Rethinking fan speed optimisation to drive greater VAV efficiency
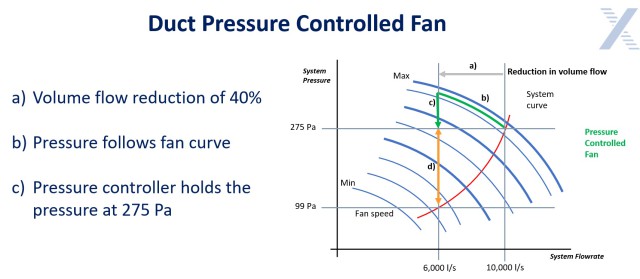
Digital technology has opened up significant opportunities for the reduction of energy consumption in air conditioning systems. Variable Air Volume (VAV) systems in particular have derived enormous benefit from digital control. If your current control methodology is based along traditional lines however, Ian Thomas of Trox Uk suggests there could be valuable additional energy savings waiting to be unlocked.
This article outlines an alternative approach to the control of fan speed in VAV systems which has delivered an additional 45% reduction in energy consumption (actual projects rather than theoretical simulations). By exploiting underutilised communication capabilities of digital control, this approach drives down energy consumption by employing damper blade positioning to optimise fan speed more effectively.
Current methodology
In today’s VAV systems fan speed is typically controlled via duct pressure measurement, utilising pressure transducers to measure duct pressure and manage fan speed. If demand reduces, the damper closes to reduce the volume flow. This causes system pressure to rise, following the fan curve. In constant duct pressure systems, the controller addresses this by reducing the fan speed and reducing the system pressure to drop back to the set point (275 Pa). See Figure 1.
A disadvantage of this approach, however, is that when volume flow is lower (to meet the building’s reduced demand), the set point of 275 Pa, which is being maintained by the controller, is no longer appropriate in terms of the characteristic fan curve. A more appropriate set point, to follow the curve, would be 99Pa.
A number of benefits are being missed as a result. Firstly, as constant duct pressure control forces a pressure drop to return system pressure to the set point of 275 Pa, the VAV units have to create the pressure that is not needed, involving a degree of energy wastage. Secondly, by creating a deviation from the characteristic curve (maintaining a set point of 275Pa, rather than the 99Pa that would better reflect the curve), constant duct pressure control forces the system to operate in its least effective working area (damper position below 40% open). This impacts on the acoustic performance of the system, elevating operational noise, and requiring higher energy consumption to meet the same load. See Figure 2.
More effective methodology
In systems incorporating the latest generation VAV technology, there is the opportunity to rethink fan speed control using damper blade positioning to avoid the problems inherent in constant duct pressure systems. This involves exploiting the communications capabilities of the VAV technology more effectively.
VAV units are now readily available with BMS protocols including BACnet ms/tp, Modbus RTU and KNX. However, most projects today install VAV controllers with analogue 0-10v communication, and fit a local digital BMS controller to control the VAV via analogue signals. This limits the amount of data that can be communicated.
A more effective methodology is to use a digital VAV controller, making all data available digitally over the BMS network. As digital control technology provides the opportunity for increased levels of data management in comparison to analogue technology, the position of the damper blade itself can be used to indicate the appropriate fan speed to meet demand.
This eliminates the need for the fan speed to be controlled by a pressure transducer, meaning that duct pressure does not have to be measured and maintained at an unnecessarily high set point. By contrast, as demand falls, both fan speed and pressure can fall together, following the characteristic curves of the devices, as shown in Figure 3.
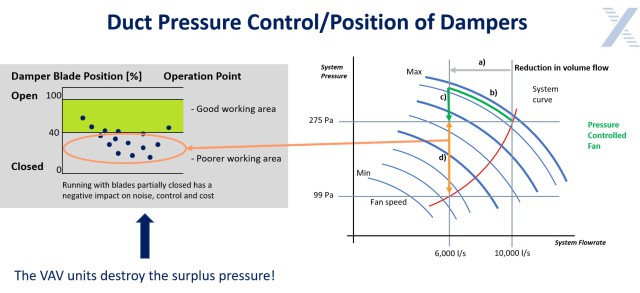
Energy savings, improved acoustics and easier commissioning
There are a number of advantages of this approach. Firstly, enabling the fan speed and pressure to reduce uniformly along the device’s characteristic curve harnesses the potential of the fan laws (power is proportional to rotary speed cubed: P α N3), reducing energy costs throughout the equipment’s lifecycle. Reducing the flow rate by 40% as shown in the examples here will result in a reduction in energy consumption of 78%, but the real-world energy saving then is dependent on demand generated by occupancy patterns. Installations employing this approach to date indicate that fan energy consumption can be reduced by around 45%.
Secondly, the damper blade position will be between 40% and 100% open at this lower pressure point, facilitating better control of the VAV units and improving acoustic performance.
Lastly, controlling fan speed in this way removes complexity during commissioning, avoiding the difficulties associated with the positioning of pressure transducers in the duct. This approach also provides a more stable control circuit on which to design and operate the system.
To deliver these benefits, the system must, of course, have controls capable of monitoring and acting upon the damper blade positioning data. A central BMS might fulfil this function, but could involve complex (and therefore expensive) bespoke programming. So, look instead for VAV systems/components which already incorporate, as standard, the capability to achieve these additional energy savings. A number of standard TROX products and solutions, for example, have resident, integrated control technology capable of fan speed optimisation without the need for bespoke BMS programming.
It can take a while to understand the full potential of technologies as they emerge. But now that digital control of VAV is in daily use, it is clear that there are valuable additional energy savings waiting to be unlocked by rethinking aspects of control methodology. The approach to fan speed optimisation described here is one such example, in which exploiting underutilised features can open up new functionality. By moving to this methodology for fan speed optimisation, utilising damper blade positioning, it is possible to deliver significantly improved environmental and acoustic performance, whilst simplifying commissioning and creating a more stable control circuit.
Ian Thomas is Product Technical Manager - Air Flow Controls at TROX UK
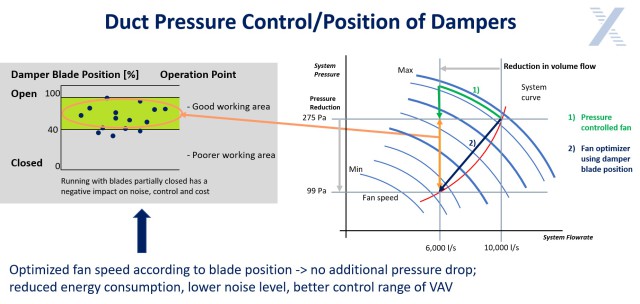