Small space, big output
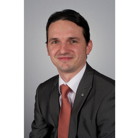
Plant room space restrictions can cause problems when replacing old atmospheric boilers. Jonathan Grist explains what to look out for.
At a time when technological advancements in space-heating are bringing energy efficiency improvements and lower gas bills, there are many buildings in this country where a surprisingly basic difficulty threatens to get in the way of progress. When old, inefficient atmospheric heating boilers have to be replaced with modern gas condensing boilers, it often becomes apparent that the existing plant room cannot accommodate the new boiler (or boilers) and ancillaries.
Particularly in older buildings where architectural heritage must be respected, plant rooms with awkward access, limited floor area, or low ceiling height can make the job of updating boilers difficult or impossible. One solution is to relocate the plant room, but this is disruptive, expensive, and not always feasible. Other answers, however, are sometimes available.
![]() |
It’s possible to replace old equipment with high performance boilers even in a small plant room. |
Why boiler choice is limited
A low water content boiler (which typically holds 0.1 to 0.06 litres of water per kilowatt of output) can only achieve its minimum necessary flow rate with the assistance of hydraulic parts such as circulation pumps and, for larger output boilers, a by-pass or low-loss header. To maintain a constant flow within the boiler circuit, a relatively high proportion of the water is diverted back to the boiler (at high temperature) via the low-loss header. But this process isn’t ideal: it inhibits condensing levels and therefore has a relatively low level of efficiency. Another undesirable consequence is that running and maintenance costs will be higher, because of the ancillary components.
A high water content boiler (which typically holds 0.6 to 1.4 litres per kilowatt) makes much better use of the condensing effect, with no need for the full flow rate once the boiler’s design temperature is attained. And because high water content boilers accommodate variable flow, there’s no requirement for minimum flow and no need for shunt pumps.
Another advantage of high water content condensing boilers is that some have two return connections, allowing bigger systems with different temperatures to be connected at different points at the boiler. A second return connector for low return temperature (down to 30°C) results in the boiler operating at the lower condensing output temperature, allowing the water returning to the boiler to be significantly lower than the gas dew point (57°C). This means the system can extract the latent heat in the water vapour of the combustion gases in the flue, producing condensate and improving operational efficiency by up to 9 per cent.
The need for a high flow temperature generally rules out wall-hung boilers, which have flow temperatures of 75-80°C - but the flow temperatures of 95°C generated by floor-standing boilers and their ancillaries come with the need for additional space which might not be available. It’s worth knowing, though, that wall-hung boilers in tight plantrooms are in fact now an option, because the recently-introduced Viessmann Vitocrossal 100 is a floor-standing gas-fired condensing boiler with a small footprint small enough to make a critical difference in tight situations.
![]() |
Newer boilers perform better and are also easier to maintain in the long-term. |
Other considerations
In addition to determining the maximum acceptable dimensions of the heat generator, there are two considerations when modernising a plantroom with a gas-fired condensing boiler. One is the flue piping which extracts gases to the atmosphere, the other is the need to drain condensate.
Older, atmospheric boilers allow the natural draught to pull flue gases through the system and have larger-diameter flues designed for low-resistance. Modern boilers, on the other hand, employ a fan to push the flue gases through, with a smaller-diameter flue creating positive pressure at the flue outlet and running lower flue-gas temperatures. This means flues will usually need replacing during the modernisation, taking care that the condensate steam exhaled into the outdoors air doesn’t cause a nuisance.
Condensate from the boiler itself is slightly acidic (typically 3.5 pH) but can be disposed of through the drainage system via an internal waste pipe or stack pipe or externally via a drain or purpose-made soakaway. With external drains the condensate pipe will have to be insulated so that it does not freeze, which would cause the boiler to automatically take the precaution of shutting down. To reach a distant drainage point might require the assistance of a condensate pump.
So it’s true that older buildings with small plantrooms can be a challenge - but by starting with a detailed survey of the room and taking into account the factors identified here, a good commercial heating engineer will find a solution.
Jonathan Grist is commercial sales director at Viessmann UK