Controlling the cascade

When operating heat sources in cascade configuration it’s important to design and configure the system to get the most from each source. Kevin Stones of Hoval explains.
There are many factors to consider when designing a heating system, ranging from the type of plant to be used through to the predicted variation in heat loads of the building. The latter is particularly important in modern or recently upgraded buildings where good thermal performance of the building envelope results in considerable heat-load variation.
Moreover, many organisations now experience considerably more change than used to be the case, so that a commercial building’s usage commonly changes considerably during its life. Occupancy changes will inevitably result in changed demand for domestic hot water and space heating.
Achieving the required level of flexibility to meet such variable heat demands efficiently has led to increased use of cascade systems, often pre-fabricated and supplied to site as a kit. Such a kit might comprise several wall-hung modular boilers — each capable of modulating — along with low temperature hot water (LTHW) and gas pipework header(s), inter-connecting flexible LTHW and gas pipework, pumps and valves.
Also, some cascade systems may incorporate other heat sources such as combined heat and power (CHP), heat pumps and solar thermal.
With all cascade systems, be they just boilers or a mix of heat sources, controlling each source to maximise efficiency is essential. And when this is achieved the result is a highly responsive and adaptable system.
A primary purpose of any such control strategy must be to maintain the design temperature differential (ΔT) between flow and return water temperatures. Failing to do so will result in frequent on/off cycling that reduces efficiency, increases emissions and reduces the life of the plant.
Where the cascade system is only using modular boilers, these should either modulate to meet the heat load or come on at low-fire initially (depending on whether a modulating or high/low burner is being used).
Where there is a mix of heat sources, the same principle applies — though in such cases the boilers will typically be ‘topping up’ low-carbon heat sources. For example, a popular and highly effective combination is to use gas-fired CHP alongside gas-fired boilers. The CHP is typically used to meet base heat loads, and it’s important to ensure there is sufficient base heat load to allow the CHP to run for at least three hours each time it fires. This will increase the amount of onsite electrical power generation as well as optimising the CHP plant.
Until relatively recently such arrangements were confined to projects with high heat loads to ensure the required run-times. Now, however, the introduction of smaller CHP units, with capacities as low as 20 kW thermal, enables buildings with lower heat loads to take advantage of this combination. Some smaller units also have lower maintenance requirements than higher-output CHP units, which has additional benefits for lifecycle costs.
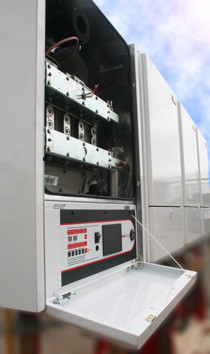
As noted earlier, a building’s usage will often change during its lifetime so it’s important that the heating control strategy is fine-tuned to reflect this and maintain efficient performance. Or the heating system may have been commissioned initially when the building was still in a shell-and-core phase and will need to be re-commissioned when tenants move in. If this takes place over an extended period, as is often the case, the system may need to be re-commissioned several times.
Consequently, such re-commissioning needs to be straightforward — otherwise it will either prove expensive for the building owner or may not get done at all!
When a heating system comprises only modular boilers this re-commissioning is indeed quite straightforward and can form part of the routine maintenance. When other heat sources are introduced things can get more complex, with a requirement to ‘tweak’ different controllers on different types of plant.
To address this issue, there are now controllers available with new levels of modularity and connectivity that make re-commissioning very straightforward, even when multiple heat sources in cascade configuration are in use.
Ideally, such controls also enable remote monitoring so that the performance of the system is easily assessed and any performance metrics that fall outside design parameters can be quickly addressed. This is a useful feature for managers of large building portfolios and for service providers that have guaranteed a pre-defined energy performance.
All of which comes back to the first point made in this article — namely that these issues should be anticipated and addressed in the early design stages and reflected in the specification of the plant. In this way the end client will get a heating system that meets both current and future requirements.
Kevin Stones is engineering and service director with Hoval Ltd.