Heating airtight buildings
Ambi-Rad Nor-Ray-Vac continuous radiant-tube heating offers 92% thermal efficiency and even, comfortable temperatures throughout the Enginuity Centre at Ironbridge Gorge.
The air-leakage requirements of the latest Building Regulations will have an effect on space heating systems. KEITH SPRAGUE explains how radiant and warm-air systems will fare under the new regulations.It is clear from the intention of the new Part L Building Regulations that the Government means business when it comes to reducing carbon emissions. Timed to coincide with the European Performance of Building Directives, the new Part L regulations form a 2-pronged attack on the environmental damage that can arise from the materials, construction methods and services applied to new and existing buildings.
Air leakage One of the key platforms of Part L is to improve the air tightness of buildings. A building’s design and the quality of its construction will have a major effect on the amount of air leakage. Draughty industrial and commercial buildings, in particular, are detrimental to the environment in a number of ways. The air that leaks out will often have been tempered in some way — by heating in winter or cooling in summer — resulting in heat loss or heat gain internally. Heat loss, especially when it is unforeseen or unnecessary, puts an additional burden on the heating system. A correctly-sized system may not be able to perform adequately if the leakage of air from the building is significant. Draughts and cold spots may compromise the comfort of building users, which could have a detrimental effect on staff productivity or customer footfall. Excessive air leakage can, in the worst cases, allow damp air to penetrate the building fabric — with potentially damaging consequences to the structure and insulation materials. Above all, leakage of air from a building is a huge waste of energy. The underlying aim of Part L is to reduce energy consumption; making buildings airtight is the natural first step towards this waste. Unlike the previous voluntary standard for airtightness, the requirement is now legal.
Target For non-domestic structures, an energy reduction target of 28% has been set. The benchmark against which this is measured is a ‘notional’ building conforming to the 2002 Building Regulations. The software that enables comparative calculations (SBEM and others) is an excellent method of ascertaining whether the selected heating system will achieve the required reduction in energy consumption. Approved Documents ADL2A and ADL2B (new and existing non-domestic buildings) set out the values for each element of the structure and services — for example, maximum U-values for walls, roofs, windows and doors. Assessment of air tightness of new and existing buildings over 1000 m2 is achieved by pressure testing. Air is pumped into the building to pressurise it to 50 Pa, and the escape rate is measured. Leakage rate is calculated based on the entire surface area of the building.
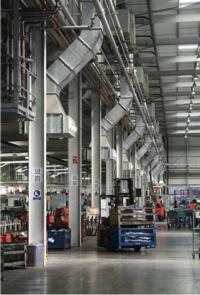
25 Reznor warm-air heaters have been fitted at different roof heights in the new 20 000 m2 Futuba Industrial factory to provide warmth and fresh-air ventilation for a complex welding and assembly operation. The factory has two open sections, each with different comfort and air-quality requirements.
For new buildings, a calculation using SBEM software will give a complete picture of the energy efficiency and carbon rating of the design, including a maximum calculation of air tightness — before construction starts. SBEM, produced by the BRE, measures the efficiency of the actual design against a hypothetical building of similar size that conforms to 2002 Part L Building Regulations. It calculates various factors, including materials used and building services, adding ‘credits’ where a particular method or choice of equipment offers energy saving benefits. It can thus offer a good guide to achieving compliance to the new Part L for radiant and warm-air heating systems.
Radiant heating Under the new regulations, all radiant heaters must have a minimum thermal efficiency rating of between 73.8 and 85.5% (gross calorific value), depending on the type of radiant heater and whether it is flued or unflued. A black-bulb sensor is also a basic requirement for all radiant systems — and carries no credits. The SBEM model calculates the efficiency benefits of radiant heating in buildings with high roofs, also taking account of the fact that radiant heating generates heat at the point of use. In a 10 m-high building, for example, this would amount to an improvement in efficiency of about 30%. Controls such as optimised shut down and zone control each add 1%. All these control options effectively limit heater usage to the absolute minimum time without compromising internal conditions.
Warm air For warm-air systems, a minimum thermal efficiency of 80% (for gas-fired or oil-fired forced convection heaters) or 90% (for direct gas-fired heaters) is required. Credits can be added for optimised shut-down, high/low and modulation burners (2% and 3%, respectively). Destratification fans, also included in the SBEM model, further improve efficiency by 4% to 6%. What is immediately apparent from these credit ratings is that radiant and warm-air space-heating systems with appropriate controls and other equipment can comply with the reduced energy requirements of Part L. In high-roofed buildings, radiant heating in particular can produce beneficial reductions in energy consumption. For both types of heating, configuration can easily be optimised to ensure savings are maximised in most large-space buildings.
Keith Sprague is with Ambi-Rad Ltd, Fens Pool Avenue, Wallows Industrial Estate, Brierley Hill, West Midlands DY5 1QA.
Related links: