A system approach to boiler costs

The focus of legislation is increasingly on the whole-life costs of boiler plant, which has major implications on how boiler plant will be specified, says Gavin Watson of Elco UK.
Since 2007, the heating industry has become accustomed to new legislation, from the inception of the 20-20-20 targets, through to the Carbon Reduction Commitment, updated Building Regulations and Energy Act 2013. The result has been wholesale changes in the approach taken to the specification of heating and hot-water equipment.
To maintain the conveyor belt of product development and quest for zero carbon, this year will usher in the Energy Related Products Directive (ErP), which is the latest European-led round of changes to affect the industry. The directive consists of two areas, but the most significant is the Ecodesign (2009/125/CE). This sets minimum energy performance and environmental criteria for energy-related products sold in the domestic, commercial and industrial sectors in the European Economic Area.
As far as the commercial sector is concerned, the main impact will be on fossil fuel (gas and oil) boilers and water heaters with outputs up to 400 kW. In addition, water heaters and hot water storage tanks with capacities less than 2000 l will also fall under these new requirements. As a whole, this legislation will help the UK continue to achieve its carbon-reduction targets, by effectively eliminating all inefficient products from the market falling under this category.
Atmospheric boilers are certain to be the most affected by these changes and are sure to be removed from the market by the end of this year. In the new-build market, condensing boilers have been the unit of choice for almost a decade. However, in retrofit applications, atmospheric units have often been specified based on reduced capital and installation costs. But the focus is changing; it now needs to be on the lifetime costs — and these need careful consideration during the specification process.
The economics of an installation now need to be reviewed from the outset. However, this approach is nothing new; for example, Elco has been developing products that are designed to reduce costs over the product lifecycle for many years.
So, what do consultants need to look out for when specifying the latest condensing boiler plant?
Selecting appliances with excellent efficiencies might sound like the obvious answer but, realistically, the days of boiler manufacturers gaining an advantage with a percentage here or there is a thing of the past. Instead, one factor to consider in the lifecycle costs of a unit is the design and manufacture of the heat exchanger.
Over a lifetime, a heat exchanger will have to tolerate thermal and mechanical stresses, the vagaries of system water quality plus dissolved oxygen — not to mention the effects of corrosive condensate.
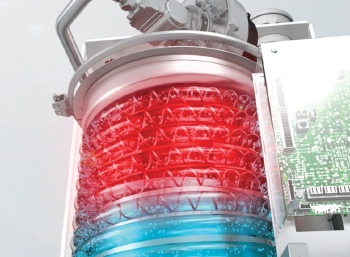
For exactly these reasons, all our gas-fired condensing boilers use stainless-steel water tube type heat exchangers. These heat exchangers are designed to promote turbulent flow within the waterways, which helps to eliminate a static boundary layer and, in turn, reduce the tendency for micro-boiling. This ensures quieter running, a reduced risk of internal fouling and, more importantly, promotes good and efficient heat exchange for better efficiencies. These factors can have a huge impact on the overall running costs of a system.
The Government is certainly behind this principle of lowering lifetime costs with the Soft Landings Framework and PAS 1192-3 — a BIM specification for the information management requirements during the operational phases of assets. Effectively, these principles recognise that better awareness of the operational and maintenance needs of assets can help optimise their whole-life costs.
This method will become even more important in 2016, when the UK introduces a new EU Directive on public procurement. So, rather than awarding a contract on the basis of lowest price, it will have to be justified as the ‘most economically advantageous’ tender. This will include life-cycle costing and environmental aspects.
To help the UK continue meeting the strict targets, it is important for manufacturers to be on hand to advise on the best options. This can often mean looking beyond the individual components to the entire heating and hot-water system, as well as ongoing servicing requirements. This approach can often bolster the argument for using a sole manufacturer for an entire system as, not only can it ensure all components work together effectively, but also allow the entire lifecycle running costs to be calculated accurately from the outset. There are also some other practical elements to using equipment from the same manufacturer, including shared maintenance schedules and first line spares, which can, again, help plan costs effectively over the lifecycle of the equipment.
Employing a more joined up approach to the specification of heating and hot-water equipment is sure to help reduce long-term running costs and overall expenditure. Promoting this message to the whole industry will be a challenge, but it will ultimately help drive the UK industry forward in its carbon reduction ambitions.
Gavin Watson is sales director for Elco UK.