Enjoying the benefits of clean ductwork
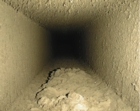
Above the suspended ceiling and inside the ductwork could lurk all manner of undesirables. It is a problem that concerns Ian Wall.
The challenge with maintaining good air quality is that because we can’t see it and can rarely smell it, we really don’t consider it or its importance to our health and wellbeing.
But the fact is that wherever there are mechanical ventilation systems, air-quality issues can arise. Dust and debris can build up, and viruses and bacteria can thrive in ducting — resulting in impaired performance at work, unhappy customers, sickness or even death.
The problem is exacerbated by the fact that there is only a legal requirement to have ventilation systems inspected regularly and the findings recorded (every 14 months for general buildings, 12 months for kitchen environments). There is no obligation to clean — only a recommendation to clean every four years or 12 months for sterile environments. This ambiguity is not helpful as, with budgets under pressure, it is too easy to put off what may be essential cleaning work.
In hospitals, highly infectious diseases like MRSA and Clostridium difficile can thrive and feed on flakes of dead, dry human skin — which is a component of hospital dust and can build up in ventilation ducts. In the workplace or public buildings, cross infection is also a problem, mould building up in ducting can cause breathing problems, and poorly maintained ventilation systems can result in loss of concentration, drowsiness, aches and pains caused by draughts, and even skin problems.
A report by the International Centre for Indoor Environment & Energy at the Technical University of Denmark states: ‘It has now been shown beyond reasonable doubt that poor indoor air quality in buildings can decrease productivity, in addition to causing visitors to express dissatisfaction. The size of the effect on most aspects of office work performance appears to be as high as 6 to 9%, the higher value being obtained in field validation studies. It is usually more energy-efficient to eliminate sources of pollution than to increase outdoor air supply rates.’
And, of course, poorly maintained ventilation systems increase energy use, which in turn can affect the Climate Change Levy.
The solution is quite simple — a comprehensive and sustained cleaning and maintenance programme for ventilation systems.
Site surveys will typically be done free of charge, and risk assessments will determine the condition of ductwork and whether cleaning is necessary. But facilities and estates managers can also monitor ducting and grilles to identify potential problems, such as the following.
• Ceiling and wall air grilles should be clean as should be ceiling or tiles around the grilles.
• There should be no discolouration marks in the areas adjacent to the air grilles.
• The temperature should be constant — not too hot or cold.
• There should be no draughts.
• The environment should not be dusty.
• Reports of anyone experiencing abnormal bouts of sneezing or nasal discomfort should be investigated.
In addition, if a clean sheet of white paper left on a desk for 12 hours overnight shows signs of dust, the ducting probably needs attention. If ducting hasn’t been cleaned in the last five years, the paper almost certainly will be dusty.

If duct cleaning is required it is essential to find a specialist to the job; duct cleaning requires much more than just a surface clean.
In choosing the right supplier, I recommend looking out for the following memberships and accreditations: HVCA; ADCAS; ISO 9001 and 4001, and Skillcard. Constructionline is a good resource for finding contractors. Depending on the job in hand, you need your contractors to have the necessary trading certificates to cover the work involved.
The whole process of ventilation ductwork cleaning and maintenance can be made a lot easier by installing the system properly from the offset. Many builders may be using the PDI Level 3 process, with ductwork delivered to site wrapped and then stored in a dust-free environment prior to installation. Once installed, the ductwork is bagged off to prevent dust entering the system prior to handover. This approach is very expensive as the ductwork has to be delivered to site as a single piece and, despite all the precautions, dust will inevitably still get inside, so the ducts will need cleaning anyway. It is much better and cheaper to have the ductwork sections ‘nested’ inside one another so they can be delivered in fewer drops and then cleaned.
When installing, allowing for adequate access is vital. Ducting should have sufficient access doors, and, while this might sound all too obvious, they should be easily accessible. I have come across plenty that aren’t, believe me.
Finally, just as it is essential to do a full clean prior to commissioning the building, careful consideration needs to be given to timing and logistics. I have seen situations where cleaning takes place and the system is commissioned before work is fully completed, resulting in construction dust being drawn into the system unnecessarily and necessitating a further clean.
Regular cleaning and maintaining of ductwork does not have to be costly. In any case, what price can you put on high productivity, happy (returning) customers, lower energy bills and the general health, happiness and wellbeing of your employees?
Ian Wall is sales director with Ductbusters.
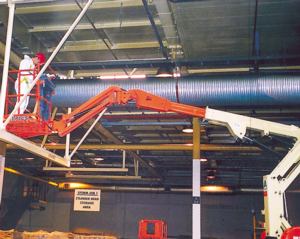