Why use gas: renewable methods of producing potable hot water
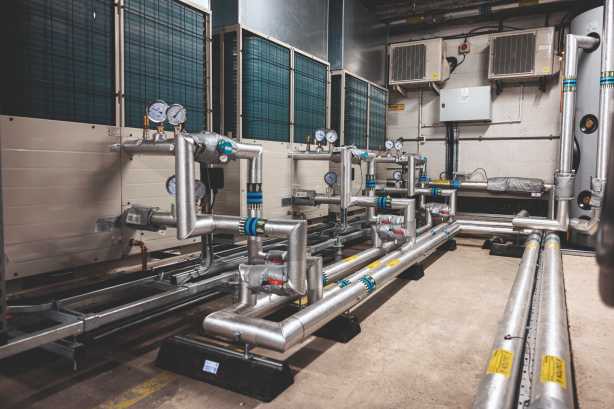
Harriet Evans, MHI Sales Director at Beijer Ref UK & Ireland, discusses why the requirement to produce potable hot water from renewable technologies shouldn’t be ignored.
In the drive to decarbonise our towns and cities, renewable technologies are making significant inroads into the supply of heat for commercial buildings.
The UK Government’s 10-point Plan for a Green Industrial Revolution highlighted the challenges of making buildings more energy-efficient by moving away from fossil fuel boilers, and heat pumps are often well equipped to meet the demands for space heating.
Delivering potable hot water to those same buildings, however, presents a different set of hurdles to overcome.
Improvements to the fabric and air-tightness of buildings, due in part to the impact of Building Regulation Part 2LA, Minimum Energy Efficiency Standards and building certification schemes such as BREEAM, mean that space heating loads are often reduced, while the hot water demand remains constant, leading to concerns over the potential environmental impact.
What is BREEAM?
BREEAM is the leading sustainability assessment method for planning projects, infrastructure and buildings. It recognises and reflects the value in higher performing assets across the built environment lifecycle, from new construction to in-use and refurbishment.
It does this through third party certification of the assessment of an asset’s environmental, social and economic sustainability performance, using standards developed by Building Research Establishment (BRE). BREEAM-rated developments are more sustainable environments that enhance the well-being of the people who live and work in them, help protect natural resources and make for more attractive property investments.
- 2 BREEAM points are awarded for using a refrigerant under GWP 10 (CO2 is <1).
- 1 BREEAM point is awarded for being a hermetically sealed system which minimises the risk of refrigerant leaks.
CO2 hot water generation
One of the main issues in replacing traditional fuels with heat pumps for potable hot water use is the maximum temperature achievable from a single stage refrigerant circuit. For R410 this is approximately 55°C, for R32 and R134a it is 65°C. This is generally at a system’s maximum operating capability with efficiency impacted accordingly.
Using natural refrigerant CO₂, which does not fall under F-Gas regulations, MHI’s Q-ton has been developed to produce hot water ranging from 60°C to 90°C even down to -25°C ambient, so when applied into commercial buildings requiring 70°C leaving water temperature to combat legionella, system efficiency is maintained. The ability to hold capacity to low ambient temperatures also helps with reducing capital costs by ensuring the kW capacity needed is supplied all year round without the need for electric immersion heater back-up.
Unlike systems using gas or oil, renewable heating systems are not usually designed for instantaneous hot water and so variation in design is required. A system incorporating a product such as the Q-ton needs to be designed to meet a building’s peak load. Using a method known as energy accumulation, the energy is generated, and a thermal store is used to hold the hot water until it is ready to be used.
Understanding profile
It is important to fully understand a building’s usage profile in order to design effectively, working on the basis that enough energy is required to meet peak load, but with enough heat pump capacity to replenish that energy before it is required again. This process is fluid, with the likelihood that water is being used in some aspect throughout most of the day. It is also important to consider any possible reductions in operating costs by designing a system to operate during periods of low electricity tariffs.
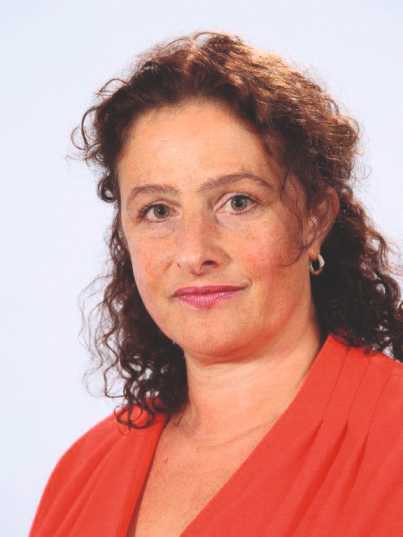
From a design perspective, the system needs to be capable of providing sufficient hot water between the thermal stores and the Q-ton together to meet demand of the absolute peak load. The Q-ton then needs to be able to heat enough water back to temperature from what has been used in order to meet the next peak with the process continuing throughout the day. Therefore the relationship between the volume of stored water and an the system kW capacity is based on the building’s usage pattern.
Heat pump products of this type lend themselves to both direct and indirect hydronic circuits, meaning that central circulation loops and secondary return loops are still serviceable. Specific hydronic system design is important, and has developed over years of research to make sure stratification of stored water is maintained to allow the water returning to the Q-ton to be as low as possible. This is important because CO₂ operates at discharge temperatures of around 110°C and high sided pressures of circa 10Mpa. Returning water temperature needs to be as low as possible to accommodate the high energy transfer taking place. Because of this, the system operates with a water ∆t of around 50°C.
Using a traditional heat pump system to achieve these leaving water temperatures would require a cascade system made up mostly of an air-to-water heat pump and a water-to-water heat pump, increasing capital expenditure and system complexity.
Future proof
Today’s commercial customers require solutions which offer both high efficiency and low carbon emissions. Improved efficiencies can be achieved through technologies such as two-stage CO₂ compressors that benefit performance at low ambient temperatures and direct energy exchange, meaning WRAS approval is key. This means there is no loss in capacity until -7°C because of vapour injection and remains operational to -25°C, providing hot water all year round and reducing capital costs.
The increasing emphasis on low global warming potential (GWP) refrigerants highlights the advantages or products such as CO₂ (R744), which has a GWP of 1 and an Ozone Depletion Potential of 0. As a naturally occurring refrigerant, CO₂ is used as a benchmark when comparing other refrigerants in terms of environmental impact.
With products like Q-ton holding the edge in commercial application due to high leaving water temperatures, low GWP refrigerants and the flexibility of a compact modular design, the transition to include space heating application has been the logical next step. With careful design, the accumulated energy can be used as required for heating circuits that maintain low returning water temperatures with simple blending, such as underfloor heating or low temperature radiators, whilst at the same time providing the energy for potable hot water use.
What is Part 2LA?
Building Regulation Part 2LA covers compliance for domestic and non-residential buildings, considering high efficiency alternative systems to improve the energy performance and in turn reduce CO₂ emissions. It sets minimum standards of performance of building services equipment and also sets the target emissions rate (TER). Compliance with Part L2A can be calculated using government approved methods such as SBEM (simplified building modelling), SAP (standard assessment procedure) and EPC (energy performance certificate).
Using SAP10.1 as a reference for g CO₂/kWh per fuel type, renewable technologies operating with a COP of 4.3 reduce annual CO₂ emissions by up to 76% compared to electric immersion heaters and 86% compared to gas boilers.
Harriet Evans is MHI Sales Director at Beijer Ref UK & Ireland