Design for performance
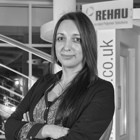
Good design is at the heart of good performance when it comes to district heating schemes. Alexandra Ivanchuk highlights the key points to bear in mind to get the most out of this form of heating.
District heating is experiencing a renaissance, as the government, local authorities and developers see the potential for modern heat networks to reduce energy consumption and lower fuel bills – particularly in areas where fuel poverty is commonplace. While we know modern systems are more efficient than their post-war counterparts, to ensure they deliver the best efficiencies possible, scheme design is everything.
In the UK, district heating became popular after World War II, providing heat to some of the large residential estates built to replace those damaged in the Blitz. Unfortunately, many of these early district heating systems were inefficient and part of poorly conceived schemes, so their roll-out was limited. But with the government now looking at ways to reduce the carbon emissions from heating our homes and buildings, district heating has made a comeback.
So how can specifiers get the most out of their modern heat networks, and avoid the mistakes of the past?
Let’s start with heat losses. In the past it was fairly common practice to oversize networks and in some cases use uninsulated pipes, but we now know this means potential efficiencies are only realised in part, or not at all. There are networks in operation that run with heat losses of over 25%, costing operators more in both energy use and running costs and having a negative impact on the end users. This is certainly something to avoid.
To minimise heat losses, we always advise verifying the heat load for the installation in the first instance. By getting to know your customers and their energy habits upfront, you can draw up an accurate load profile. This can then be used alongside thermal modelling of the building you are heating, so the exact anchor load for the network is known. No need to oversize.
![]() |
Pipes with superior insulation reduce heat losses |
In reality though, all connected buildings will not require their maximum theoretical heat load at the same time, so the anchor load can be reduced by using a diversity factor. Experience tells us that diversity in real heat networks typically ranges from 0.9 to 0.7. With a diversity of 0.7 the heat load used for pipe sizing can be reduced by 30%.
Network heat losses can also be attributed to inefficient building fabric and hydraulic imbalances in the system. So, if you are retrofitting a heat network, it is worthwhile looking at the thermal efficiency of a building and considering whether upgrades are necessary before installing the district heating.
Similarly, addressing the hydraulic balance of the system from the outset will ensure an even distribution of heat energy between residents, and produce lower return temperatures to minimise heat losses and by this increase the temperature difference between flow and return.
Most new district heating networks are considering technologies such as gas CHP but we are seeing an increasing trend in our designs for low carbon heat sources such as water source heat pumps or waste heat from industry.
In theory, we can achieve good cost and maximum energy efficiencies by minimising heat losses and closely matching a network’s load to its output. However, to achieve these in reality the layout of the system and the materials used must also be carefully considered.
One of the most popular heat network designs uses a primary spine, which is directly connected to the energy centre, and a series of secondary spines to transfer the heat to individual buildings. These secondary spines should be shorter in length, which allows the designer to take away part of the heat load from the primary spine and size secondary spines with higher pressure losses, thus reducing pipe diameter.
With a large network of pipes in the ground, minimising heat losses into the surrounding soil is crucial and there are several key ways to achieve this. Firstly, consider using pipes with superior insulation; the level of insulation in relation to the carrier pipe size plays a significant role in achieving lower heat losses and reducing overall energy costs. Increasing pipe insulation by one or two levels will lead to an increase in costs, but this investment is often recovered within the first 10-15 years of operation.
![]() |
District heating is experiencing a renaissance in the UK |
Every heat network has two pipes (flow and return), so another solution is to use a twin (or DUO) pipe, rather than two separate ones. Twin pipes are increasingly used in specifications because heat losses can be around 30 per cent lower than a single pipe equivalent. They also require a much narrower trench, cutting civil engineering and material costs during installation.
Thirdly, lowering the flow temperature will reduce the heat losses. The recommended temperature according to CIBSE CP1 is around 70ºC and in practise sometimes even lower.
Rehau’s Rauthermex, for example, has excellent thermal insulation properties particularly over long pipe runs, thanks to its polyurethane foam insulation and a corrugated outer jacket.
With so much to consider, it’s worth getting a partner on board to help guide you through the design and specification process. Look for BIM-ready businesses with CIBSE-approved heat network consultants and the software to design efficient district heating systems.
The long-term energy and performance efficiency of any district heating network is dictated by the quality of the design and the specification of the components. By optimising the efficiency of every element in the design, it is possible for heat networks to become viable even in lower density population areas and help the UK meets is carbon reduction targets.
Alexandra Ivanchuk is technical team leader District Heating for Rehau