Identifying priorities

Gary Perry describes how Norland Managed Services has been helping clients to reduce their energy consumption — starting with simple and low-cost measures.
Forty per cent of the UK’s greenhouse gas emissions originate from buildings, so it is understandable that the Government is targeting both dwellings and commercial buildings to help reduce the country’s overall emissions. Building Regulations are continuously being rewritten. A building built to the current 2010 regulations is 48% more energy efficient than one built to the 2002 regulations. The 2019 regulations aim to make buildings carbon neutral.
The answer to reducing the carbon emissions of any commercial building does not always have to involve capital outlay. Updating inefficient equipment or investing in embedded renewable energy can produce dramatic results. But there are numerous low- or no-cost steps that can be implemented that can also have a significant impact, especially in conjunction with re-educating the people that occupy/ work in the building.
For example Norland launched its ‘Energy matters’ programme two years ago with the aim of reducing customers’ carbon footprints. Our approach starts with training our engineers to become energy engineers by broadening their horizons to consider wider energy efficiency. We have incorporated time within their schedules to practise this ‘energy awareness’ and to walk through their buildings and review all the energy consuming plant, and to ask three simple questions.
• If it’s on, how can I switch it off?
• If it has to be on, how can I turn it down?
• If it has to be on, how can I make it more efficient?
But for energy efficiency to really work we have to have the buy-in and co-operation of the individuals that work in the building. To achieve this, Norland has included an online module in its Energy Institute accredited ‘Energy Matters’ training for our customers’ staff. It raises their energy awareness, seeking to encourage them to replicate in the office the energy-efficiency behaviours they practise at home.
The key to energy efficiency is the effective control of plant and lighting. This includes encouraging staff to switch off lights when not needed, close windows, and not to use heating or air conditioning when unnecessary. The use of dimmable, energy-saving lighting, controlled by presence- and daylight-linking sensors will help improve the energy efficiency of the building.
But the main area we concentrate on is ensuring we have full control of all plant by reprogramming the BMS into a BEMS — the E implying energy management as well as building management. This is probably the most important energy efficiency step that can be taken and does not require a large capital expenditure.
For instance, one simple measure is to match plant and lighting times to building occupation. There is no need to turn on lighting or condition space temperatures when no one is in the building. Utilise the holiday programmer to stop plant running over bank holidays and also ensure that plant is off at weekends (if the building is used for only five days per week). Substantial savings can result.
Also, introduce strategies that take account of external conditions. This will enable the BEMS to exercise more of its capabilities.
• Adjust the air conditioning warm-up and cool-down periods.
• Change heating and cooling set points to maximise the dead band between them where heating and cooling plant stays inoperative.
• Lock out heating and cooling systems.
• Adjust flow temperatures.
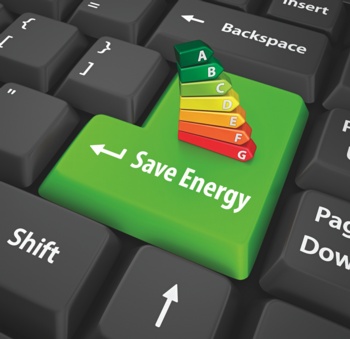
• Utilise free cooling (and heating).
• Counter anti-cycling, especially in Spring and Autumn.
• Ensure frost/fabric protection setpoints are correctly set for the application and are not raised excessively high so energy is wasted by running plant and adding heat too soon.
Reducing/increasing the heating and cooling set points, respectively, by 1 K will result in a 10% saving in energy consumption.
Having this accurate control of older and less efficient plant can often be a better solution to installing newer, more efficient plant that is not properly controlled.
Other steps that could be taken include introducing building ‘on-demand’ controls ensuring that heating or cooling only operates when a sensor calls for it. To enhance this, all heating and cooling equipment in an area should be ‘zoned’ (grouped and controlled together – ensuring that heating cannot fight the cooling).
Consider Installing variable speed drives (VSDs) on fan motors and pumps that are larger than 5kW. Install CO2 sensors in extract ducts to modulate the VSDs that are installed on the supply and extract fans based upon occupancy levels. A 20% reduction in flow equates to a 50% reduction in energy consumption.
Plant should be sized and controlled to come on sequentially. Why initiate the entire heating or cooling capacity when only a proportion would suffice? Program the system to start slowly and build up to supply only the capacity required — maintaining the required set point temperatures by running the equipment at its optimum efficiency.
The ambient temperature in the UK is below 15°C for more than 75% of the year, providing huge opportunities for free cooling. It can be as simple as introducing cool air into the building instead of utilising mechanical cooling. The overnight or early-morning introduction of cool air into a building is known as ‘purging’ and can be used to pre-cool the building in the Summer.
Another approach could be to introduce a free (dry-air) cooler into the return leg of a water-cooled chiller (although glycol/ anti-freeze will need to be added to the system to prevent freezing) so that the water can be free-cooled before entering the chiller. Ambient temperatures in excess of 3 to 5°C could result in the chiller’s compressors not being needed at all!
More capital-intensive options could include renewing older inefficient plant. This could involve replacing boilers with biomass or multi-fuelled combined heat and power (CHP) plants which burn almost anything organic from gas through to processed sewage.
Investing in grant-aided renewable energy, such as photo-voltaic solar panels, could also be considered, although the Feed-in Tariff subsidy has recently been reduced, prolonging the payback period. Ground-source heat pumps are also becoming popular considerations.
One final suggestion, which is important for all BEMSs is to ensure that sensors are calibrated regularly, as inaccurate sensors will lead to higher energy consumption.
Gary Perry is director of sustainability, energy and projects at Norland Managed Services.