The political challenge
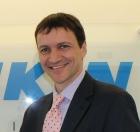
Political enthusiasm for reducing carbon emissions continues to run high. Martin Passingham of Daikin UK outlines recent building energy-efficiency legislation and how the efficiency of an existing climate control system can be improved as part of the industry’s response.
Following the international political response to climate change that began at the Rio Earth Summit in 1992, the 2015 Paris Climate Conference (COP21) was a collaboration of more than 190 countries, private-sector companies, UN agencies and NGO representatives. From COP21 The Paris Agreement was created, confirming to keep the rise in global temperature below 2 K; it further commits to pursuing the limiting of warming to an increase of 1.5 K to protect areas that are threatened by rising sea levels.
Therefore, to meet this aim, the UK Government will continue to pursue and potentially exceed its existing targets for climate change and energy efficiency. In line with existing EU legislation, all new buildings must be ‘nearly zero energy buildings’ by 31 December 2020. However, as more than a third of buildings within the EU are over 50 years old, improving their energy efficiency through refurbishment and maintenance has the potential to reduce total EU energy consumption by up to 6%.
Set out in the EU Energy Efficiency Directive, energy-efficient renovations must be made to at least 3% of Government buildings in an effort to reduce carbon emissions from older buildings. This is further supported by the EU’s Energy Performance of Buildings Directive (EPBD), which requires all buildings to be supplied with an Energy Performance Certificate and for a minimum energy performance to be set for all new buildings.
As climate-control and ventilation systems are responsible for nearly half of the energy consumption in non-residential buildings, it is crucial that building owners and managers not only understand and comply with energy legislation, but also monitor and maintain their installed system.
Therefore, enforcing the Energy Performance of Buildings Directive with specific focus on the air-conditioning system is the person who ‘controls’ the installed system. This person is responsible for ensuring regular inspections are carried out, for keeping inspection reports and for passing them on to the their successor. It is normally the responsibility of the building owner or manager, not the daily occupant, to ensure these checks are carried out and properly recorded.
Carrying out simple checks of the condition of system filters, coils and fins means that dirty, clogged or damaged components will not go unnoticed.
This is also important for outdoor units. If they are located near trees or fallen debris, the airflow around the condenser can be reduced.
Both of these checks can result in significant improvements in energy consumption. For example, replacing a dirty filter can lower the system’s energy consumption by 5 to 15%.
Another method of reducing the energy consumption of an installed HVAC system is to integrate it into the building-management system using intelligent controls. This can allow for zone-by-zone control, as well as providing the capability to automatically turn the system off or down depending on the requirements of the building and its occupants.
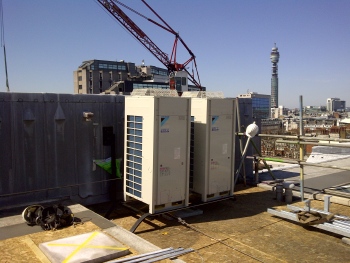
Alternatively, for situations where, for example, the system has been installed for a considerable amount of time, or if the system is using a refrigerant banned under the new F-gas regulations such as R22, a complete refurbishment would be the most energy and cost-effective solution. Therefore, when choosing a new climate-control system, one that offers total flexibility for future building changes and is a low carbon emitter would be the ideal solution.
Variable refrigerant flow (VRF*) air-conditioning systems, for example, are low-carbon solutions with high-energy efficiencies, resulting in lower energy consumption and reduced CO2 emissions.
VRF systems with inverter control to vary the speed of the compressor according to the immediate cooling or heating requirement are highly efficient. In addition, if there is a significant change in the building’s use or occupant levels, changing condensers is an option but can be expensive and disruptive, as this often involves replacing pipework, along with indoor and outdoor units. Fortunately, the modularity of VRF systems means they can be designed, built and commissioned floor-by-floor. This flexibility means they can be resized in phases, minimising disruption and installation costs.
With the UK Government and EU’s aim of creating more low-carbon buildings, building-services engineers need to help building owners and managers understand their legal obligations under the Energy Performance of Buildings Directive and the Energy Efficiency Directive.
Engineers can assist in this process by highlighting how maintenance of the HVAC system can easily reduce a building’s energy consumption.
Building-services engineers can also promote energy-efficient climate-control systems, such as those that offer operational flexibility and are based on VRF technology, which will help meet future energy-efficiency targets.
Martin Passingham is product manager for direct-expansion air conditioning at Daikin UK.
* VRF (variable refrigerant flow) is a generic term for this type of air conditioning. Daikin’s trade name is VRV (variable refrigerant volume).