Exerting control over energy efficiency
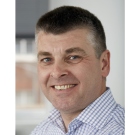
Karl Walker of Beckhoff explains how a British Standard points the way towards using controls to improve the energy efficiency of buildings at a time when building owners are under increasing pressure to improve their energy ratings.
From April 2018, owners of properties rated at EPC levels F or G will be unable to let them until remedial work has been carried out to address their energy efficiency, as defined by the ‘Energy Performance of Buildings Directive’ (EPBD 2002/91/EC). The methods for expressing energy performance and for energy certification of buildings are governed by BS EN15217:2007 and are often referred to as the ‘minimum energy performance standard’ (MEPS).
With around 19% of all EPC-certified commercial buildings having an F or G rating, and a further 16 to 17% on the cusp with an E rating, this policy has serious implications for landlords and occupiers regarding the required investment to improve the energy efficiency of existing commercial property stock.
Of course, improvements to the building’s fabric, such as insulation and glazing can realise the biggest returns, but they are high-cost and also not always possible on existing buildings. However, substantial improvements in the energy efficiency of many existing buildings can be made through intelligent and holistic building automation.
Amongst other things, BS EN15217 specifies ‘overall indicators to express the energy performance of whole buildings, including heating, ventilation, air conditioning, domestic hot water and lighting systems’. What it doesn’t do, however, is specify how the interaction between the control of these functions can seriously help to mitigate energy wastage and realise greater levels of occupier comfort. This is where BS EN15232 comes into play.
BS EN15232 defines the minimum levels of building controls required to achieve different levels of energy efficiency in commercial and domestic buildings. The standard was developed to support the European Energy Performance of Buildings Directive (EPBD), which sets the targets used in Part L of the Building Regulations.
BS EN15232 offers clearly defined methods for clients to decide what they want the building automation control system (BACS) to achieve, and to ensure that contractors understand and deliver these requirements.
The standard outlines four performance classes, from A to D.
It would seem obvious that everyone would want to achieve class A and, in a new build, there is absolutely no reason why this wouldn’t be possible. The caveat though, as highlighted above, is that the contractors have a full understanding of the client’s requirements and don’t try to cut corners through ‘value engineering’. It is also important that there is an implicit understanding of how the different building-services disciplines — heating, cooling, shading, ventilation, lighting —interact with one another to work as an holistic end solution.
It would go without saying that a modern lighting system would have PIR presence/absence detection for control of the luminaires. So, why should these same PIRs not also be used as part of the control for, say, the heating or cooling circuits? The problem lies, quite squarely, with the myriad disparate control systems generally found in a building — all installed by different contractors as isolated parts of the BACS, with little thought of any interaction between them.
Taking this a step further, the very term M&E (mechanical and electrical) hints at the core of the problem. ‘Mechanical’ disciplines (HVAC, heating, ventilation) and ‘electrical’ (lighting, security, network infrastructure) are usually awarded to different consultants, contractors and integrators, and any ideals of harmonised control quickly gets lost in the chain.
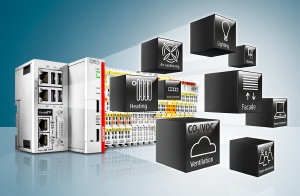
The best approach is simple — one compact, system-spanning holistic solution that uses synergies efficiently to future-proof the installation, reduce energy consumption and save valuable plant room real estate. This can be achieved only with the use of an intelligent, software-based control system that has all information from all building systems at its disposal at all times and uses this information specifically to optimise efficiency.
As well as inexpensive implementation, there are several key benefits to an integrated approach.
• The possibility of particularly fast payback time.
• Reliable future security for expansion of the building-management system, focused on long-term availability of hardware and guaranteed future compatibility.
• Seamless integration with legacy systems and networks, as long as integration is specified early in the selection of the controls system.
• Buildingautomation-specific interface terminals.
• BTL BACnet approved hardware and OPC-UA connections for easy integration with BMS head-ends.
Maybe it’s time for the end-user to take more control and help to redefine the term ‘value engineering’ into an investment that considers the lifetime operational cost of a building, rather than a short-term cost-cutting exercise during build which, ultimately, benefits no one.
Karl Walker is market-development manager at Beckhoff Automation Ltd.