Fewer volts means using less energy
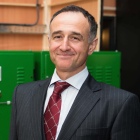
The supply voltage in the UK is often higher than required by much equipment, increasing energy consumption unnecessarily. Dr Alex Mardapittas of Powerstar discusses how voltage-optimisation technology addresses this issue.
If your site is being supplied with electricity at a higher voltage than required, you could be wasting energy and money — along with being responsible for a greater level of carbon emissions than necessary.
Electrical equipment can sometimes consume more power at higher voltages. Voltage optimisation reduces the voltage of the electricity supplied to the equipment, minimising consumption while remaining within the operating conditions specified by the equipment manufacturer.
So why might my supply voltage be higher than necessary?
Until 1995, the statutory supply specification in the UK was 415/240 V ±6% (i.e. the single-phase voltage within the range 225 to 254 V). The vast majority of the electrical distribution network has been in place for many years and was designed to deliver electricity within this range. As a result there are many sites across the UK where the phase voltage is normally in excess of 240V.
Steps to harmonise voltage levels were taken in 1995 when the statutory supply specification in the UK changed to 400/230 V +10%/-6%. This remains the current UK position.
In addition, electricity suppliers have to supply everyone with voltage levels as described above; hence they start at the highest voltage to ensure that all users have power supplied within these required levels.
Several types of voltage optimisation are available.
Optimisation of the low-voltage (LV) side corrects the over-voltage problems once power has entered the building. Typically either a fixed or electronic-dynamic system (sometimes referred to as variable or intelligent) will be implemented.
A fixed voltage-optimisation system reduces the incoming voltage by a set amount and matches the incoming voltage profile. Electronic dynamic voltage-optimisation systems set the output voltage to the optimum level and maintain this by systematically managing the peaks and troughs in the power supplied — irrespective of the incoming voltage.
Optimisation technologies on the high-voltage (HV) side offer solutions to sites that own their own distribution transformer, allowing the over-voltage problem to be addressed before power is distributed into the facility. The application requires the replacement of an old, inefficient HV transformer currently on site with an amorphous core super-low-loss HV transformer.
Many HV transformer technologies exist, but only one on the market offers amorphous core transformer technology with integrated electronic-dynamic voltage optimisation that exceeds the Eco Design 2021 efficiency specifications.
How does voltage optimisation save energy?

True voltage-optimisation systems are transformer-based technologies used to optimise the current supplied at the source (first current) according to the current characteristics required at the load (second current).
The first current is typically an alternating voltage, in which case the resultant voltage is increased or decreased, resulting in excess transformed voltage.
In a voltage-optimisation systems, the supply current flows from the first winding into the second winding, where the magnetic flux causes the induction of a reverse current, which is typically 10% of the supply current.
This reverse current flows in the opposite direction to the supply current, from where it is directed back to the electricity supply. As this reverse current is real energy, which is distinct from apparent or reactive energy, there is a direct effect on the consumption of the load. This results in a reduction of power consumed by a load, producing kWh savings.
Where can the greatest savings be made?
Optimising the voltage of all equipment across a site typically provides 8% to 12% energy savings per annum.
The greatest savings come from inductive loads such as lighting and motors, especially if they are not always loaded at 100% capacity. A building that has fixed-speed devices such as air-handling units, multi stage compressors (i.e. chillers), pumps and standard switch-start fluorescent fittings, will achieve high savings.
Some loads such as variable-frequency drives will also see savings, but at reduced levels. Some loads will yield zero savings but will benefit in other ways. When considering a voltage-optimisation system it is important to understand the electrical loading characteristics of your site and remember that no two sites are the same.
Designed, engineered and manufactured in the UK since 2001, Powerstar is a market-leading voltage-optimisation solution. We have worked with an wide portfolio of clients in the public and private sector and are recognised as industry experts able to offer thorough advice and guidance to companies looking into the viability of voltage optimisation for their sites.
Dr Alex Mardapittas is managing director of Powerstar.