Put to the test - fire safety system performance under real-life conditions
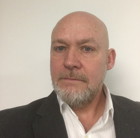
The culture change called for by the building regulations review following the Grenfell Tower tragedy is already driving demand for more rigorous fire safety testing, according to Andrew Collard
The interim report published by the independent Hackitt Review, which was appointed to look into the effectiveness of the current Building Regulations and fire safety measures following the Grenfell disaster, did not pull any punches.
According to Dame Judith Hackitt, who is chairing the review process, there needs to be a complete culture change so that the focus switches from doing work for the “least cost” to ensuring that all buildings remain safe throughout their full operating life.
Dame Judith called for new regulations and criticised the complexity of the guidance documents used to support the regulations, which she described as flawed and overly detailed. She said the documents were well intentioned, but “difficult to penetrate” and open to misinterpretation. In particular, she called for an immediate update of Approved Document B, which covers fire safety.
This has already increased desire across the construction industry to seek clearer understanding of the current standards and testing requirements for dampers and smoke ventilation specifically. The emphasis has already begun to change, with consultants and contractors now more concerned with achieving a compliant and fully tested installation.
Rigorous
The Hackitt Review says designers of tall buildings should not rely on compartmentation to keep people safe in the event of a fire and, therefore, there should be more rigorous testing and certification of products. Compartmentation is often breached by changes to the building in use so more risk-mitigating factors are essential. So, there should be a focus on testing smoke ventilation systems; fire and smoke dampers; and sprinklers.
London Fire Brigade chiefs have highlighted a “general lack of competence” across the construction sector in relation to fire safety measures. They are demanding the creation of formal qualifications and accreditation for anyone installing “life-saving systems like smoke ventilation”.
![]() |
Physical testing provides reassurance about fire system performance |
“There will be an increase in serious building fires unless the construction industry starts to take fire safety more seriously,” said an LFB submission to the Hackitt Review. “The responsibility for ensuring buildings are constructed with proper fire safety measures sits with the construction industry and yet a general lack of competence means that dangerous decisions are being made about buildings’ design or construction.”
Fire officers reported regularly noting “significant construction defects” in critical fire safety systems, such as mechanical smoke ventilation, that were either not installed as per the original design, poorly designed, or simply not working.
All of this reinforces the importantance of physical testing of systems to support improved competence, knowledge and skills around life-safety systems such as fire and smoke dampers; fire-rated ductwork; smoke ventilation; and the pipework for fire sprinkler systems.
Dame Judith believes there should not be an over-reliance on ‘desktop studies’ to establish the safety of building designs and called for more detailed information about the fire safety performance of different design features to be handed over by the installation and building teams during new build or refurbishment projects.
Building control officers will be given more responsibility to ensure adequate information is provided by construction teams and that means they must have comprehensive testing data at their fingertips.
Physical testing
At Swegon Air Management, we have already seen a marked shift in demand from the industry for more physical testing of products and fire safety installations. We are also receiving record numbers of enquiries for technical assistance regarding the correct installation methods for our dampers.
Our Research & Development (R&D) Academy in Whitstable, Kent is becoming more popular with consulting engineers, contractors and building clients as specifiers look for greater reassurance about system performance.
Despite the increasing sophistication of simulated testing via computer models, there is still a strong demand for physical test facilities because there can be significant inconsistency between different models even using the same input data. A physical test recreates actual conditions and shows the engineer or client how their equipment will respond in reality.
Swegon hosts monthly invitation days at the Academy where visitors witness product demonstrations, including best practice fire and smoke damper installations, and take part in training in the installation of products to the tested methods. The events also allow for discussion around issues of safety and energy efficiency.
![]() |
Recreating actual fire conditions |
Engineers and consultants, in particular, could benefit from more exposure to physical demonstration of their designs. The way our industry’s supply chain works means that they are often kept remote from the real- life performance of the systems they specify.
Where designs are partially developed, and then passed to the contractor to be finalised and installed there can be a lack of understanding of what is typically required. Coupled with cost constraints this can limit the intended effectiveness of the original outline design. By witnessing a physical test and influencing how the bespoke conditions are adjusted, the consultant can be as close as possible to seeing their ideas in action.
The Local Authority Building Control body pointed out that its members often had no way to identify or check what was delivered to sites. That is unacceptable and the industry must ensure robust and easily verifiable test data is available during installation, commissioning and handover.
The changes called for by the Hackitt Review are creating a significant shift towards more comprehensive testing and a more thorough design process to support the increasingly rigorous professional standards that will emerge once the final report is published this spring.
Andrew Collard is Actionair product manager at Swegon Air Management.