The bright spot that is refurbishment
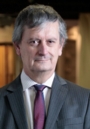
With funding and legislation coming together to support potentially the most significant building-refurbishment programme in decades, heating specialists are gearing up for an extensive programme of boiler retrofits, controls upgrades and new hot-water solutions. Ron Barker explains how this will change the industry.
The ongoing crisis in the Eurozone and plummeting stock markets have hit investor confidence on a global scale, but there are several more hopeful signs for the building-services industry. The delay to the Renewable Heat Incentive (RHI) was a blip, but as of the end of November the scheme was expected to be back on track, thanks to the quick work to revise the large-scale biomass tariff.
Alongside the RHI, a broad base of funding is now in place. The Green Deal finance will soon be available to small businesses, Feed-in Tariffs (FiTs) have boosted the solar photovoltaic market — and we should not forget about Enhanced Capital Allowances, which are a very tax efficient way of financing energy-efficiency upgrades in commercial buildings.
Even conservative estimates state that 60% of the commercial building stock that will still be in use in 2050 is already built. Assuming the ‘new’ 40% meets increasingly stringent new-build standards, it is clear where the energy-efficiency challenge lies. Interestingly, the current economic gloom may well serve to speed up the delivery of the massive retrofit programme we need to meet this challenge.
With new build stepped back, budgets are being redirected to improving and upgrading existing installed systems. Buildings account for 41% of total worldwide energy use, and 80% of that is used in day-to-day running. As energy prices continue to rise, reducing energy consumption is becoming an increasingly urgent priority for finance directors.
Building owners can make a serious dent in their running costs with a series of straightforward and low-cost steps before they have to consider more ambitious moves such as adding renewables.
For example, chillers, ventilation plant and lighting systems can be upgraded or simply re-commissioned to improve their performance, and controls can be added. In addition, replacing an older boiler with a modern one will pay dividends in terms of reduced energy costs, making payback periods very fast.
Something as basic as applying variable-speed pumps, energy-efficient lighting, DC fan coils and heat-recovery systems — alongside repair and refurbishment of existing systems will show an instant return on investment against current energy prices.
These things are not as ‘sexy’ as renewables, but they are often the best place to start. Renewables can also be retrofitted later — and with Feed-in Tariffs in place can be financially attractive. However, energy-efficiency upgrades should be carried out first to ensure that renewables deliver their full potential. There is no point fitting renewables, such as solar-thermal water heating or photovoltaic (PV) electricity generation, onto energy-wasteful buildings because the valuable renewable energy will just be wasted too.
However, it is important to think about what matters to business occupants of buildings. They do want the savings and the improved working conditions that lead to better productivity, but they also want the improvements to be made without disrupting their day-to-day operations.
So, when carrying out refurbishment works, project teams should be encouraged to use phased programmes so that only small parts of the building are shut down at any one time. This ability to phase works and keep critical facilities operating is one of the advantages refurbishment has over new build. It is also cheaper, quicker and more sustainable because existing materials are retained and reused, so minimising embodied carbon impact.
Any successful energy retrofit programme needs to start with improvements to the building fabric improvements — such as insulation, draught-proofing and glazing. Such measures will have an immediate impact on energy demand and allow access to Government funding. The next step should be to examine what controls are in the building, how they are set up and if they are easy to use.
The Building Controls Industry Association (BCIA) claims that building automation and control offers a faster payback than any other energy-efficiency measure applied to an existing building. Of course, they would say that, but there is plenty of evidence to back up that claim.
For example, heating systems are often working at too-high temperatures and cooling at too-low because of poor understanding on the part of the end user. Improved automation will let the user take some control, but will also allow the system to reset and rebalance itself to avoid long-term running cost problems. Systems can also be remotely monitored by controls specialists able to make suitable adjustments to get energy consumption back on track.
Controls will be increasingly important as we see greater use of modern techniques like heat pumps. The Energy Saving Trust identified serious problems with many heat-pump installations during a field trial last year. Many were so badly controlled that their auxiliary immersion heating was running continually. As a result users’ electricity bills were considerably higher than before they had upgraded their system — a very damaging result for our industry.
We have a job to do educating end users in how new systems work, but by the same token we must make sure we are confident that the installation is as robust as possible. We have the tools, the funding is in place, and the market is moving in our direction. Things might look pretty gloomy from the outside, but here in our sector there are several reasons to be cheerful!
Ron Barker is group product manager at Ideal Commercial Heating.