BIM and facilities management
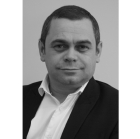
Ged Smith of Waldeck Consulting, discusses why BIM is central to effective facilities management.
Few can deny that Building Information Modelling (BIM) is now central to the construction process. In fact, the recent enforcement of the government’s BIM Level 2 mandate means all publicly-funded projects must be procured on a BIM compliant format.
And for good reason. BIM’s benefits stretch from ensuring notable cost savings to supporting health-and-safety objectives. BIM combines graphical and non-graphical data on a common data environment — a secure virtual space where all project data is correlated and housed.
Through creating an intelligent 3D model of a facility prior to construction, contractors can detect potential infrastructure clashes, ensure accurate procurement and work more collaboratively.
With BIM proving its worth at construction-phase, a new question emerges. How can BIM support safer and more efficient facilities management?
The answer lies in project lifecycle management (PLM), which directly interfaces BIM with product lifecycle management. PLM provides a complete digital solution, supporting feasibility and planning, design and development, construction, operations and, crucially, facilities management.
In simple terms, PLM ensures the benefits of BIM are felt throughout a facility’s lifecycle — not just at construction phase. Detailed tagging of assets — which encompasses everything from make and diameter of pipes to the maintenance needs of ventilation systems — is directly interfaced with a site’s facilities management programme. This creates a ‘digital twin’ of a facility — enabling real-time analysis and insights, as well as the ability to model potential scenarios.
The benefits to facilities managers are wide-ranging. However, there are core parts of facilities management that PLM transforms.
One is that costly errors and overruns are entirely avoidable. When BIM data is plugged into a facilities-management system, the transfer of data is seamless. Human error, such as incorrect inputting of figures, is avoided.
Operators possess a full digital map of a facility, which multiple people can work into. This supports an efficient and collaborative working environment, ensuring that all parties are updated on maintenance requirements and that there is no doubling up of tasks.
The benefits of knowing the exact manufacturing code, size and location of each element of the building’s infrastructure are huge. Gone are the days of engineers spending valuable time identifying replacement parts and pinpointing locations of faulty hardware. Faults are flagged immediately, if not before they happen, and operators can be alerted remotely. Correct parts and part numbers are ordered immediately, and no further damage or wasted time is incurred.
PLM also helps to control energy usage, ensuring parts are working efficiently and guarding against wastage.
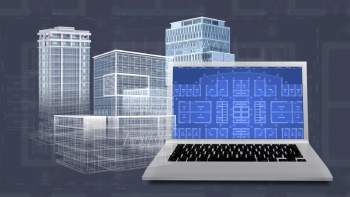
Avoiding errors and more efficient, collaborative working ensures substantial cost savings. Introducing PLM at the start of a project will add to savings already achieved by BIM, with some early adopters claiming capex savings of up to 20%.
The data that PLM provides also directly supports responsible health-and-safety provision.
High profile, dangerous health and safety concerns, such as Legionnaires’ Disease, can be eradicated through comprehensive data storage. Ventilation systems are easily monitored, with instant alerts to warn when servicing is required.
Previously unforeseen issues are identified well ahead of time as the PLM system contains intelligence on when parts require replacement. This directly avoids any malfunctions that can generate risk to a building’s inhabitants.
In addition to these benefits, easy identification of faults means that fewer engineers are required on site. In fact, many maintenance needs can be controlled remotely. Fewer engineers on site means fewer opportunities for injury — directly supporting health-and-safety policies.
The substantial benefits of PLM for facilities management are clear. The question is, will it be embraced? Uptake of BIM was slow, mainly due to fears over the upfront cost rather than recognition of the long-term savings. However, with the Government increasingly championing the development of digital skills, the construction industry is starting to recognise just what a difference this technology can make.
Thanks to 3D laser scanning, it’s possible to reverse engineer a PLM system on any building. However, the most cost-effective option is for every asset to be prepared for PLM from inception.
If companies adopt PLM now, the future is a safer, more efficient and far more cost-effective facilities management landscape.
Ged Smith is director of digital design at BIM and engineering consultancy Waldeck Consulting