Preassembly: What lies ahead?
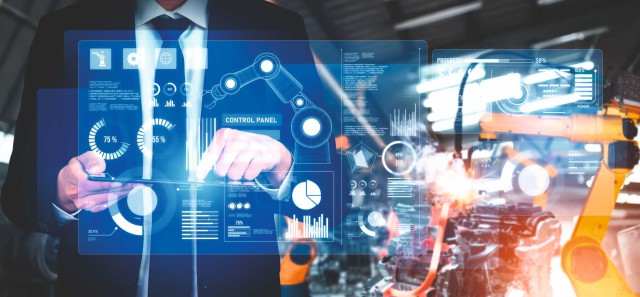
Adam Cafer, Advantage Technical Manager from Polypipe Building Services draws on preassembly’s benefits to articulate why it is here to stay.
Preassembly is on the rise in the construction industry. Its growing popularity doesn’t come as a surprise given the benefits it has to offer including consistent quality, greater flexibility and customisation, and less waste onsite. Preassembly is making everything simple, offering specifiers, contractors, installers and architects a solution that is driving efficiency across a project’s supply chain.
Greater control and productivity
Speed of installation, less labour-intensive, quality control; the benefits of offsite manufacturing to the commercial sector are wide-ranging. According to a paper titled ‘Modular construction: From projects to products’ published by McKinsey & Company, modular construction, also referred to as prefabrication or preassembly, can speed-up construction by as much as 50%.
Modern construction sites feature a number of challenges for contractors, not least of which are increasingly tight margins, quality control and space limitations, especially in built-up urban environments. Manufactured under factory-controlled conditions, every prefabricated system is delivered based on the exact specifications of the project, so there’s no waste and no need for additional labour to undertake assembly – saving even more space, time and money. This is welcome news considering offsite has been tipped to help provide a solution to an industry that has been plagued with low productivity even when project timeframes are getting tighter.
Skills gap
Offsite can further assist with other challenges within the industry including the labour and skills gap. With the industry experiencing both a shortage of skilled tradespeople and an ageing workforce, it is certainly assuring to rest in the knowledge that the likes of prefabrication can fill an important gap where it is needed. The high costs of skilled labour can be overlooked until they are required onsite. But with offsite manufacturing, these costs can’t be accrued as assembly is taken into a controlled manufacturing environment with rigorous quality control, and health and safety measures in place.
It’s not only the high cost of skilled labour that can be overlooked. The need for hired machinery can also escape attention. For instance, some large sites can take two years to install, and hiring equipment for this long period of time can come at a price. By utilising offsite manufacturing however, a reduced number of welding tools are required on site compared to a traditional installation. As a result, contactors don’t have to invest money in tooling or ongoing hiring costs.
Not only can preassembly provide a remedy to the skills shortage, it can assure the consistency and quality of manufacture that is nigh on impossible to replicate onsite. Offsite construction has an array of advantages over traditional build methods – speed of installation, fewer site workers and, perhaps most importantly of all, a higher quality finished product. Quality control has been a key focus in construction over the past few years. Changing regulations have placed greater responsibility on contractors to install systems that hit the mark on excellence. Creating products in a factory-controlled environment ticks a huge box in this respect; offering the consistent manufacture of systems that comply with and meet the high levels set by British Standards.
Quality control
Maintaining a high level of quality onsite can be difficult when traditional trades are employed – particularly on sites prone to inclement weather. Annual precipitation in the UK averages at around 133 days a year, which can cause disruption on construction sites. Utilising offsite manufacturing however means products are manufactured in a factory-controlled environment that isn’t exposed to the same weather conditions as traditional methods.
Not only is the project completed in less time, but it often yields a better result that hasn’t been potentially affected by the damages caused by rain, storm, or snow — something that a building owner may not learn until further down the line.
Minimise risk
Working in construction comes with its fair share of risks. Over the past decade or so, the industry has been putting a number of measures in place to improve safety for workers and mitigate risk. Whether it be operating heavy machinery, working at height, or handling dangerous materials, these risks have to be prevented to ensure health and safety remains uncompromised.
With offsite construction, there is less labour to be done onsite, reducing the number of injuries and health hazards. Studies show that traditional construction still has more serious and fatal injuries than manufacturing. The accident rates are 29% less for major injuries and 52% less for fatalities in manufacturing.
Furthermore, products tested in a manufacturing environment to a high-quality standard are less likely to experience problems including leaking. This can help contractors save on costs as they are not having to revisit the site after the final installation to fix any snags onsite, often disrupting the tenants.
Less waste
Sustainability continues to be a key pressure point for the construction and manufacturing industries. To put it simply, offsite manufacturing leaves fewer waste materials onsite, with the likes of Polypipe’s Advantage Service offering able to reuse and recycle materials that are cast away during the manufacturing process. More than just a fabrication service, Polypipe Advantage is an end-to-end solution for the UK commercial market. Devised by Polypipe Building Services, the Advantage Service supports construction teams from design and planning to ordering, delivery, technical support and customer service, to simplify complex processes.
In the manufacturing area, all pipework is cut to the size specified on a customer’s drawings. Any cut-offs are repurposed for other jobs. A process such as this ensures every piece of material is used to create an alternative product or recycled into the next line. This streamlined approach not only minimises the amount of waste created, generally, it makes everything that little bit more efficient. Furthermore, completed drainage SVPs are delivered on wooden stillages which can be recycled or returned back to Polypipe Building Services, further reducing waste onsite.
This pays in dividends for contractors onsite where traditionally extra sums of money would have to be paid to remove the waste. A solution such as the Advantage Service, therefore, delivers precisely what customers need and nothing more, with no spare parts or unnecessary extras to dispose of.
Offsite manufacturing and preassembly are making huge differences to construction projects. Not only is prefabrication ensuring contractors and the like can meet ever tighter deadlines, manufacturers can create and supply systems to the highest standard, guaranteeing compliance in the process. All of these products pass through rigorous testing before being delivered to site. Prefabrication is, thus, offering contractors the flexibility and speed they need for projects to excel. It’s streamlining what were once onsite inefficiencies and boosting productivity in key areas too. With such clear benefits on offer, utilising preassembly is simply a no brainer.
Adam Cafer is Advantage Technical Manager at Polypipe Building Services