself) which must all be maintained — coupled with more complex designs and changing views on maintenance techniques.
At the same time, our expectations of maintenance have evolved. They are no longer confined to ensuring that the physical assets in a building are in good repair. Instead, there is a growing awareness of the extent to which a building’s infra-structure is vital in enabling employees to perform their jobs effectively.
As our dependence on physical assets grows, so too has the cost to operate and own them. In some sectors, maintenance is the highest proportion of operating costs, far exceeding the initial capital investment. In this context, delivering innovation has a dual role to play, enabling improvements in asset performance and, at the same time, reducing the overall cost of maintenance.
This has led to an explosive growth in new maintenance techniques over the years, with many businesses left challenged to understand what these techniques are and then decide which are worthwhile.
Our response is a strategy based around a business-focused maintenance framework that enables stakeholders to respond directly to these challenges. The process begins with a comprehensive review of the maintenance requirements of each asset in its operating context.
Previous maintenance regimes have not always followed this principle, resulting in the implementation of systems based on incomplete or incorrect assumptions about assets. However, if these requirements are defined correctly at the start of the process, it is possible to achieve a significant step change in maintenance efficiency and effectiveness.
To demonstrate, we use a workforce management solution for a number of clients, which enables real-time management of planned and reactive work across any geographical area. Based on a set of parameters that are in line with the requirements of the contract, this solution has increased first-time fix rates to 63% and reduced call response times from three minutes to 15 seconds.
Importantly, it also saved the client £1 million and introduced a system that manages and monitors the whole estate in real time from anywhere in the country.
With the constant drive for cost reductions hitting many companies hard, there are difficult decisions to make on where cutbacks can and should be made.
Cutting out maintenance regimes altogether is clearly not a viable solution and will only serve to increase costs later on as the likelihood of equipment failure increases. Equally, there will not be an unlimited capital expenditure budget for new plant and equipment.
As a result, service providers are working with their clients to see how the performance of existing assets can be optimised. One route may be for companies to simply categorise their buildings and equipment from critical to non-critical, with the latter receiving statutory compliance and reactive maintenance and the more critical receiving a detailed planned-maintenance programme.
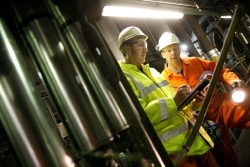
While this approach may release some cost from the overall maintenance budget, it will have minimal effect on improving asset performance and protecting a business’s equipment investment for the long term.
It is at this stage, that investigation into some of the latest trends in maintenance can pay real dividends.
One example is the use of mobile technology and web-based systems, which can provide real-time reporting on the status of equipment. Portable devices are now becoming more commonplace for undertaking routine operations such as daily plant room checks or quality inspections. This allows asset data to be captured and monitored straightaway, instead of there being a delay that could impact on productivity.
There are an increasing number of energy-efficiency products and technology innovations being delivered due to the need to reduce energy costs and carbon emissions. Examples of this include voltage-reduction schemes, using both passive and active reduction technology, the use of high-performance light fittings with on/off and sensor technology to minimise waste, and the investigation of district-heating schemes with the installation of higher-efficiency plant and heat exchangers to capture otherwise wasted energy.
Another trend in the drive for service innovation is to take a more intelligent approach to routine equipment maintenance. Rather than implementing a standard reactive or planned method, there is a move towards the use of predictive techniques.
Predictive, or condition-based, maintenance is based on using real-time data to prioritise and optimise maintenance resources.
The main value of this approach is to allow convenient scheduling of any necessary repairs or service requirements and to prevent unexpected equipment failures. By continually monitoring performance, the service team can factor in maintenance, resource and spare parts availability. What may have resulted in unplanned equipment failure is transformed to planned downtime, thereby enabling greater productivity to be achieved.
Another option includes exploring less intrusive maintenance techniques. It is quite common for inspections of boilers and electrical equipment to rely on infra-red imaging and X-ray techniques to determine any existing or potential defects, helping to reduce the time and cost associated with more traditional equipment-inspection routines.
The right maintenance contract requires a balanced approach. There is never a one-size-fits-all approach for each business, and every single maintenance programme needs to be tailored for each client.
It is by working strategically with the maintenance services provider that customers can optimise asset performance. By thinking smarter about the way the maintenance programme is built and delivered and by introducing innovation in small ways, businesses can begin to achieve the cost and efficiency savings required.
Tony Byrne is managing director for integrated facilities management at Interserve.
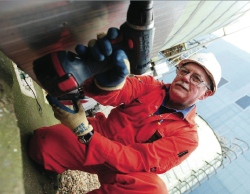