Making space for tall buildings
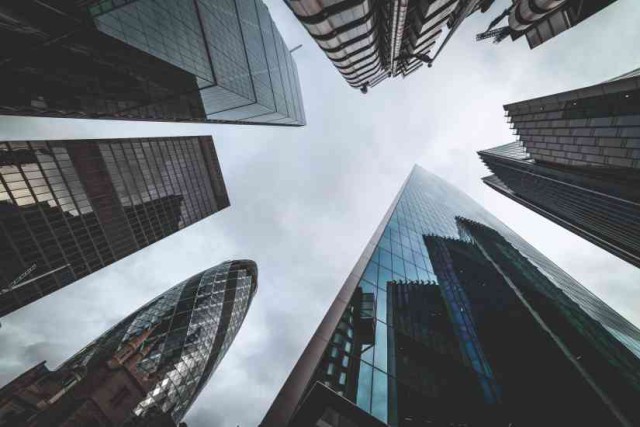
The construction of office and apartment blocks in UK cities may have stalled during the pandemic but, as the sector rebounds, a new era of ‘hybrid working’ means new office builds will have to create more internal space while apartments may be designed with home-working in mind. Jonathan Greenwood explains.
New office construction in London rose by 20 per cent in the six months to March 2021, (according to Deloitte’s Crane Survey) but 56 per cent of the new projects were refurbishments, as companies repurpose their offices for the new hybrid model with staff working partly from home.
A survey by commercial estate agency Cushman & Wakefield and George Washington University found that 80 per cent of businesses are expecting to switch to hybrid working in the future.
In Manchester, meanwhile, Deloitte reported a resilient market for apartment building with 4,914 new homes delivered to market in 2020, the highest number recorded in the city in a single year.
Pre-fabrication more common
Using off-site prefabrication has become more commonplace when constructing tall buildings given the small building floorplate and overall building footprint. Often in a tight, city centre location, there is very limited space to deliver goods and carry out work on-site. Developing sections of the building utility services off-site to allow rapid delivery, craning and installation makes the construction process faster and more efficient.
Modular construction allows fast building and adaptable flexible design with adjustable walls and screens. Off-site manufacturing also reduces the chance of on-site contamination for construction workers and increased significantly during lockdown.
To create further valuable space to assist with proximity measures, sites will need to reduce the footprint of materials stored and managed onsite turning to the supply chain to deliver more components just in time.
Trouble with high buildings
In Manchester, the 28-storey Axis Tower is positioned between a canal and locks, a critical city centre junction between Whitworth Street and Lower Moseley Street, as well as the tram tracks serving Deansgate Castlefield station. The development is 93 metres high and is currently the 12th highest building in the city.
This footprint is exceptionally tight, just 3,200 square feet, and the base of the building is so small that the upper 25 floors of the structure cantilevers over the adjoining canal.
This provided a challenge in managing water from the top of the building, through the bottom of the structure, without relying on an extensive network of pipes. The design of the system also required a reduction in additional secondary stack pipework.
Polypipe Building Services worked with primary contractor Russell WBHO and Quartzelec to develop a new system to combat these issues.
The positive pressure reduction device is used to mitigate the effects of positive air fluctuations in the drainage pipework system, such as when a toilet is flushed on an upper floor. The system was stress-tested on site to a flow of 360 litres per minute.
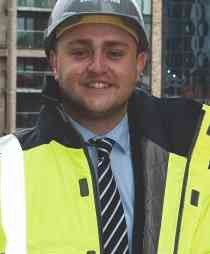
Removing the need of a secondary vent reduces the drainage pipework system footprint. This, in turn, allows for greater flexibility in the layout and design of internal drainage systems for engineers, architects and design professionals. This increased flexibility means that building designs, as well as room layouts, are no longer dictated by strict pipework systems.
Sites constrained by roads
Also in Manchester, Aberla M&E started work on a new development in Old Trafford in 2020, and we provided an array of key services to help make the best use of limited time and space. The £72m No1 Old Trafford development consists of two towers, 15 and 18 storeys, across 214,000 sq ft on the waterfront at Old Trafford. The towers are made up of 354 apartments including six penthouses.
Again, due to the site being constrained by roads, existing buildings and waterways an offsite solution was required.
Offsite fabricated water supply kits were delivered. Floor by floor, stillages of the lightweight material were craned to each level and installation could be carried out by one person. The ease of install of the system also allowed skilled labour to be freed up to work in other crucial areas on the site such as the plant room.
This type of technology helps to save M&E contractors and project managers up to 75% of on-site install time on complex water supply systems when compared to traditional installation methods.
This method allows for customised solution for complex buildings to be designed, developed, manufactured and tested before reaching site, ensuring that a sustainable drainage stack can be delivered to the high-rise building.
Tall buildings are, by nature more time-consuming and expensive to construct than low-rise counterparts and need specialist, bespoke solutions.
While hybrid working has become the norm for office workers it could be that blending off-site and on-site processes – fabrication, project management and logistics - will become the solution for M&E contractors when time, and space, are tight.
Jonathan Greenwood is Strategic Project Manager at Polypipe Building Services