The power to reduce electricity costs
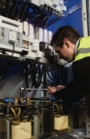
Supplying more than 220 V to most electrical equipment is wasteful of energy and can dramatically shorten its life. But the UK voltage is nominally 240 V, which is why voltage optimisers can be very attractive. Jeremy Dodge explains how.
Energy — the provision of it, the use of it and the saving of it — has been thrown into sharp focus in recent years with successive Governments pledging to deliver tough CO2 reduction targets and users facing sharp price increases.
The CRC Energy Efficiency Scheme is forcing organisations that fall within its remit to make energy cuts a board-level discussion, with the scheme requiring year-on-year CO2 reductions. It’s a daunting task and there comes a point when only ‘big ticket’ items such as CHP, photo-voltaics, solar thermal and voltage optimisation will deliver the required results.
Voltage optimisation is probably the least understood of these technologies but one of the easier and more straightforward to install. It is not quite fit and forget, but for most installations a yearly service is all that is required — Not bad for a system that can return double-digit percentage energy savings.
The basics
Voltage optimisation (VO) is a proven method of reducing electricity bills at commercial and industrial operations. It is not a new concept, but technological developments have seen new and more effective systems come to market.
Why VO works is simple. Following European harmonisation in 1995 the UK’s electricity supply was set at a nominal 230 V (+10% to –6%). Therefore power supplied by the National Grid can vary from around 216 V to 253 V but generally averages about 240 V. This is also the case for a number of other countries, including Japan, Africa, India, the Middle East and Australasia.
In contrast, electrical equipment worldwide is designed to work most efficiently at around 220 V. Over-voltage dissipates as heat and vibration within machinery and equipment, greatly reducing its operational life. Research suggests that an over supply in voltage of 10% (242 V instead of 220 V) can reduce the life of electrical/electronic equipment by up to 90%.
Voltage-optimisation systems are installed in series with mains electricity and act as an interface between the main electrical feed and the building’s power supply, reducing the voltage of electricity fed to equipment and machinery, for example from 242 V to around 220 V.
The principle is comparable to that of the National Grid pumping out electricity at kilovolt levels to strategically placed sub-stations containing transformers that ‘step down’ the power to useable levels — averaging about 240V as discussed above. But this level is still much higher than most equipment requires.
Voltage optimisation is, in broad terms, just another transformer stage added in to the supply process, albeit this time a private intervention set at specific reduction levels for the organisation the VO system serves. Electricity bills are reduced, carbon emissions lowered, and the life-span of electrical equipment increased. In short, VO systems match power supply to power demand with the resulting, beneficial, efficiencies. It is straightforward, cost-effective and results-driven. Bills can, theoretically, be reduced by as much as 25% but we find that our customers achieve between 12 and 18%.
The VO market has grown massively in recent years, and many of the systems work in slightly different ways, based on the functionality of their transformers, or offer specific advantages.
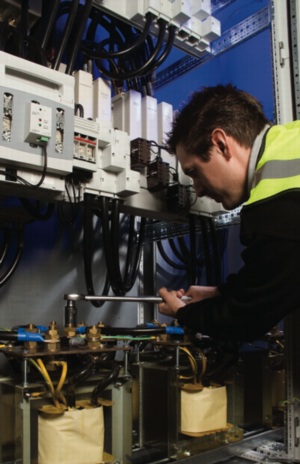
The most basic solutions step down electricity by a set, pre-fixed amount, delivering savings of around 8%. These work fine until the mains voltage drops. The VO system will continue to lower the voltage, potentially to unusable levels; the worst-case scenario is cutting all power to the facility they serve.
More modern systems use logic-controlled ‘intelligence’ to monitor incoming mains supply, removing the risk of powering down a facility and delivering savings of 15% or more. Intelligent systems work on a supply reduction ratio of 1:0.92, standard units 1:0.945.
Some systems also have an automatic bypass which allows the VO unit to switch itself into bypass mode should it detect a mains-supply issue. These units can also be serviced without cutting power to the facility, an important consideration for many clients. Fixed-output voltage stabilisation is a further enhancement that allows the output to be fixed, typically at 220 V, giving greater savings. Remote monitoring is also an important feature; meters fitted to VO units allow performance and management reporting data to be accessed remotely if required.
Selecting the right VO system will also reduce maximum-demand levels, refine power quality by balancing the phases on a 3-phase supply, reduce harmonic distortion (particularly in 3-phase systems utilising single-phase auto transformers), suppress transients, improve power-correction factors and automatically rotate auto-transformers to prevent overheating. Self-cooling (either from air movement or built-in cooling) can be specified.
When considering investing in voltage optimisation, it is imperative to understand how each of the systems work and to research the market, asking pertinent questions and requesting proof of fuel-bill savings.
Check other energy-saving methods installed at the same time as the VO system, such as low-energy light bulbs and movement sensors, and ensure savings figures are produced separately for each energy-saving element. You should also bear in mind that mains supply to site may reduce over time if new facilities are added to the existing supply, so your incoming voltage could drop naturally and having a fixed-ratio system in place could create problems.
Conclusion
Not all VO solutions are the same, and maintaining the integrity of supply to site is vital. Users need a solution that not only provides a good level of saving but also improves the quality and reliability of the supply.
Jeremy Dodge is business manager with Marshall Tufflex Energy Management.