Tackling energy efficiency with effective M&R
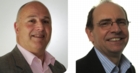
Effective maintenance and refurbishment are about delivering a comfortable environment in buildings — and reducing energy consumption and emissions. Mike Russell and Graham Child take an in-depth look at what should and can be done.
The current economic climate is suppressing development of new, low-energy buildings and major redevelopment of existing ones, so the pressure to reduce energy usage and carbon emissions must focus on the economic operation of existing building stock.
The economic factors to consider regarding building occupation and refurbishment are:
• 2011 has recorded one of the lowest ever levels of construction orders;
• Long-lease activity is becoming a less-and-less attractive option, with preferences driving towards five- and 10-year lease agreements;
• High level of unoccupied buildings throughout the UK.
These factors will influence the frequency and complexity of refurbishment activities over the next five or so years, with fewer companies committing to investment until economic recovery is more established.
Therefore compliance with ever-increasing energy-consumption legislation and delivery of energy-reduction initiatives falls even more onto the provider of M&E maintenance services.
Driving energy saving initiatives without replacing and upgrading equipment and systems is difficult. However, by ensuring the effective maintenance and upkeep of main plant and assets and controlling the occupied environment, the service provider actions become more and more critical to achieving of energy-reduction targets.
By concentrating on simple, standard operating practices, the service provider can ensure energy consumption is controlled and opportunities for energy savings can be realised using measures such as those listed below.
• Optimise the BMS, including run times and set points — a repetitive but essential process to remove unnecessary running of systems and overcooling / overheating of the building.
• Identify any simultaneous heating and cooling of areas and conflicts within the building — and then embark on systematic eradication of the conflict areas.
• Check for valve leakage. Valve maintenance and operational checks are a frequently overlooked maintenance activity, but pay large dividends on energy consumption and the efficiency of a system.
• Check variable-speed drives are correctly responding to changes in system pressure and demands.
• The monitoring and measurement of closed-systems performance, specifically responses to changing demand (valve operation with flow rates and temperature change rates) is an essential part of the upkeep and maintenance of any system. Far too frequently, valves are only checked that they open and close, without detailed checks of rates of supply against demand.
• Switch off lighting. It sounds simple, and it is, but it is effective and overlooked too regularly. Where possible install simple lighting controls (such as PIR).
• Check ventilation plant volumes and flow rates. Many are oversized and not monitored or controlled to ensure that air change rates or heat transfer rates are tailored to occupancy levels and requirements of use.
• Clean and/or change filters according to pressure drop readings, not calendar requirements. Switch to filters with low pressure drop and high dust capacity type. Several filter companies will, free of charge, undertake calculations and produce accurate energy-efficiency figures to show how cost-effective and beneficial the change to a higher-specification filter can be.
• Effective strainer cleaning and upkeep, especially the secondary strainers, assists greatly in keeping flow rates to their optimum and energy consumption under control. Differential-pressure gauges should be monitored for the requirement to clean strainers, not due to calendar schedules.
• Removing air from heating and cooling closed systems (air separators, automatic air vents) and regularly ensuring they are working, will keep systems efficient and avoid wasting energy.
Effective, specific-to-asset, maintenance activity is a key element of controlling costs, maintaining design specifications of installed equipment and prolonging asset life.
The M&E service provider in any building has a responsibility for the upkeep not just of the asset but also for evaluating and recommending the most effective maintenance strategy for the asset.
The service provider needs to ensure effective control of the following.
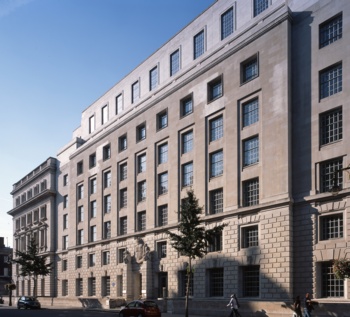
• BMS, ensuring only authorised persons can adjust settings (control of the controls).
• Optimising energy-consuming systems and equipment is part of the maintenance strategy.
• Measurement and recording of energy consumption against system performance over time to provide trend and condition indicators.
• Compliance with requirements such as CIBSE’s TM44 for air-conditioning inspections), EPCs, DECs, CRC Energy Efficiency Scheme etc.
• Managing the energy profile by optimising plant-operating schedule and temperature set points, to match output to requirements of occupancy and also maximise use of tariffs when per unit cost savings can be made. Don’t forget that occupancy requirements can change over time and that what was correct at building design may not be totally applicable 10 years later. Regular reviews are essential.
• By ensuring systems work to optimum design specification, then all systems will work with one another to reduce emissions and energy costs — thus lower operating costs.
The refurbishment of a building provides an ideal opportunity to implement a comprehensive energy-performance programme — similar in approach to the energy-performance contracts (EPC’s) being tendered in the marketplace and based on the following.
• Monitoring and measurement of systems and equipment performance requirements.
• Evaluation the effectiveness of maintenance activity against CIBSE life expectancy guidelines and analysing energy demand/consumption of the building, particularly in the light of current requirements.
• Analysing the above results to indicate further optimisation requirements.
• Opportunities from refurbishment.
• Thermal Imaging of building systems and building fabric.
• HVAC plant evaluation and suitability.
• Setting up plant monitoring systems (temperatures, flow rates, pressures, energy consumption) as part of the refurbishment package for taking into the next maintenance strategy.
• Before-and-after consumption of gas, water, electricity.
• Introducing alternative energy sources such as photovoltaic, wind turbines, heat pumps, biomass boilers etc.
• Lighting-upgrade opportunities with occupancy and daylight control.
• Provide sub-metering to monitor energy consumption at the business unit or major plant such as individual chillers.
• Installing plant and systems with inherent high efficiencies — such as boilers, chillers, chilled ceilings, 2-port valve control with variable-speed drives, ventilation systems that respond to the environments served with VSDs.
The services of an organisation which can embrace all aspects of design, installation, commissioning and maintenance are essential in delivering buildings that meet the requirements of the occupants, whilst meeting ever tougher energy targets, is now more than ever an essential requirement for both the public and commercial sectors.
Mike Russell is managing director of Banyard Maintenance, and Graham Child is a director with Banyard Consultants.