Race tuning your air conditioning system
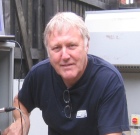
The loss of performance of an air-conditioning system can pass un-noticed, and the causes can be difficult to identify. Mike Creamer of Business Edge shares his enthusiasm for an approach to both problems.
Most people have no idea how much energy their air-conditioning systems consume. It can be over 50% of a building’s running cost! Moreover, most people responsible for the running costs of buildings are also completely unaware of the variation in the power input and cooling capacity of their air-conditioning system, both of which can change dramatically according to outdoor temperature and building load.
Worse still, cooling capacity and power input are very badly affected by only the smallest adverse condition such as partially blocked outdoor condenser coil, a broken blade on a condenser fan, too much or too little refrigerant in the system, an incorrectly adjusted expansion valve or a compressor that is progressively wearing out.
To make matters worse, temperature, pressure, power input and many other parameters are constantly changing — making it virtually impossible for even the best refrigeration engineers to record and analyse exactly how a system is behaving. Indeed there is no technology to enable the refrigeration engineer to accurately determine the cooling capacity, compressor efficiency, system efficiency etc.
However, there is a technology that enables all this information to be monitored quickly and readily in the field. It is the portable ClimaCheck Performance analyser, which can be connected in about 20 minutes to any type of air-conditioning system, of any configuration and running off any refrigerant fluid. This technology then enables the engineer to see every operating parameter and record them for service reports. Most importantly, the refrigeration engineer can immediately see what areas of the system require attention, adjustment or remedial action. Indeed, the technology also allows the refrigeration engineer to see running costs and CO2 emissions.
Armed with this technology, the engineer can show the client the poor performance before adjustments and repairs and the resulting improvements — often reducing energy costs by 10 to 40%.
As an example, a well-known bank in London has four water chillers, each of 750 kW cooling capacity. Power input should be about a third of the cooling capacity, i.e. 250 kW per machine (1000 kW). The water chillers serve the building’s comfort air conditioning and data centre requirements with a running cost of about £450 000 per annum. However, adverse conditions led to two machines consuming almost 350 kW. Simple adjustments led to just under 40% energy saving. The associated impact on running cost was very dramatic indeed.
ClimaCheck is also available as a permanently installed add-on. It streams recorded data every minute to the ClimaCheck web server, which records a 2-year rolling window of performance. Instantaneous or historical performance is available by smart phone, table or PC. ClimaCheck technology will also perform direct and indirect refrigerant-leak detection, providing advance warning of imminent plant failure and/or excess energy consumption to eight recipients in text or email format.
The portable ClimaCheck can normally be connected within 20 minutes, or you can fit permanent ClimaCheck to your water chiller or direct-expansion system. You can then view all of the following parameters from a smartphone, tablet or PC.
• Cooling capacity (kW).
• Power input (kW).
• Power factor.
• Heat of rejection (kW).
• Sub-cooling/superheat values (K).
• Compressor isentropic efficiency.
• Water in/out or air on/off temperatures (°C) at the evaporator.
• Water in/out or air on/off temperatures (°C) at the condenser.
• Water or air flow rate (kg/s and m3/s) at the evaporator and the condenser.
System abnormalities can be easily identified and rectified as you watch the live effects of adjustments.
• Cyclic operation.
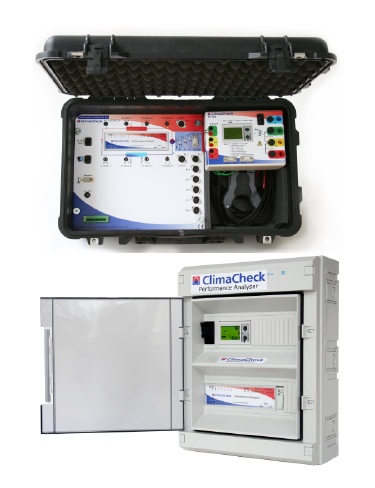
• Inadequate or excess refrigerant charge.
• Undersized or blocked condensers.
• Fouled evaporators.
• Defective or maladjusted thermostatic expansion valves.
• Inadequate water-flow/air-flow rates.
• Incorrect low ambient – head pressure control settings.
• Poor compressor isentropic efficiency.
• Unstable operation and imminent failure.
• Compressor motor overheating.
Another very useful capability of ClimaCheck is SEI (system efficiency index). SEI determines your plant efficiency and even which component is responsible for defective operation — which is far better than COP. ClimaCheck can also identify which of your systems require the most urgent and immediate attention.
Finally, a summary of ClimaCheck’s capabilities.
• Calculate and display of cooling capacity, heat of rejection, SEI, compressor efficiency and water/air-flow rates.
• Identify massive energy-saving opportunities by maximising the efficiency of critical cooling systems.
• Reduce the incidence of plant failure by providing early warning of unstable operation and progressive deterioration.
• Minimise downtime through AC&R plant failure, thus increasing reliability.
• Enable technical staff and external service contractors to view the system performance and status locally and remotely.
• Provide advance warning of refrigerant leakage/loss via email and text alerts.