Evolution never ends
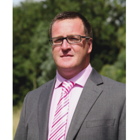
With boilers hitting the ceiling of achievable efficiencies, Gavin Watson of Elco Heating Solutions, discusses the importance of a solid controls strategy, the careful consideration of the heat-exchanger material, plus the ongoing refinements in commercial boiler design.
In March 2013, the Government outlined how non-domestic buildings accounted for 17% of total UK energy consumption, with over 60% of their energy use attributed to the delivery of heating and cooling. Since this report, we have had the monumental commitment made at the UN Climate Change Conference (COP21) last year, limiting global warming to below 2 K and bringing down greenhouse-gas emissions to net zero within a few decades. Together, these figures add up to a desperate need to update the heating systems of the UK’s 1.8 million non-domestic buildings.
The energy benefits of upgrading an old atmospheric boiler to a modern condensing unit are fairly evident. However, specifiers need to be able to recognise the underlying technology of a commercial boiler and which specific features have the greatest long-term energy-saving credentials.
Firstly, let’s address the debate over stainless steel and aluminium heat exchangers. Manufacturers on both sides of the argument have presented strong cases to each material’s benefits.
However, at Elco, we are firmly in the stainless-steel camp as the long term performance of this material is superior to its counterpart.
When you compare lifetime efficiency — which is the key aspect of any boiler installation — aluminium loses efficiency significantly during its operating window, whereas stainless steel does not suffer any reduction in performance levels.
![]() |
The heat exchanger plays a key role in maximising boiler efficiency. |
In addition, there is no build-up of sludge in the form of aluminium oxide, nor is there a corrosion on the hydraulic side of the boiler. With these potential issues in mind, specifying commercial boilers with stainless-steel heat exchangers makes complete sense for the long term performance of a heating system.
Cascade arrangements are particularly popular in the commercial refurbishment market as, very often, they reduce the overall plant footprint while offering deeper turndown ratios, improved seasonal efficiencies, lower fuel costs and a significant reduction in emissions.Of course, using a cascade arrangement requires a suitable control strategy. A cascade control system, for example, allows two or more boilers to be modulated up or down, or switched on or off when the heating load changes. This maximises efficiency, improves fuel consumption and reduces wear and tear on the boilers. Other controls to consider include weather compensation to adjust the system flow temperature relative to outside temperature variation.
For a while now, there haven’t been huge strides in condensing boiler technology, especially as efficiency levels started to hit a ceiling. However, more recently, there have been a number of smaller gains which, when combined, add up to a considerable leap forward in boiler performance. Certainly this is the approach taken at Elco, where key areas have been identified surrounding overall efficiency and the environment. Only by breaking these down to an almost atomic level can the potential gains be unlocked.
Take the design of a heat exchanger as an example. Maximising heat transfer is paramount, so utilising laser-welded fin tubes allows for the best possible heat transfer between tube and fin, as does optimising the turbulent flow of water through the coils. These might seem like simple solutions, but the design of a heat exchanger is incredibly complex and requires years of research and development — something only established manufacturers can undertake.
![]() |
Cascade boiler arrangements are particularly popular in the commercial refurbishment market. |
Another incremental improvement that has come to light is the ancillary energy consumption of a commercial boiler. This can emanate from a variety of sources, but it’s vitally important to keep resistance on the flue and hydraulic side as low as possible, as this ensures the energy consumption of main components such as the fan and the pump is minimised.
Finally, from an environmental standpoint, careful consideration should be given to the emissions of gas condensing boilers. After all, this directly leads back to the global warming targets that the UK and a hundred other nations have committed to. Consequently, the latest boilers need to be targeting and achieving the highest class of NOx emissions (Class 6). Doing so not only ensures the specification of a boiler is ecologically sound but also futureproofs the heating system it is connected to.
Taking into account all the underlying features of a new boiler at the specification stage is sure to offer long-term gains for a heating system. Major components such as the heat exchanger should always be evaluated carefully to ensure lifetime efficiency, while a solid control strategy is an essential element of any modern plant room.
Combining these aspects with the smaller incremental improvements of the latest modern units will ultimately help provide a high-quality and efficient system — one that can help meet the tough targets ahead and help deliver a net-zero-carbon economy.
Gavin Watson is sales director at Elco Heating Solutions.