Thinking renewables? Think early
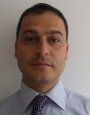
It’s never too soon to start planning renewable energy for space heating into a project if a satisfactory outcome is to be achieved, argues Firat Ucer.
Ask any heating-systems manufacturer what would make life easier in terms of working with constructors and the answer would be to be admitted to the design process as early as possible. This has always been the case, even when dealing with conventional boilers and technologies that have been around for decades.
However, renewable heating systems, including solar thermal, solar PV, CHP modules, heat pumps and biomass boilers, bring a new set of challenges — ranging from product specification, controls, system design and integration to location and housing of plant within the building. In such a relatively new market where experience and education levels of renewables are so varied, it is vital that heating-systems manufacturers are consulted at the outline design stage.
Designing heating and renewable systems with the building ensures that the correct system is specified and the required space is available for the plant. A fact that is commonly overlooked is that renewable systems often require more space than conventional heating systems. This could be a plant room for additional heating water cylinders or pumps or exterior locations for solar panels, for example.
Exploring the detail of heating options early provides a longer consideration phase in which a greater choice of products and solutions can be evaluated and which can lead to greater efficiency and savings. Viessmann, for example, can run a series of usage simulations, balancing different combinations of technologies based on in-depth technical knowledge. Architects can consider better how the use of the building could be enhanced by the heating/climate technology and factor this into the building design.
The best time to involve the heating systems manufacturer is during the concept and design development parts of the design phase. It is valuable to be able to consider feedback from the initial planning application, such as hearing that a local authority demands a further 25% reduction in carbon. This is the crucial stage, where architects and engineers draw up a list of possible alternative strategies and where the manufacturers’ influence on technology selection can have a significant impact on the success of the project.
Unfortunately, it is not always the case that the engineers are up-to-date with information on the latest technologies and systems design. Or too often, the manufacturer is brought in at the detailed design phase when key decisions have already been made — decisions that can't be changed without significant expenditure and project delay. Poorly designed plans often result in the tendering process having to start again from scratch or in a system that fails to deliver against the original objectives.
As with any new technology, awareness grows with time, and we are constantly seeing lessons being learned and fewer corrective actions needing to be made. Many of the big architects firms and their new breed of sustainability architects, as well as consultant engineers and specifiers, are gaining valuable experience and creating efficiently designed, well-specified, easy-to-maintain efficient heating systems that suit the needs of the building, save customers money and lower carbon emissions. While provisions for heating and climate control are still often seen as a ‘necessary evil’, demand for carbon reduction is being driven by customers, and this presents opportunities for both architects and manufacturers.
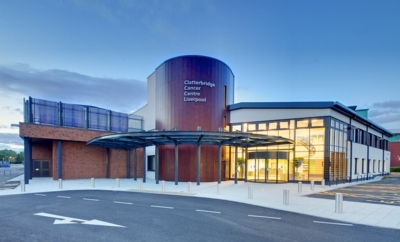
Increasingly, Viessmann is working with architects, planners and contractors to reduce the cost of heating-systems controls, reporting and maintenance. This is something that also has to be considered in the early design phase when specifying plant to budget. Through the latest, fully-integrated renewable heating controls, expensive BMS controls can be eradicated — often saving thousands of pounds in capital costs and additionally delivering substantial operational efficiency gains.
Although something of a comfort blanket to facilities managers and a popular tactic to acquire a good BREEAM credit rating, heating systems actually integrate more effectively without third-party controls or a BMS. Such integration is particularly the case when using plant from a single source, which is possible in Viessmann’s case as its product range encompasses all fuel types.
The Vitotronic range of controllers is common across the whole product range and easily ensures that all individual technologies communicate together and offer the best possible control strategy to achieve the highest possible efficiency, resulting in better energy savings, especially in weather-compensated heating systems.
Using the same control platform for all technologies sequences and allows a greater dialogue and management between the technologies for a fraction of the cost.
Many companies are successfully converted to using the heating system’s own controls, saving money by not paying for the same functionality twice. By reducing the number of suppliers, all elements of the renewable heating system are sourced from one company, and the end-user has only one point of call.
Firat Ucer is national specification manager for renewables, with Viessmann.