When new boilers meet old heating systems
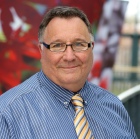
With a boiler upgrade implying modern condensing boilers, Robert Brown of Bosch Commercial & Industrial Heating, explains how modern condensing boilers can be introduced to upgrade existing heating systems with the minimum amount of upheaval for maximum savings.
For those thinking of embarking on a boiler-replacement project, the good news is that carrying out work to upgrade a system needn’t be as intrusive as you might expect. Whilst one solution definitely doesn’t fit all, there are ways and means of integrating new condensing boilers into existing systems and pipework, without the risk of any contamination of the primary boiler circuit or loss of performance.
Today, most high-performance condensing boilers need to be installed as part of a sealed system. Those that don’t still benefit greatly from being separated from an old system, where the water quality may be difficult to control.
For certain applications, conversion from an open-vented to a sealed system can be tough to achieve. Problems to consider are potential leaks from old pipework and fittings, as well as the possibility of corrosion problems if the water from an old system is allowed to circulate freely around a brand-new condensing boiler.
![]() |
Heat exchangers in modern condensing boilers are highly susceptible to debris in the heating system. |
In such situations, the most practical way of overcoming this kind of problem is to leave the existing system open vented whilst separating the boiler primary circuit using a stainless-steel plate heat exchanger. Introducing a plate heat exchanger to the system ensures a safe and protected primary circuit for the new condensing boiler, whilst also ensuring there is no risk of an increase in corrosion to the existing system at the same time.
The most usual position for the plate heat exchanger is to replace the low-loss header usually associated with modular boiler cascade systems. Fitting a low-loss header allows the creation of a primary circuit within which water velocity can be maintained at the required constant, regardless of changes or requirements in the secondary circuits. In cases where plate heat exchangers have been introduced, there is no longer a need for the low-loss header as there is now no chance of the system pumps having influence over the boiler shunt pumps.
From the point of view of control, the plate heat exchanger functions in much the same way as a low-loss header. The system strategy sensor is placed on the secondary flow, which compensates for any flow-temperature loss across the plate heat exchanger (typically at 5°C). However, it is vital that the heat exchanger is correctly sized to ensure both the correct heat transfer and hydraulic resistance can be handled by the boiler and the system pumps.
Over the years, heat exchangers in condensing boilers have become significantly more sophisticated as manufacturers have optimised designs to deliver greater outputs from highly efficient, compact exchanger units. As a result of being smaller by design, some compact heat exchangers can have small waterways that are in danger of becoming blocked if large debris finds its way in.
![]() |
The efficiency of modern condensing boilers can significantly reducing heating bills. |
Depending on the system condition, the addition of a strainer, a filter, or even a dirt separator, on the common return to the plate heat exchanger is recommended to protect the unit from debris that has not been successfully flushed from the old system. Where plate heat exchangers have been installed, the expansion vessel required to accompany the installation can be sized to accommodate the expansion of water of the small primary circuit.
This is another plus for investors, as it saves on both cost and space when purchasing a much larger vessel that may otherwise be required if a plate heat exchanger is not incorporated into the system design. It is, however, important to note that the filling arrangement will still need to comply with the requirements of the Water Regulations relating to the size of the boiler and the property — typically fluid category 4.
Finally, on the secondary side of the heating system, the position of the existing open vent and cold feed will need to be considered carefully, as the changes made to the system may mean further alterations are required. Within the new system, the plate heat exchanger effectively becomes the heat source, and therefore careful consideration needs to be given to the positioning of the open vent and cold feed in relation to the existing heating pumps.
Although clearly there is a lot to consider where any installation work is undertaken to improve the efficiency of a current heating system, above all it is reassuring for investors to know there are ways and means of managing the process within existing parameters to make it as smooth and effective as possible.
Robert Brown is technical manager with Bosch Commercial & Industrial Heating.
For more information on the products and services offered by Bosch Commercial and Industrial Heating, call 0844 892 3004 or visit the link below.