Delivering greener buildings
The latest Building Regulations require carbon emissions from buildings to be reduced by about 25% compared with an equivalent building designed to the 2002 Building Regulations. Simulation software provides a useful approach to comparing the building emission rate (BER) with the target emission rate (TER).
‘Greenness’ cannot easily be added to a building at a late stage in the design process. The reduction of carbon emissions must be considered from the very beginning, and building-performance simulation software is an important tool. DAVID McEWAN explains.This year has seen an incredible change in attitude towards sustainability and energy use, both by building designers and at a wider business and consumer level. Rising fuel prices, worries over future security of energy supplies and a broader understanding of environmental impact are definitely all major contributing factors to this growing concern. However, within the building-design team the major changes to Part L of the Building Regulations, which took place earlier this year, have certainly been a significant factor in this re-evaluation. The 2006 amendments to Part L2 of the English and Welsh Building Regulations require commercial buildings to have overall emissions of carbon-dioxide 23.5 to 28% lower than an equivalent, or notional, building designed to 2002 regulations.
Thinking efficiency from the start The major perception shift required by the industry is understanding that being sustainable and having green credentials is becoming a standard requirement for all buildings. The substantial emission reduction required by the new Building Regulations for commercial properties sets the minimum standard. Those looking to achieve excellent sustainable credentials need to push further. To achieve such savings the building-design team has had to take a close look at the way it works and interacts. Designing energy efficient buildings is not just about installing renewables. It makes no sense to create unnecessary energy demand and fulfil that with cleaner energy. Building designers have to do everything possible to cut energy demand by looking at a multitude of factors — including location, form, orientation, making the best use of daylight, controlled natural ventilation, insulation, air tightness and energy-efficient services. What many have realised is that a lot of these key decisions are taken right at the very early stages of the project. Designs have previously been fully developed architecturally before the impact on energy efficiency has even been considered, limiting the scope of improvements that can be made. Changes are afoot, however, and some forward-thinking architects are starting to understand and look at how design decisions they make affect a building’s energy performance, while engineers are increasingly being involved at an earlier stage. This collaboration across the whole design team is essential in promoting a more integrated and seamless approach to building design, one where the emphasis is on the effective and intelligent consideration of sustainable issues from the very start. In addition, a building’s energy performance is often considered at a too elemental level. Complex interactions between different elements mean a more encompassing holistic approach has to be taken. Addressing these issues and getting energy efficiency on the agenda right from the word go has to be a key priority if the industry really wants to embrace sustainable design.
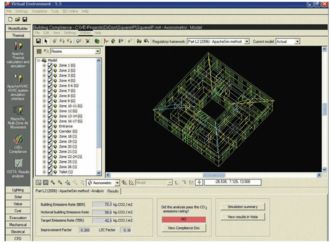
Software that simulates the energy performance of the building enables designers move away from the elemental approach of previous Building Regulations.
The use of building-performance simulation software helps designers shift the emphasis onto the building as a whole and aid closer interaction across the project team. Such software offers the tools to consider the impact of different design choices on energy efficiency, taking into account and exploring the interactions between a wide range of factors such as such as orientation, layout, form, definition of space, environmental factors and the materials and energy sources used.
Achieving compliance For non-domestic buildings and domestic properties above 450 m2 compliance with the requirements for carbon-dioxide emissions must now be proved by calculation with an approved software tool, i.e. SBEM (Simplified Building Energy Model) or other accredited simulation software such as IES’s VE Compliance tool. A key element to the regulations is understanding that it is necessary for the architect and the building-services engineer to collaborate more closely. Compliance is not just an M&E issue. If compliance is not considered when the design is being evolved, it is conceivable that costly re-design may be required later. In addition, engineers need to ensure that they really understand the principles of the Calculation Methodology and the difference between the ‘real’, ‘actual’ and ‘notional’ buildings. The Approved Calculation Methodology sets out the way to demonstrate compliance with the principle criterion of Part L2 2006, which requires an acceptable reduction in carbon-dioxide emissions. The building as a whole must be considered, with many different factors taken into account — such as the building fabric, HVAC systems, position, orientation, occupancy and usage. The ‘actual’ building is, in effect, the ‘real’ building populated with standard activity data. The ‘notional’ building is the ‘real’ building populated with standard fabric and plant data associated with the 2002 Building Regulations. SBEM is a compliance software tool developed by the BRE on behalf of the DCLG for the assessment of simple buildings against the National Calculation Method. For more complex buildings, or indeed any building, more sophisticated commercial software, approved by the DCLG, will need to be used. However, in most cases it should be easier to use such simulation software across the board, both for design and compliance, to ensure that the right design decisions are made whilst at the same time ensuring compliance at each stage. These simulation tools must encourage closer collaboration and be accessible to the whole design team. IES in particular has developed an easy-to-use HVAC wizard for its VE Compliance module that enables designers to use generic information which can be refined if necessary at a later date by the building-services engineer. In summary, the key to hassle-free compliance with Part L2 is to incorporate the principles into the design process right from the start, ensure close collaboration between the whole design team, make sure you have a clear understanding of the concept and energy strategy at the beginning and, most importantly, take the time to look at the different options.
David McEwan is divisional manager (building regulations) with IES Ltd, Helix Building, Kelvin Campus, West of Scotland Science Park, Glasgow G20 0SP.
Related links: