Legislation develops to favour thermal wheels

ErP legislation is changing the way the industry looks at the thermal wheel. Once thought of as costly when considered alongside other heat recovery systems, they are now growing in popularity, as Chris Jones of Fläkt Woods explains.
Accounting for around 15% of the total energy consumption in the EU, heating and ventilation systems present an excellent opportunity for significant energy savings within a building. Recognising this opportunity, further changes to the Ecodesign Directive will be introduced from January 2018, which will see higher efficiency requirements for energy-related products (ErP).
Adopted by the EU in 2009, The Ecodesign Directive 2009/125/EC applies to energy-related products sold in the domestic, commercial and industrial sectors in the European Economic Area. The directive involves dozens of product groups, called ‘Lots’. Last year, a requirement was introduced in accordance with Lot 6 for all ventilation units with two directions of airflow to have a heat-recovery system. The minimum levels of efficiency in heat recovery were also increased. From January 2018, in order to obtain a CE mark and be legally sold, ventilation units in the EU market will need to achieve even higher efficiencies.
In an air-movement system, crossflow plate heat exchangers, run-around coils or thermal wheels are used for heat recovery. Due to the changes in the ErP regulation, thermal wheels are now the most effective solution, principally because the costs associated with compliance for wheels have not dramatically increased, and they are inherently more efficient.
Let’s look at this in more detail.
Historically, the crossflow plate heat exchanger was a popular choice, being largely regarded as the ‘go-to’ product when heat recovery was required. This was mainly because it was a relatively low-cost solution — but this advantage has been lost in the drive for higher efficiency.
To meet the requirements of ErP now and beyond, crossflow plate heat exchangers have had to become more efficient, but this means they have increased in size and cost. With costs rising and such heat exchangers still being less efficient than thermal wheels, we are starting to see them being phased out.
The ErP regulation applies to AHUs used in existing buildings as well as new-build projects. Therefore any replacement AHU with a crossflow plate heat exchanger would need a plate of a minimum 73% efficiency when the new ErP legislation comes into effect. This would require a lot more space than an existing unit, which is likely to have a heat recovery efficiency of only 50% in line with Approved Document Part L of 2013, so replacement AHUs may not fit into existing spaces.
The cost of run-around coils has also increased significantly in line with ErP, with design and manufacturing changes again being required to improve efficiencies. In the past, run-around coils offered only 45% efficiency. Upcoming ErP changes require these systems to increase their minimum thermal efficiency to 68%. As a result, run-around coils are probably only going to be considered where building geometry precludes thermal wheels.
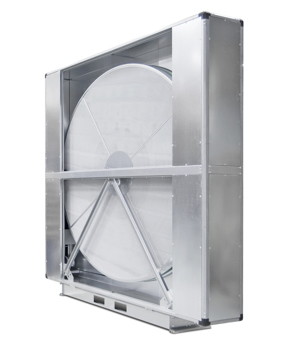
In comparison, the thermal-wheel efficiency required by Part L 2013 was 65%, so meeting the new ErP requirement of 73% has resulted in a much smaller increase in unit costs, if any, as wheels have always been typically over 70% efficient. This makes thermal wheels the most cost-effective and efficient heat-recovery device available on the market today.
In addition, thermal wheels can easily be manufactured to achieve a heat recovery efficiency of 80% — maximising heat recovery for UK design conditions according to the Carbon Trust, and resulting in the lowest possible life-cycle cost for the AHU.
Historically, one concern specifiers had about thermal wheels was contamination. Recirculating contaminants is undesirable and can cause a build-up of odours and an unhealthy environment, which is a concern for some applications such as offices, healthcare facilities and schools.
Advances in manufacturing methods have, however, minimised this risk.Fläkt Woods’ RegAsorp thermal wheels, for example, feature a 0.3 nm (1 nm is 10-9 m) molecular sieve coating, which has the unique ability to limit adsorption to particles that are smaller than around 0.3 nm. Because water vapour has a kinetic diameter of 0.265 nm it is strongly attracted to a 0.3 nm transfer media. Practically all substances that are regarded as contaminants in the air-handling context are larger than 0.3 nm, so they pass through the heat exchanger and are carried away with the exhaust air.
In practice this results in a rotor with a high overall energy efficiency, which is not only ideal for regular ventilation requirements but also applications like hospitals and research laboratories (traditionally known as hygiene applications) as there are no negative effects on the indoor environment due to cross-contamination.
With Lot 6 increasing the cost of crossflow plate heat exchangers and run-around coils, the gap between these solutions and thermal wheels is closing. The latter was once considered a more expensive choice. It has now become a financially viable option for both standard and hygiene applications, without the risk of cross-contamination.
Chris Jones is specifications engineer and national AHU product manager at Fläkt Woods Group.